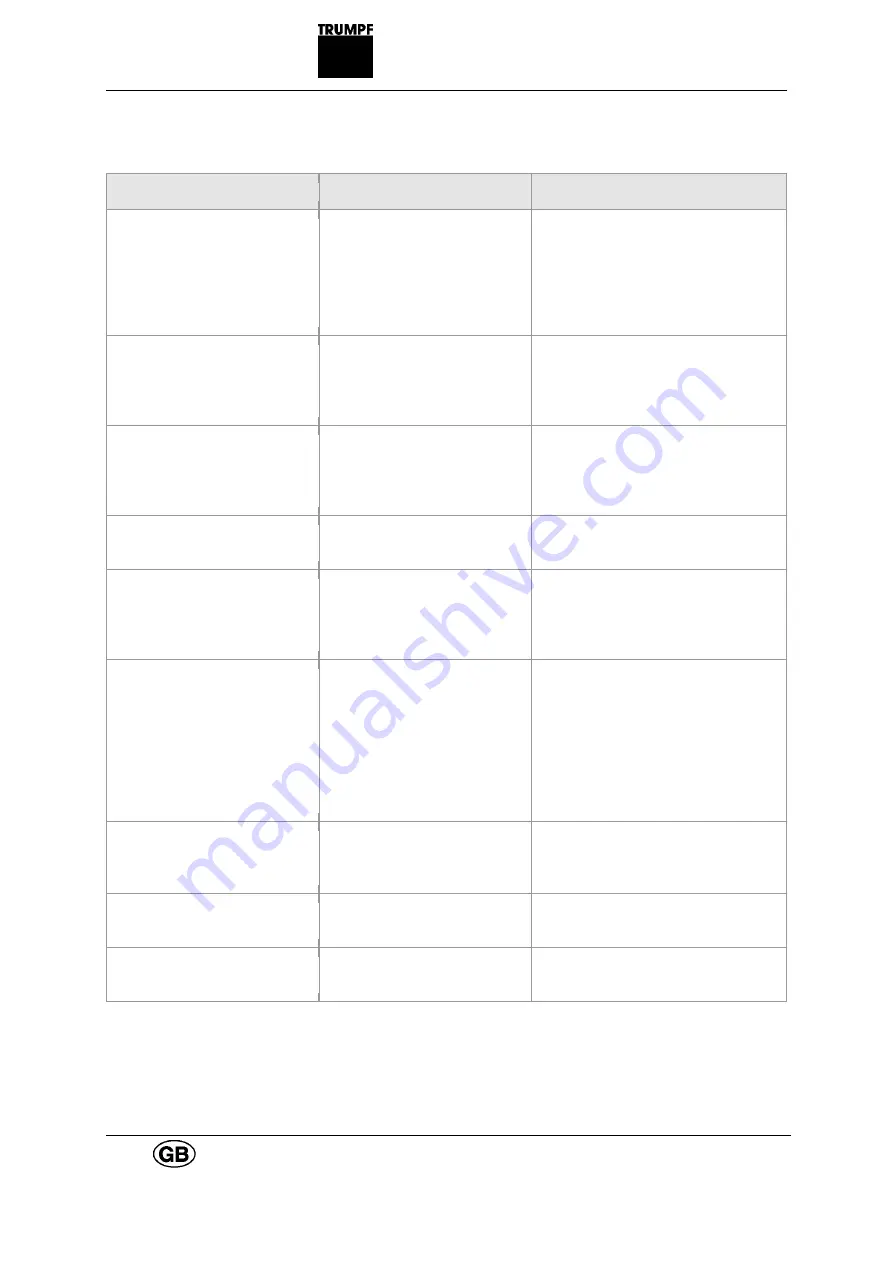
6. Troubleshooting
Malfunction
Cause
Remedial
action
Grinding takes longer than 5 min.
• Hydraulic oil is too cold
• Let machine warm up
• Throttle valve setting is wrong
• Set cycle time
• Dirt in hydraulic system
• Let hydraulic cylinder run
with throttle valve open,
then return to original setting
(cycle time 3 1/2 - 4 1/2 min)
Green pin is not visible after
• Cam does not reverse
• Inspect the hydraulic hoses
grinding is completed
• Air in hydraulic system
• Inspect the pressure relief valve
• Pressure at relief valve too low
(22
+4
bar), install an external
pressure
gauge
Grinding does not start, nothing is
• Wrong setting of locating
• Adjust locating stop and setting screw
ground off
stop and screw
• Required clearance between bottom of
• During setup, the locating stop
grinding wheel and top of stop:
did not come to rest on the tool
0.1 mm
Grinding motor stops, cannot be
Motor overload due to excessive
Release the brake with screwdriver
switched on again
grinding pressure
SW6, raise the top, set cycle time
Rotary tool holder < 20 min
-1
Dirt or air in hydraulic system
• Remove and clean the cover on the
drive/rotary tool holder
• Check hydraulic lines for air leaks,
Inspect the pressure relief valve
Grinding wheel is "burning"
• Grinding wheel is blunt
• Sharpen the grinding wheel
(smoking), loud grinding noises,
• Grinding pressure too high
• Set cycle time to 3 1/2 - 4 1/2 min
rough grinding effect
• Grinding coolant not directed at
• Adjust the grinding coolant tubes
grinding wheel
Distance to wheel face: 1 mm
• No grinding coolant flow
• Too little grinding coolant in
• Add grinding coolant
container
• Intake filter clogged
• Clean intake filter
Grinding coolant and hydraulic oil
• Air is being drawn in, the line
• Inspect all lines for leaks
are frothing in the container
has a leak
• Fluid level is too low
• Fill container up
The fixture is pulled off the rotary
Fixture not properly clamped onto
Push clamping jaws upward, make sure
tool holder during grinding
the rotary tool holder
the diameter of the fixture is 150
h11
There is no intake of grinding
Intake hoses are bent
Position the hoses correctly, replace
coolant and hydraulic oil
them if necessary
18
quicksharp
B60E
Summary of Contents for quicksharp
Page 1: ...q u i c k s h a r p D K D G B F E I N L...
Page 2: ......
Page 4: ...Operator s manual quicksharp 06 2000...
Page 22: ...Manuel op rateur quicksharp 06 2000...
Page 40: ...Manual de operaci n quicksharp 06 2000...
Page 58: ...Ersatzteilliste Spare parts list Liste de pi ces de rechange quicksharp 06 2000...
Page 63: ...6 Avant de poursuivre B60EL...
Page 88: ...Fig 24493 B60EL Ersatzteilliste Spare parts list Liste de pi ces de rechange 31...
Page 89: ...Fig 24426 32 Ersatzteilliste Spare parts list Liste de pi ces de rechange B60EL...
Page 91: ...Fig 24427 34 Ersatzteilliste Spare parts list Liste de pi ces de rechange B60EL...
Page 93: ...36 Ersatzteilliste Spare parts list Liste de pi ces de rechange B60EL...
Page 95: ......