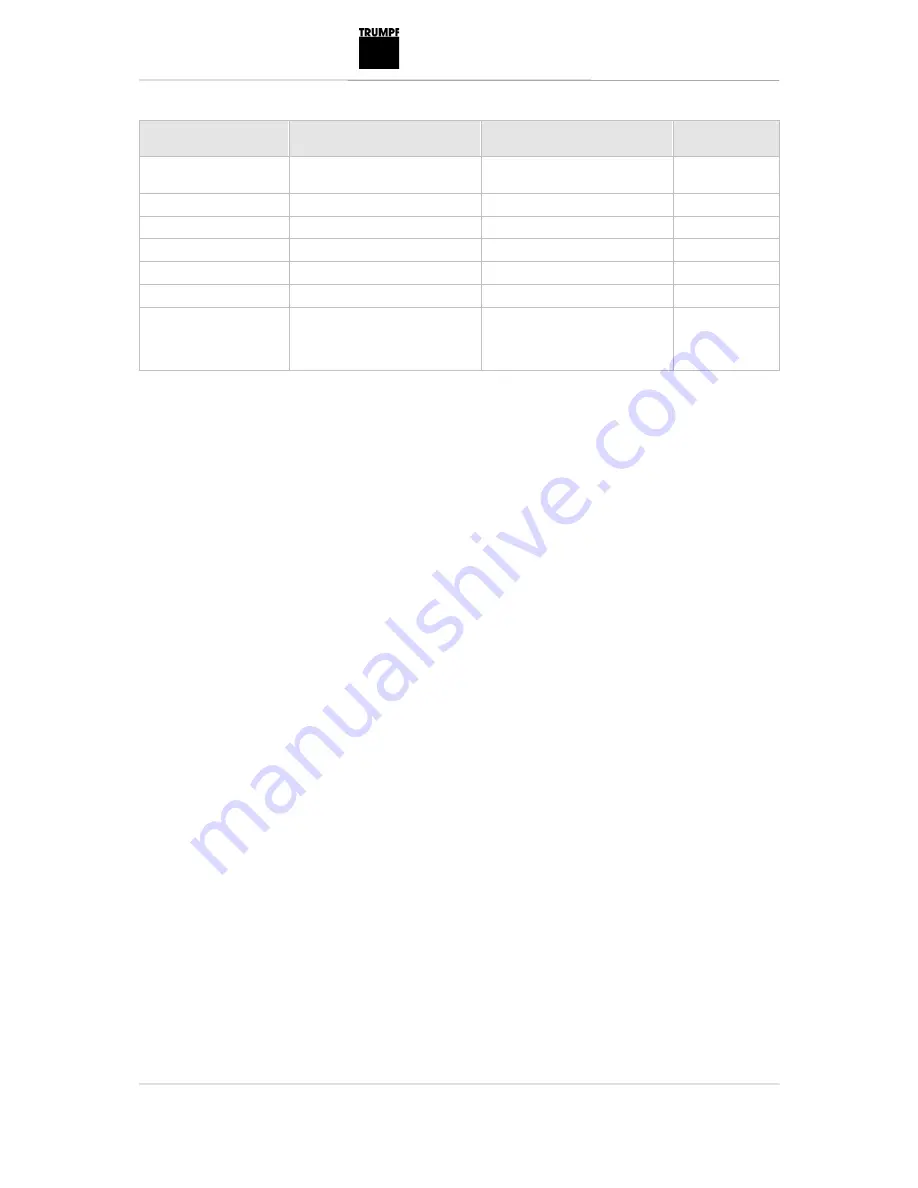
E528EN_03.DOC
Maintenance
17
Maintenance point
Procedure and interval
Recommended lubricants
Material No.
Lubricants
Punch, die and wearing
parts
Check hourly
-
-
Punch and die carrier
With each tool change
-
-
Punch
Regrind/replace as needed
-
-
Ventilation slot/grid
Clean as needed
-
-
Die
Replace as necessary
-
-
Wearing plate
Replace as necessary
-
-
Gearbox and
gear head (2)
After 300 operating hours,
arrange for a trained specialist
to relubricate or to replace the
lubricating grease.
"G1" lubricating grease
139440
Maintenance points and maintenance intervals
Tab. 6