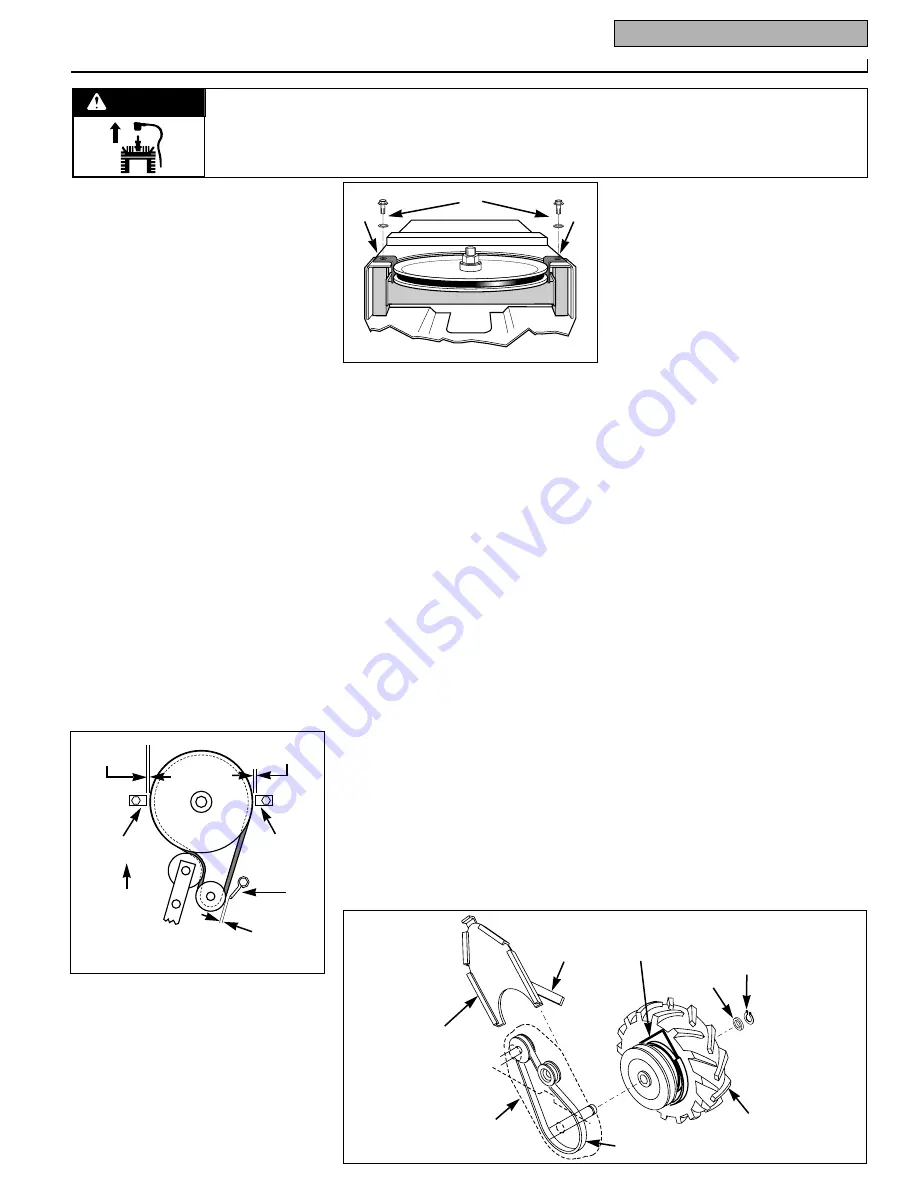
Section 5: Maintenance
21
Before inspecting, cleaning or servicing the machine, shut off engine, wait for all moving parts to
come to a complete stop, disconnect spark plug wire and move wire away from spark plug. Remove
the key from the keyswitch on units so equipped.
Failure to follow these instructions can result in serious personal injury or property damage.
WARNING
1. Stop the engine, wait for all moving
parts to come to a complete stop, discon-
nect the spark plug wire and prevent it
from contacting the spark plug.
2. Remove the hair pin cotters securing
the upper ends of the control rods to the
plastic thumb latches and wheel drive con-
trol levers (see J, Fig. 2-5).
3. Thread the rods in or out of the idler
arm (A, Fig. 5-2) as needed. Adjust each
wheel drive control rod (A, Fig. 5-3) until
there is a 1-1/4" (32mm) gap between the
rod and the plastic thumb latch. Adjust
both control rods evenly.
4. Re-install the hair pin cotters on the
outside of the wheel drive levers.
CUTTER BAR DRIVE BELT
REMOVAL/REPLACEMENT
Replace the cutter bar drive belt if it is
cracked, severely frayed, or worn to the
point where proper tension can no longer
be applied by the spring loaded idler.
1. Stop the engine, wait for all moving
parts to come to a complete stop, discon-
nect the spark plug wire and prevent it
from contacting the spark plug.
2. Put the cutter bar lever in the OFF posi-
tion (Fig. 4-7). Reach up underneath the
unit and remove the belt from the small
lower pulley (Fig. 5-4).
3. Remove screws and washers (B, Fig. 5-
5) and both belt guides (A). Remove the
belt from the large pulley.
4. Install new belt as shown in Fig. 5-4.
5. Reinstall belt guides (A, Fig. 5-5) and
screws and washers (B). Adjust the guides
1/16" - 1/8" (1.6-3.2mm) away from belt.
CUTTER BAR BELT GUIDE
ADJUSTMENT
1. Stop the engine, wait for all moving
parts to come to a complete stop, discon-
nect the spark plug wire and prevent it
from contacting the spark plug.
2. Place the belt under tension (Fig. 4-7)
by moving the cutter bar lever to the ON
position.
3. Adjust front belt guides (Y, Fig. 5-4)
1/16"—1/8" (1.6—3.17 mm) away from
belt.
4. Secure guides.
5. Adjust the right rear belt guide (Z) 1/4"
(6.35 mm) from the belt (Fig. 5-4).
6. Secure the guide.
WHEEL DRIVE BELT
ADJUSTMENT
Poor wheel traction can result if the belt
tension spring (B, Fig. 5-2) has loosened,
or if the wheel drive belt has worn.
To Adjust Wheel Belt Tension:
1. Move the end of spring (B, Fig. 5-2),
located on the underside of the deck, to
the lower hole (C).
2. If the belt tension is still too loose, the
spring or the belt may need replacing.
WHEEL DRIVE BELT
REMOVAL/REPLACEMENT
When a wheel drive belt is frayed, broken
or worn to the point where tension can no
longer be controlled with the idler pulley,
the belt or spring must be replaced.
NOTE: Prop the unit up by placing sturdy
supports under the engine deck.
To Remove the Wheel Drive Belt:
1. Remove drive belt cover (A, Fig. 5-6).
2. Remove snap ring (B) and washer (C)
from drive axle.
3. Remove wheel assembly (F).
4. Slip the drive belt off the pulleys and
off the unit.
To Replace the Wheel Drive Belt:
1. Slide wheel assembly (F, Fig. 5-6) onto
axles. Note that seal tabs (AA) fit inside
the belt guard (J).
2. Route belt (E) into place around pulley
on wheel assembly (F).
3. Secure wheel with washer (C) and snap
ring (B) removed earlier.
4. Install drive belt cover assembly (A).
Note that finger (H) on drive belt cover
points toward the front of the unit.
WHEEL DRIVE BELT GUIDE
ADJUSTMENT
1. Place belt under tension by engaging
wheel drive clutch lever. See Fig. 4-5.
2. Remove Drive Belt Cover (A, Fig. 5-6).
3. Adjust belt guide (A, Fig. 5-7) to 1/16”
(1.6mm) or less away from belt.
4. Adjust belt guide (B) 1/4” (6.4mm)
away from pulley (D).
5. Tighten belt guide (B) at bolt (C) after
adjusting.
6. Install belt cover (A, Fig. 5-6).
A
A
B
Fig. 5-5
A
H
J
E
F
C
B
AA
Fig. 5-6
1/16"-1/8"
(1.6-3.2mm)
1/4"
(6.4mm)
FRONT
Fig. 5-4
Y
Y
Z
1/16"-1/8"
(1.6-3.2mm)