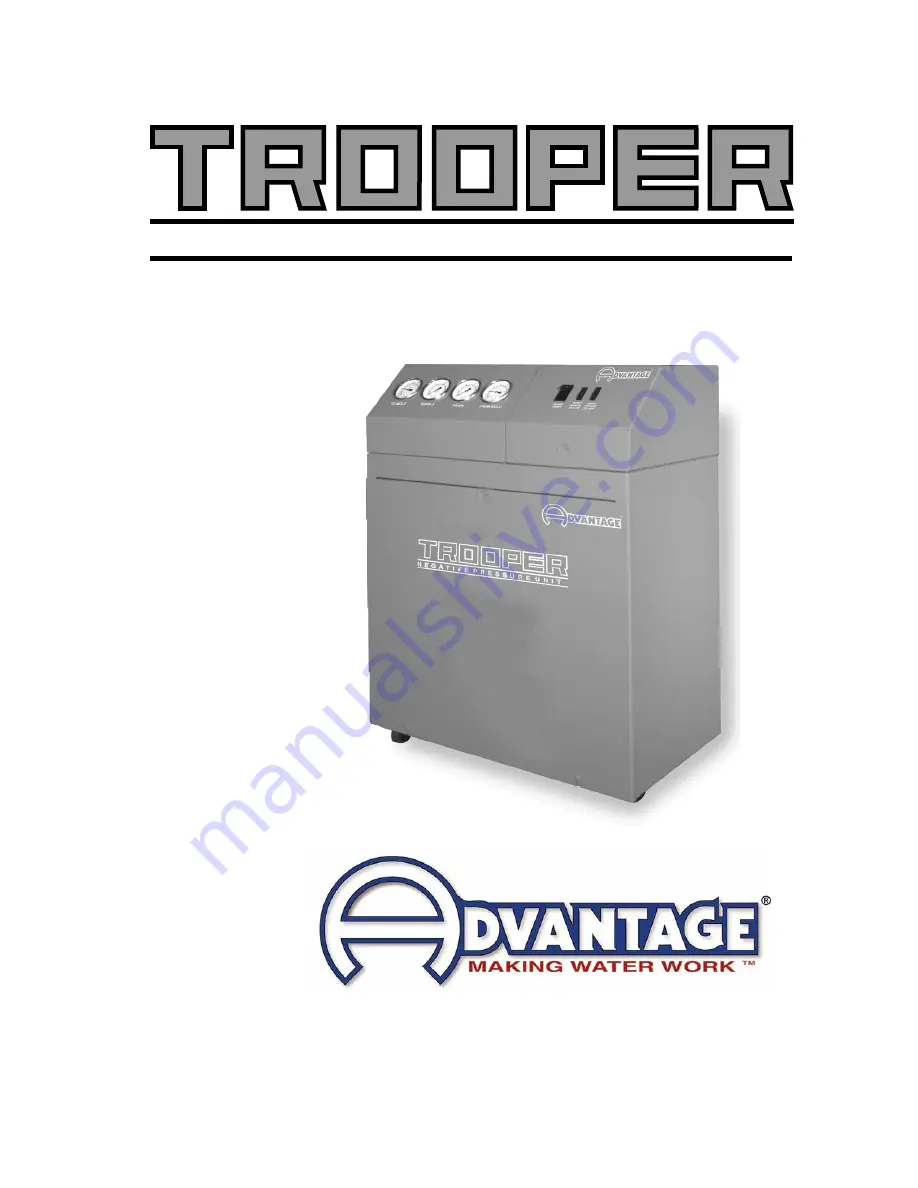
N E G A T I V E P R E S S U R E U N I T
TM
I.O.M. #08A 9/95 updated 11/13
INSTRUCTION MANUAL
• INSTALLATION • OPERATION • MAINTENANCE
ADVANTAGE ENGINEERING, INC.
525 East Stop 18 Road Greenwood, IN 46142
317-887-0729 fax: 317-881-1277
Service Department fax: 317-885-8683
www.AdvantageEnegineering.com
e-mail: [email protected]