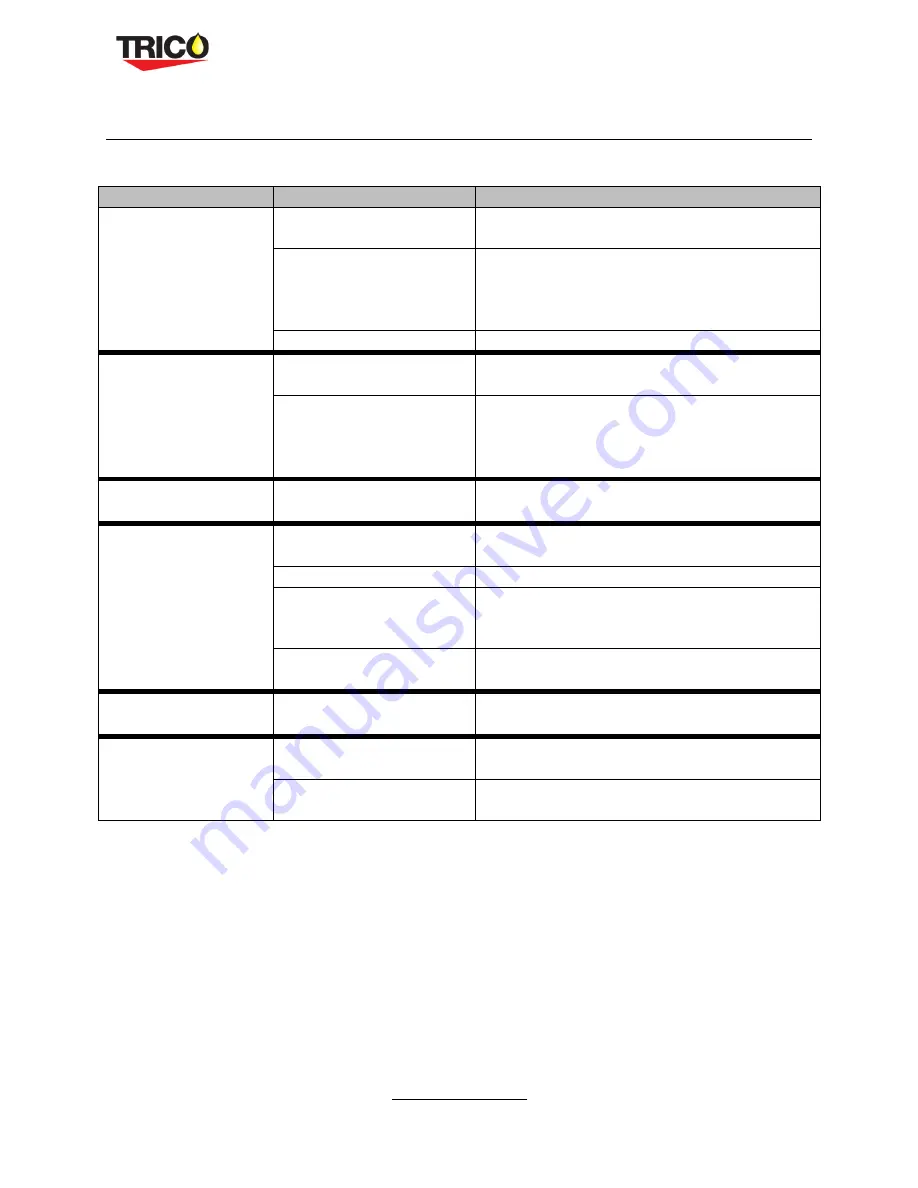
Spectrum Essential Oil Storage System
TRICO CORPORATION
1235 Hickory Street; Pewaukee, WI 53072
For Customer Support: 800-558-7008
P a g e
16 | 20
TROUBLESHOOTING
The following troubleshooting guide gives issues, causes, and corrective action. If any of these actions do
not solve the issue entirely, please contact Trico for additional support.
Symptom
Possible Cause(s)
Corrective Action
Pump system does not
prime
Suction wand above liquid
Ensure open end of suction wand remains
completely below surface of liquid
Clogged suction wand
and/or discharge hose line
and/or manifold valves are
closed
Clean suction wand and/or discharge hose line
and/or open manifold valves
Suction wand line too long Reduce length in suction line to reduce pressure
Insufficient flow
Clogged/ kinked discharge
hose line or nozzle
Remove and flush discharge hose line and
nozzle, inspect for damage
Fluid viscosity exceeds
recommended viscosity for
motor
Check viscosity of fluid at temperature. See SUS
vs. Temp. chart or contact fluid supplier. If
viscosity exceeds maximum cSt, fluid must be
warmed to reduce viscosity
Fluid Leaking from
manifold or any fittings
Loose fittings and/or
connections
Check tightness of hose/fitting connections
Electric motor does not
function/ or stops
working
Power On/Off switch not
fully switched
Check On/Off switch
No power to receptacle
Check outlet for power and breaker
Unit has overheated
tripping internal overload
breaker
Turn unit power to the “OFF” position, allow
motor to cool, turn back to “ON” position and
resume filling
Unit generates excessive
heat
Fluid viscosity exceeds maximum recommended
viscosity
Tank is not filling
Tank Manifold Valve is
closed
Open Correct Tank Manifold Valve
Tank is not dispensing
fluid
Tank Shut-Off Valve is
closed
Open Tank Shut-Off Valve below the tank to
have gravity feed for the Dispensing Nozzle
Dispensing Nozzle is
clogged
Clean Dispensing Nozzle to remove
contamination or clogs