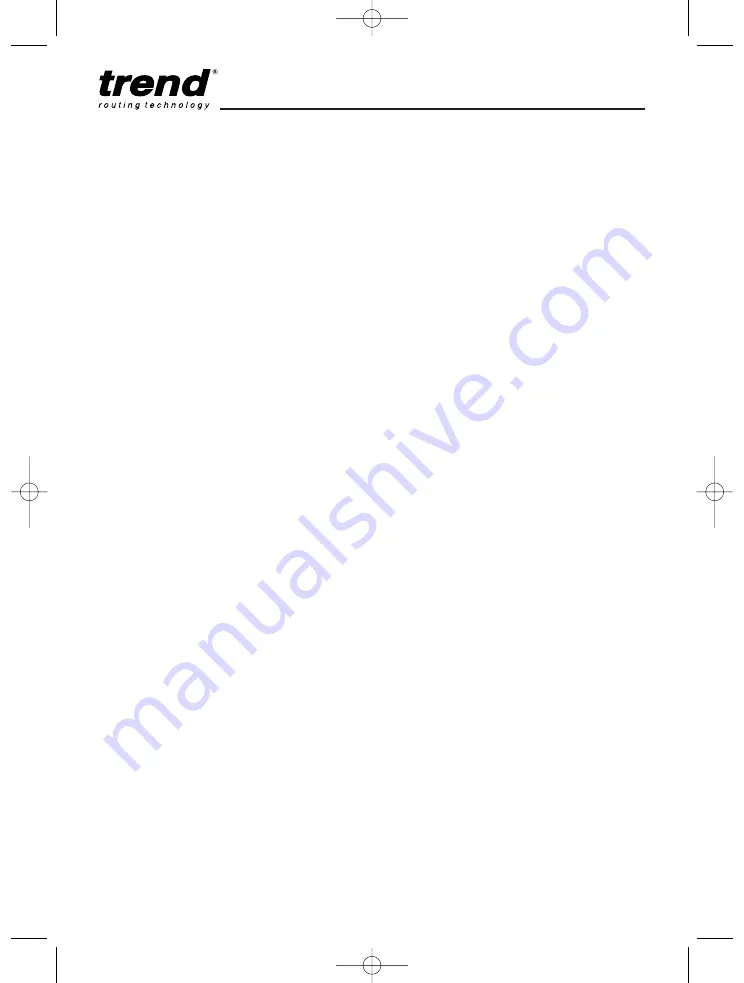
T4
-3-
6.
Respiratory protection. Wear a face
or dust mask, or powered respirator.
Dust masks/filters should be changed
regularly.
7.
Do not switch router on with the cutter
touching the workpiece. At the end of
the cut, release the router plunge and
allow spindle to stop rotating. Never
use the spindle lock as a brake
8.
The direction of routing must always
be opposite to the cutter's direction of
rotation. Do not back-cut or climb-cut.
9.
Check before cutting that there are no
obstructions in the path of the router.
Ensure there are no obstacles
beneath workpiece when cutting full
thickness, and that a sacrificial work
surface is used.
Router Cutter Safety
1.
Cutting tools are sharp. Care should
be taken when handling them. Do not
drop cutters or knock them against
hard objects. Handle very small
diameter cutters with extra care.
Always return cutter to its packaging
after use.
2.
Always use cutters with a shank
diameter corresponding to the size of
the collet installed in your tool.
3.
The maximum speed (n.max) marked
on the tool, or in instructions or on
packaging shall not be exceeded.
Where stated the speed range shall
be adhered to. Recommended speeds
are shown in the Trend Routing
Catalogue and/or website.
4.
Always use router cutters in a router.
Drill and boring bits must not be used
in a router. Router cutters must only
be used for the material cutting
application for which they are
designed. Do not use on metal or
masonry.
5.
Never use cutters with a diameter
exceeding the maximum diameter
indicated in the technical data of the
powertool or attachment used.
6.
Before each use check that the cutting
tool is sharp and free from damage.
Do not use the cutting tool if it is dull,
broken or cracked or if in any other
damage is noticeable or suspected.
7.
Cutters should be kept clean. Resin
build up should be removed at regular
intervals with Resin Cleaner
®
. The
use of a PTFE dry lubricant will
reduce resin build up. Do not use
PTFE spray on plastic parts.
8.
When using stacked tooling (multi-
blade, block and groover etc.) on a
spindle arbor, ensure that the cutting
edges are staggered to each other to
reduce the cutting impact.
9.
Cutter shanks should be inserted into
the collet all the way to the line
indicated on the shank. This ensures
that at least
3
⁄
4
of the shank length is
held in the collet. Ensure clamping
surfaces are cleaned to remove dirt,
grease, oil and water.
10.
Observe the correct assembly and
fitting instructions in the router
instruction manual for fitting the collet,
nut and cutter.
11.
Tool and tool bodies shall be clamped
in such a way that they will not
become loose during operation. Care
shall be taken when mounting cutting
tools to ensure that the clamping is by
the shank of the cutting tool and that
the cutting edges are not in contact
with each other or with the clamping
elements.
12.
It is advisable to periodically check
the collet and collet nut. A damaged,
worn or distorted collet and nut can
cause vibration and shank damage.
Do not over-tighten the collet nut
13.
Do not take deep cuts in one pass;
take several shallow or light passes to
reduce the side load applied to the
cutter and router. Too deep a cut in
one pass can stall the router.
15.
In case of excessive vibrations whilst
using the router stop immediately and
have the eccentricity of the router,
router cutter and clamping system
checked by competent personnel
15.
All fastening screws and nuts should
be tightened using the appropriate
spanner or key and to the torque
value provided by the manufacturer.
16.
Extension of the spanner or
tightening using hammer blows shall
not be permitted.
17.
Clamping screws shall be tightened
according to instructions provided by
the manufacture. Where instructions
are not provided, clamping screws
shall be tightened in sequence from
the centre outwards.
Using Routers In A Fixed Position
1.
Attention should be made to the
HSE’s Safe Use of Vertical Spindle
Moulding Machines Information Sheet
No.18 and any revisions.
2.
After work, release the router plunge
to protect the cutter.
3.
Always use a push-stick or push-block
when making any cut less than
300mm in length or when feeding the
last 300mm of the cut.
4.
The opening around the cutter should
be reduced to a minimum using
suitably sized insert rings in the table
and closing the back fence cheeks or
fitting a false fence on the back fence.
5.
Whenever possible use a work
holding device or jig to secure
component being machined. Ensure
any attachment is securely fitted to the
workbench, with table surface at
approximately hip height.
6.
Use a No-Volt Release Switch. Ensure
it is fixed securely, easily accessible
and used correctly.
7.
In router table (inverted) mode, stand
to the front right of the table. The
cutter will rotate anti-clockwise when
viewed from top so the feed direction
is from the right (against the rotation of
the cutter). In overhead mode, stand
to the front left of the machine table
and the feed direction is from the left.
8.
Do not reach underneath table or put
your hands or fingers at any time in
the cutting path while tool is connected
to a power supply.
9.
Never thickness timber between the
back of the cutter and the backfence.
Useful Advice When Routing
1.
Judge your feed rate by the sound of
the motor. Feed the router at a
constant feed rate. Too slow a feed
rate will result in burning.
2.
Trial cuts should be made on waste
material before starting any project.
3.
When using some attachments e.g. a
router table or dovetail jig, a fine
height adjuster is recommended.
4.
When using a template guide bush,
ensure there is sufficient clearance
between cutter tip and inside edge of
bush and that it cannot come into
contact with collet and nut. Ensure
cutter and guide bush are concentric.
Router Cutter Repair/Maintenance
1.
Repair of tools is only allowed in
accordance with the manufacturers
instructions.
3.
The design of composite (tipped) tools
shall not be changed in process of
repair. Composite tools shall be
repaired by a competent person i.e. a
person of training and experience, who
has knowledge of the design
requirements and understands the
levels of safety to be achieved.
4.
Repair shall therefore include, e.g. the
use of spare parts which are in
accordance with the specification of
the original parts provided by the
manufacturer.
5.
Tolerances which ensure correct
clamping shall be maintained.
6.
Care shall be taken that regrinding of
the cutting edge will not cause
weakening of the body and the
connection of the cutting edge to the
body.
Version 7.1 06/006
MANU/T4 v2.0 30/8/07 1:08 pm Page 3