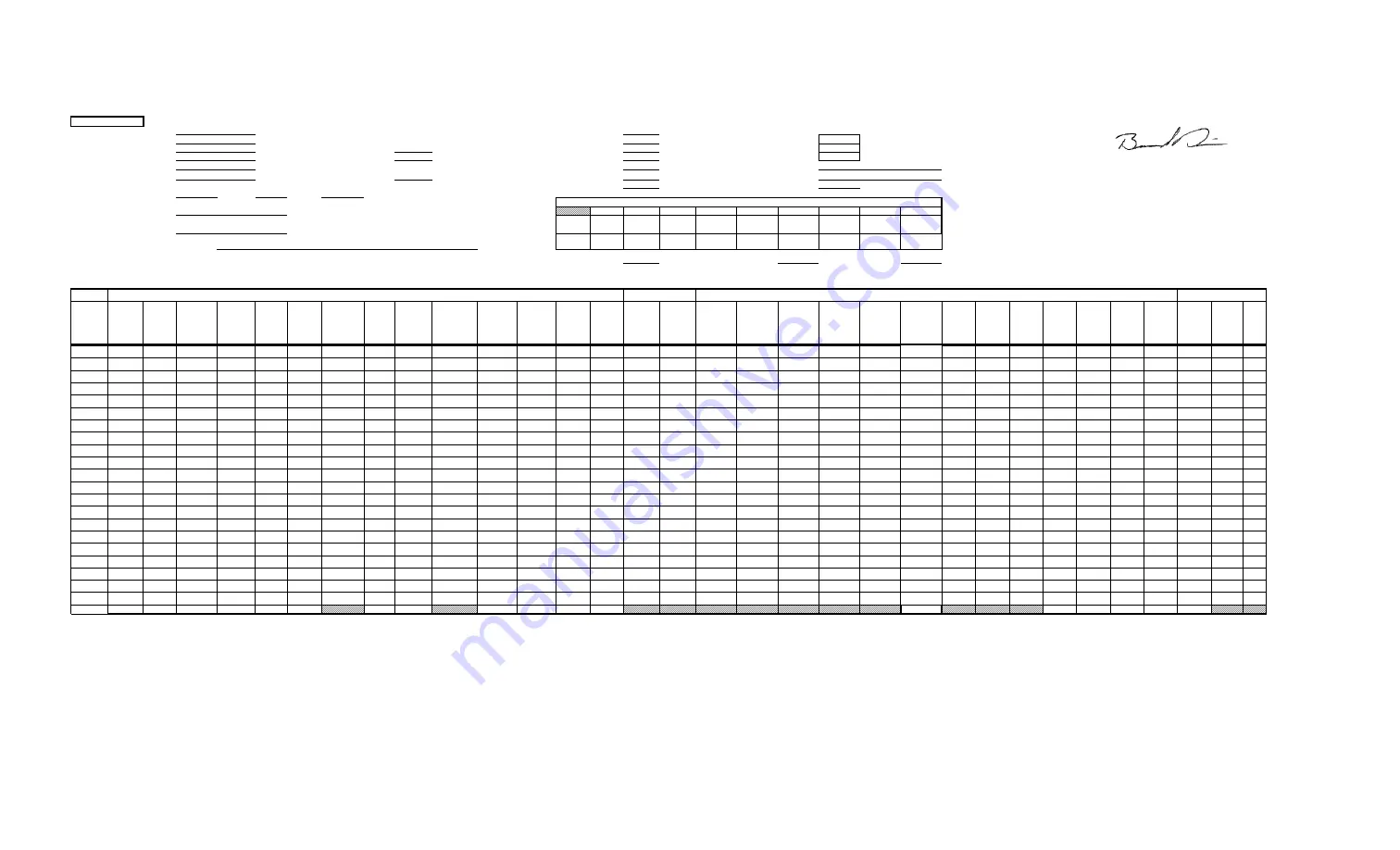
OMNI-Test Laboratories, Inc.
Run:
2
Travis Industries
PM Control Modules:
371, 372
Medium Flushwood
Dilution Tunnel MW(dry):
29.00 lb/lb-mole
Avg. Tunnel Velocity:
14.91
ft/sec.
2301
550
min
Dilution Tunnel MW(wet):
28.78 lb/lb-mole
Initial Tunnel Flow:
197.1
scfm
Technician Signature:________________________________
0028WN118E
Recording Interval:
10
min
Dilution Tunnel H2O:
2.00 percent
Average Tunnel Flow:
163.0
scfm
31-Jul-18
Dilution Tunnel Static:
-0.210
"H2O
Post-Test Leak Check (1):
0.000
cfm @
8
in. Hg
Beginning Clock Time:
11:30
Background Sample Volume:
cubic feet
Tunnel Area:
0.19635
ft2
Post-Test Leak Check (2):
0.000
cfm @
6
in. Hg
Pitot Tube Cp:
0.99
Average Test Piece Fuel Moisture:
23.11
Dry Basis %
Meter Box Y Factor:
0.983
(1)
0.974
(2)
(Amb)
Barometric Pressure:
Begin
Middle
End
Average
Pt.1
Pt.2
Pt.3
Pt.4
Pt.5
Pt.6
Pt.7
Pt.8
Center
30.05
29.96
30.01 0
Initial dP
0.060
0.074
0.080
0.070
0.060
0.080
0.078
0.074
0.080
"H2O
OMNI Equipment Numbers:
Temp:
113
113
113
113
112
112
112
112
112
°F
V
strav
18.57
ft/sec
V
scent
19.47
ft/sec
F
p
0.954
Particulate Sampling Data
Elapsed
Time (min)
Gas
Meter 1
(ft
3
)
Gas
Meter 2
(ft
3
)
Sample
Rate 1
(cfm)
Sample
Rate 2
(cfm)
Orifice
dH 1
("H
2
O)
Meter 1
Temp
(°F)
Meter 1
Vacuum
("Hg)
Orifice
dH 2
("H
2
O)
Meter 2
Temp (°F)
Meter 2
Vacuum
("Hg)
Dilution
Tunnel (°F)
Dilution
Tunnel
Center dP
Pro. Rate
1
Pro. Rate
2
Scale
Reading
Weight
Change Firebox Top
Firebox
Bottom
Firebox
Back
Firebox Left
Firebox
Right
Avg. Stove
Surface
Catalyst
Exit
Stack
Filter 1
Dryer
Exit 1
Filter 2
Dryer
Exit 2
Ambient
Draft
("H
2
O)
CO
2
(%)
CO
(%)
Wood Heater Test Data
Emissions and Efficiency Data
Test Date:
Stack Gas Data
Fuel Weight (lb)
Temperature Data (°F)
Velocity Traverse Data
Manufacturer:
Model:
Tracking No.:
Total Sampling Time:
Project No.:
Export to
350
57.689
60.908
0.17
0.18
2.26
93
-0.71
60.91
60.908
60.908
97
0.060
94
92
1.0
-0.1
333
122
167
299
272
239
398
181
86
79
87
80
87
-0.024
6.52
-0.01
360
59.369
62.681
0.17
0.18
2.26
93
-0.99
62.68
62.681
62.681
96
0.060
94
92
0.9
-0.1
329
121
165
292
267
235
394
178
86
80
87
80
86
-0.023
6.44
-0.01
370
61.050
64.457
0.17
0.18
2.28
93
-0.65
64.46
64.457
64.457
96
0.050
103
100
0.8
-0.1
322
120
163
284
262
230
384
176
86
71
87
67
87
-0.021
6.11
-0.01
380
62.730
66.234
0.17
0.18
2.26
93
-0.75
66.23
66.234
66.234
96
0.050
103
100
0.7
-0.1
315
119
160
278
255
225
374
172
86
68
87
62
88
-0.021
6.13
-0.01
390
64.407
68.011
0.17
0.18
2.25
93
-0.89
68.01
68.011
68.011
96
0.050
103
100
0.6
-0.1
307
119
159
272
249
221
366
169
86
66
87
62
88
-0.021
5.97
-0.01
400
66.086
69.789
0.17
0.18
2.25
94
-1
69.79
69.789
69.789
96
0.050
103
99
0.5
-0.1
302
118
157
266
244
217
358
166
86
66
87
62
89
-0.020
5.96
-0.01
410
67.763
71.569
0.17
0.18
2.25
94
-0.97
71.57
71.569
71.569
95
0.050
103
99
0.4
-0.1
296
118
155
261
238
214
350
162
85
66
86
63
87
-0.020
5.88
-0.01
420
69.440
73.349
0.17
0.18
2.26
94
-0.84
73.35
73.349
73.349
95
0.050
103
99
0.3
-0.1
288
117
154
256
232
209
343
159
85
67
86
65
88
-0.019
5.71
-0.01
430
71.118
75.130
0.17
0.18
2.25
94
-0.68
75.13
75.13
75.13
95
0.050
103
99
0.3
0
280
116
152
250
226
205
332
156
85
68
86
66
88
-0.019
5.4
-0.01
440
72.795
76.911
0.17
0.18
2.27
94
-0.82
76.91
76.911
76.911
95
0.050
103
98
0.2
-0.1
270
116
150
242
220
200
320
153
85
69
86
68
87
-0.018
4.97
-0.01
450
74.305
78.694
0.15
0.18
2.27
94
-0.65
78.69
78.694
78.694
94
0.050
92
98
0.2
0
264
115
148
234
213
195
310
149
85
69
86
70
87
-0.017
5.01
-0.01
460
76.151
80.476
0.18
0.18
2.25
94
-0.66
80.48
80.476
80.476
94
0.050
113
98
0.1
-0.1
262
115
148
234
213
194
309
149
85
69
86
71
87
-0.017
5.03
-0.01
470
77.829
82.260
0.17
0.18
2.26
94
-0.66
82.26
82.26
82.26
93
0.050
103
97
0.1
0
254
115
146
226
207
190
300
145
85
70
85
72
87
-0.016
5.01
-0.01
480
79.509
84.043
0.17
0.18
2.26
93
-0.97
84.04
84.043
84.043
93
0.050
103
97
0.1
-0.03
247
114
144
219
201
185
290
141
85
71
85
73
86
-0.015
4.96
-0.01
490
81.187
85.828
0.17
0.18
2.26
93
-0.96
85.83
85.828
85.828
92
0.050
103
97
0.1
-0.01
240
113
142
213
196
181
280
136
85
72
85
74
86
-0.013
4.69
0.04
500
82.866
87.609
0.17
0.18
2.25
92
-0.8
87.61
87.609
87.609
91
0.050
103
96
0.1
-0.01
232
112
140
206
191
176
266
132
85
73
85
74
86
-0.012
4.3
0.23
510
84.545
89.391
0.17
0.18
2.26
92
-0.81
89.39
89.391
89.391
90
0.050
103
96
0.0
-0.01
222
112
137
199
185
171
246
127
84
73
85
75
85
-0.011
3.88
0.51
520
86.223
91.172
0.17
0.18
2.26
91
-0.66
91.17
91.172
91.172
89
0.050
103
95
0.0
-0.01
212
111
135
192
179
166
227
119
85
74
85
75
84
-0.010
3.91
0.69
530
87.900
92.952
0.17
0.18
2.25
91
-0.7
92.95
92.952
92.952
89
0.050
103
95
0.0
-0.01
201
110
133
185
173
160
212
112
84
74
84
75
83
-0.008
4.05
0.73
540
89.577
94.732
0.17
0.18
2.26
90
-0.99
94.73
94.732
94.732
88
0.050
103
94
0.0
-0.01
191
110
131
177
167
155
200
106
84
75
84
75
81
-0.006
4.26
0.76
550
91.255
96.513
0.17
0.18
2.26
90
-0.65
96.51
96.513
96.513
87
0.050
103
94
0.0
-0.01
181
108
128
170
161
150
190
101
84
75
83
76
80
-0.005
4.3
0.75
Avg/Tot
91.255
96.513
0.17
0.18
2.22
90
47.93
48
99
0.053
100
100
220.4
73
86
72
84
-0.038
Control No. P-SSAR-0003
Page 4 of 7
Run 2-Low_10-min
71 of 236
Summary of Contents for Medium Flush Wood Hybrid Fyre Insert
Page 4: ...Section 1 Sampling Procedures and Test Results 4 of 236 ...
Page 11: ...Section 2 Photographs Appliance Description Drawings 11 of 236 ...
Page 16: ...Run 4 Test Fuel Run 4 Test Fuel Load Run 4 Remaining Coal After Test 16 of 236 ...
Page 18: ...Engineering Drawings Blueprints K List 18 of 236 ...
Page 19: ...19 of 236 ...
Page 20: ...20 of 236 ...
Page 21: ...21 of 236 ...
Page 22: ...22 of 236 ...
Page 23: ...23 of 236 ...
Page 24: ...24 of 236 ...
Page 25: ...25 of 236 ...
Page 26: ...26 of 236 ...
Page 27: ...27 of 236 ...
Page 28: ...28 of 236 ...
Page 29: ...29 of 236 ...
Page 30: ...30 of 236 ...
Page 31: ...31 of 236 ...
Page 32: ...32 of 236 ...
Page 33: ...33 of 236 ...
Page 34: ...34 of 236 ...
Page 35: ...35 of 236 ...
Page 36: ...36 of 236 ...
Page 37: ...37 of 236 ...
Page 38: ...38 of 236 ...
Page 39: ...39 of 236 ...
Page 40: ...40 of 236 ...
Page 41: ...41 of 236 ...
Page 43: ...Section 3 Test Data by Run 43 of 236 ...
Page 50: ...Run 1 High Burn 1 minute data Emissions Results Cold to Hot Cycle 50 of 236 ...
Page 59: ...59 of 236 ...
Page 60: ...60 of 236 ...
Page 69: ...Run 2 Low Burn 69 of 236 ...
Page 76: ...76 of 236 ...
Page 77: ...77 of 236 ...
Page 78: ...Run 3 Non Particulate Sampling High Burn 78 of 236 ...
Page 82: ...82 of 236 ...
Page 83: ...Run 4 Medium High Burn 83 of 236 ...
Page 91: ...91 of 236 ...
Page 92: ...92 of 236 ...
Page 93: ...Section 4 Quality Assurance Quality Control 93 of 236 ...
Page 96: ...Flush Wood Plus Quality Assurance Manual 96 of 236 ...
Page 104: ...104 of 236 ...
Page 105: ...105 of 236 ...
Page 106: ...106 of 236 ...
Page 107: ...107 of 236 ...
Page 108: ...108 of 236 ...
Page 109: ...109 of 236 ...
Page 110: ...110 of 236 ...
Page 111: ...111 of 236 ...
Page 112: ...112 of 236 ...
Page 113: ...113 of 236 ...
Page 114: ...114 of 236 ...
Page 115: ...115 of 236 ...
Page 116: ...116 of 236 ...
Page 117: ...117 of 236 ...
Page 118: ...118 of 236 ...
Page 119: ...119 of 236 ...
Page 120: ...120 of 236 ...
Page 121: ...121 of 236 ...
Page 122: ...122 of 236 ...
Page 123: ...123 of 236 ...
Page 124: ...124 of 236 ...
Page 125: ...125 of 236 ...
Page 126: ...126 of 236 ...
Page 127: ...127 of 236 ...
Page 128: ...128 of 236 ...
Page 129: ...129 of 236 ...
Page 130: ...130 of 236 ...
Page 131: ...131 of 236 ...
Page 132: ...132 of 236 ...
Page 133: ...133 of 236 ...
Page 134: ...134 of 236 ...
Page 135: ...135 of 236 ...
Page 136: ...136 of 236 ...
Page 137: ...137 of 236 ...
Page 138: ...138 of 236 ...
Page 139: ...139 of 236 ...
Page 140: ...140 of 236 ...
Page 141: ...141 of 236 ...
Page 142: ...142 of 236 ...
Page 143: ...143 of 236 ...
Page 144: ...144 of 236 ...
Page 145: ...145 of 236 ...
Page 146: ...146 of 236 ...
Page 147: ...147 of 236 ...
Page 148: ...148 of 236 ...
Page 149: ...149 of 236 ...
Page 150: ...150 of 236 ...
Page 151: ...Sample Analysis Analysis Worksheets Tared Filter Probe and O Ring Data 151 of 236 ...
Page 152: ...152 of 236 ...
Page 153: ...153 of 236 ...
Page 154: ...154 of 236 ...
Page 155: ...155 of 236 ...
Page 156: ...156 of 236 ...
Page 157: ...157 of 236 ...
Page 159: ...159 of 236 ...
Page 160: ...160 of 236 ...
Page 161: ...161 of 236 ...
Page 162: ...162 of 236 ...
Page 165: ...7 20 18 165 of 236 ...
Page 168: ...7 20 18 168 of 236 ...
Page 169: ...169 of 236 ...
Page 170: ...170 of 236 ...
Page 171: ...171 of 236 ...
Page 173: ...173 of 236 ...
Page 174: ...174 of 236 ...
Page 175: ...Example Calculations 175 of 236 ...
Page 187: ...Section 5 Labeling Owner s Manual 187 of 236 ...
Page 227: ...Listing Information 39 Travis Industries 4 27 2021 1496 Med Flush Wood Insert Listing Label ...
Page 229: ...Appendix A Alt 125 E3053 Letter ...
Page 233: ...Appendix B Design Change Request ...
Page 234: ......