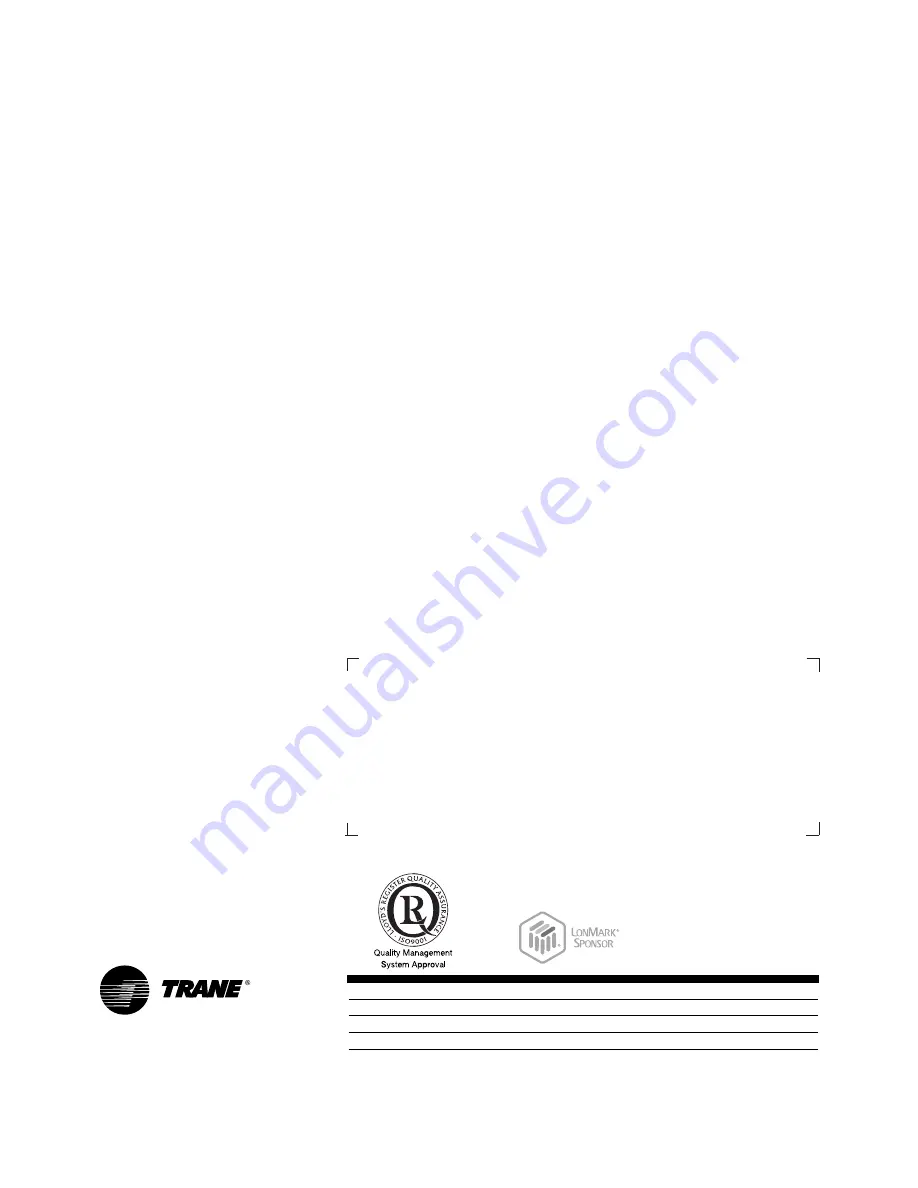
The manufacturer has a policy of continuous
product improvement, and reserves the right
to alter any details of the products at any time
without notice.
This publication is a general guide to install,
use and properly maintain our products. The
information given may be different from the
specification for a particular country or for a
specific order. In this event, please refer to
your nearest office.
Safety recommendations
To avoid accidents and damage, the
following recommendations should
be observed during maintenance
and service visits:
1. The maximum allowable
pressures for system leak testing
on low and high pressure side are
given in the chapter “Installation”.
Always provide a pressure
regulator.
2. Disconnect the main supply
before any servicing on the unit.
3. Service work on the refrigeration
system and the electrical system
should be carried out only by
qualified and experienced
personnel.
Maintenance contract
It is strongly recommended that you
sign a maintenance contract with
your local Service Agency. This
contract provides regular
maintenance of your installation by
a specialist in our equipment.
Regular maintenance ensures that
any malfunction is detected and
corrected in good time and
minimizes the possibility that
serious damage will occur. Finally,
regular maintenance ensures the
maximum operating life of your
equipment. We would remind you
that failure to respect these
installation and maintenance
instructions may result in immediate
cancellation of the warranty.
Training
The equipment described in this
manual is the result of many years
of research and continuous
development. To assist you in
obtaining the best use of it and
maintaining it in perfect operating
condition over a long period of time,
the manufacturer has at your
disposal a refrigeration and air
conditioning service school. The
principal aim of this is to give
operators and technicians a better
knowledge of the equipment they
are using, or that is under their
charge. Emphasis is particularly
given to the importance of periodic
checks on the unit operating
parameters as well as on preventive
maintenance, which reduces the cost
of owning the unit by avoiding
serious and costly breakdown.
American Standard Europe BVBA
Registered Office: 1789 Chaussée de Wavre, 1160 Brussels - Belgium
www.trane.com
For more information contactyour local district
office or e-mail us at [email protected]
Trane has a policy of continuous product and product data improvement and reserves the right to
change design and specifications without notice. Only qualified technicians should perform the
installation and servicing of equipment referred to in this publication.
For additional information, contact:
Distributor/Installer stamp
Literature Order Number
CG-SVU01B-E4
Date
0304
Supersedes
CG-SVU01A-E4-0902
Stocking Location
Europe
Summary of Contents for TRACER CH532
Page 1: ...TRACER CH532 Chiller controller User guide CG SVU01B E4...
Page 29: ...CG SV01B E4 29 Notes...
Page 30: ...30 CG SV01B E4 Notes...
Page 31: ...CG SV01B E4 31 Notes...