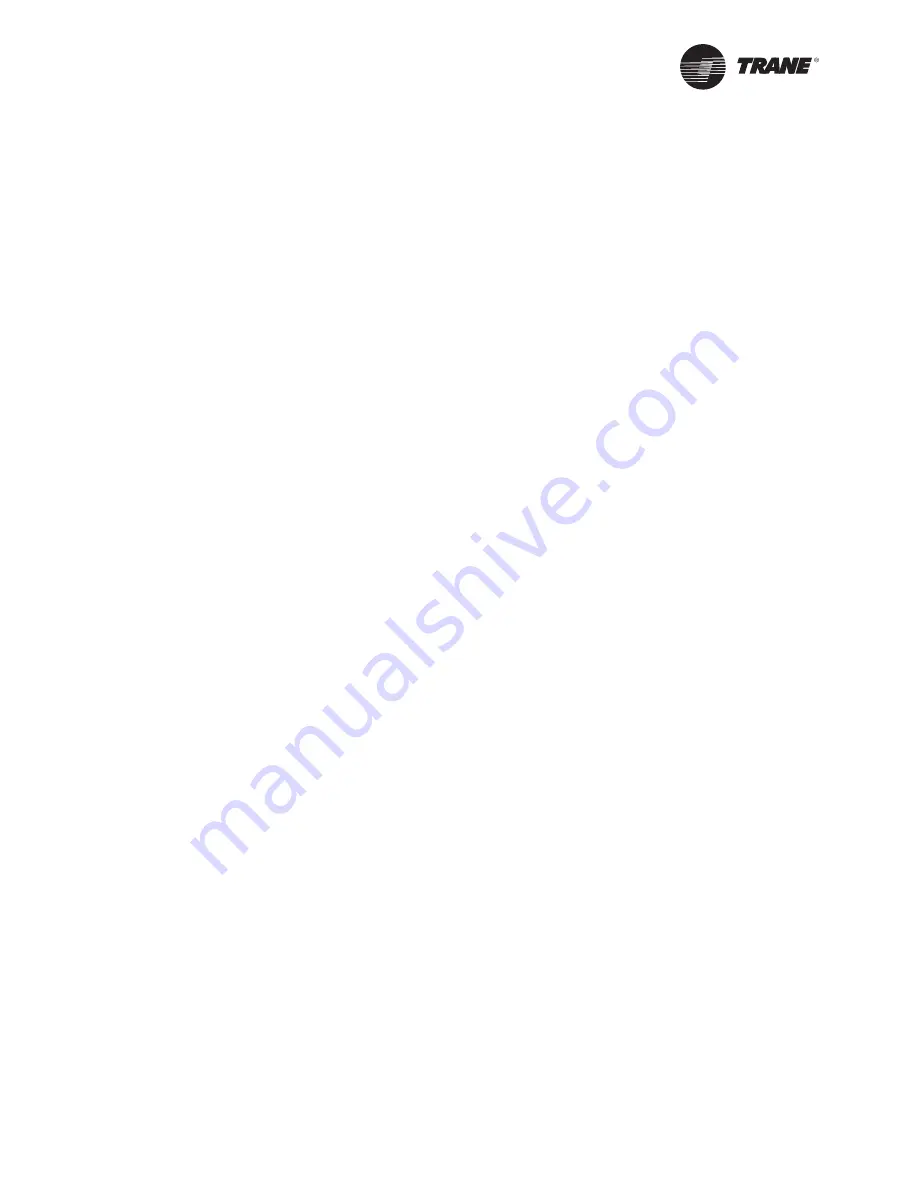
RLC-SVX14H-GB
95
Oil analysis
Trane Oil Analysis is a predictive tool used to detect
minor issues before they become major problems. It
also reduces failure detection time and allows planning
for appropriate maintenance. Oil changes can be
reduced by half resulting in lower operating costs and a
lower impact on the environment.
Vibration analysis
Vibration analysis is required when oil analysis reveals
the presence of wear indicating the start of possible
bearing or motor failure. Trane oil analysis has the
ability to identify the type of metallic particles in the oil
which, when combined with the vibration analysis, will
clearly point out the failing components.
Vibration analysis should be performed on a regular
basis to build a vibration trend of the equipment and
avoid unplanned downtime and costs.
Compressor R’newal
To ensure a long lifetime for Trane compressors, system
oil and vibration are regularly analyzed. These tests
build a detailed picture of the condition of internal
system components. Over time, they also help build a
`wear trend’ of the equipment. This informs our service
experts whether your compressor is due for minor
maintenance or a complete overhaul.
System upgrade
This Service provides a consulting service.
Upgrading your equipment will increase the unit
reliability and can reduce the operating costs
by optimizing the controls A list of solutions /
recommendations to the system will be explained to the
customer Actual upgrade for the system will be costed
separately.
Water treatment
This Service provides all of the necessary chemicals
to properly treat each water system for the period
designated.
The inspections will be conducted at agreed upon
intervals and Trane Service First will submit a written
report to the customer after each inspection.
These reports will indicate any corrosion, scaling, and
alga growth in the system.
Refrigerant analysis
This Service includes a thorough analysis for
contamination and solution upgrade.
It is recommended that this analysis be performed every
six months.
Annual cooling tower maintenance
This Service includes the inspection and maintenance of
the cooling tower at least once a year.
This involves checking the motor.
24 hours duty
This service includes emergency calls outside of the
offi ce normal working hours.
This Service is only available with a Maintenance
Contract, where available.
Trane Select Agreements
Trane Select Agreements are programs tailored to
your needs, your business and your application. They
offer four different levels of coverage. From preventive
maintenance plans to fully comprehensive solutions,
you have the option of selecting the coverage that best
suits your requirements.
5 years motor-compressor warranty
This Service will provide a 5 years part and labor
warranty for the motor compressor only.
This Service is only available for units covered by a
5 years Maintenance Contract.
Tube analysis
- Eddy Current Tube Testing for prediction of tube failure/
wear
- Frequency - every 5 years for fi rst 10 years (depending
on the water quality), then every 3 years thereafter.
Energy enhancement
With Trane Building Advantage you can now explore
cost effective ways to optimize the energy effi ciency of
your existing system and generate immediate savings.
Energy management solutions are not only for new
systems or buildings. Trane Building Advantage offers
solutions designed to unlock energy savings in your
existing system.
Additional services