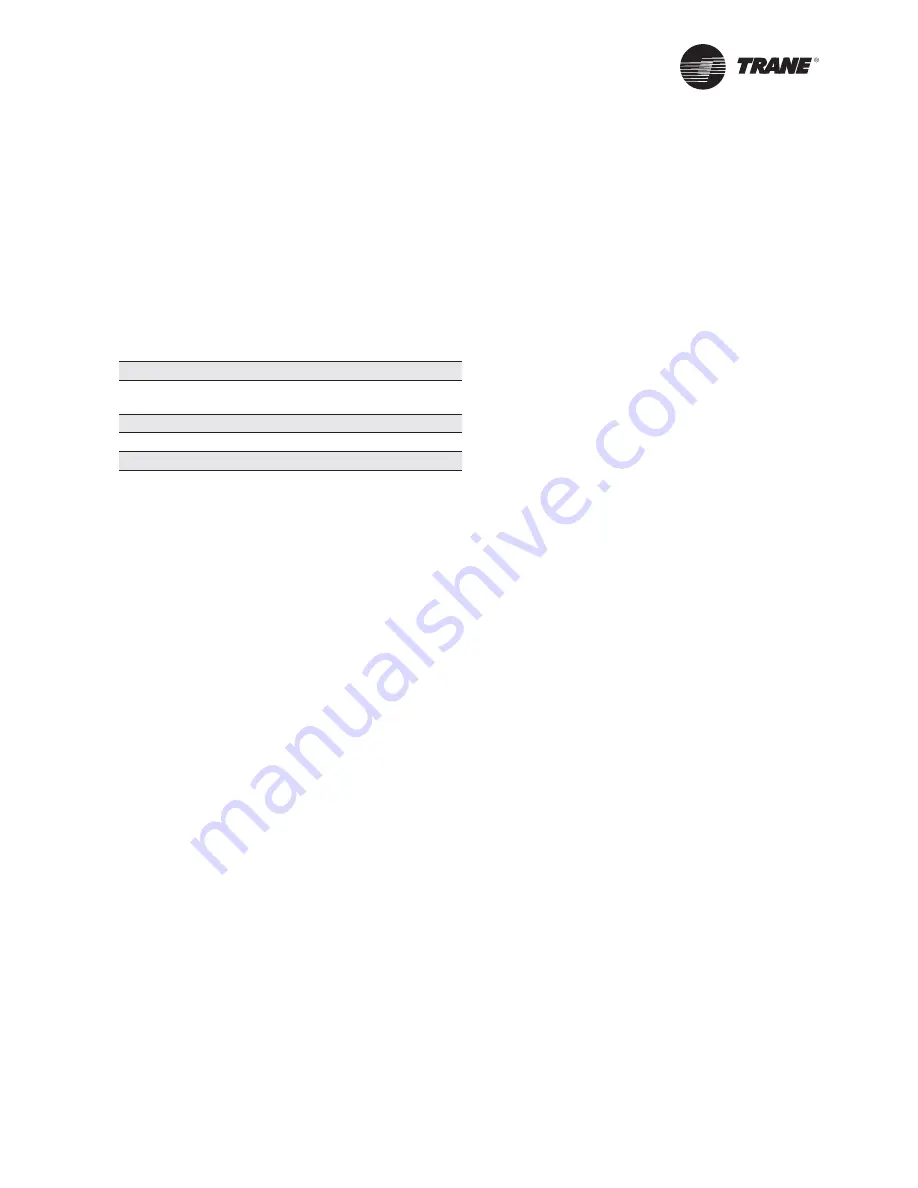
RLC-SVX14H-GB
85
All conditions stated above are based on the unit running
fully loaded, running at Eurovent.
•
If full load conditions can not be met. Refer to note
below to trim the refrigerant charge
Note: Conditions at minimum must be: entering
condenser water: 29°C and entering evaporator water:
13°C
Table 26 - Operating Conditions at Minimum Load for
R134a
Description
Condition
Evaporator approach
Less than 4°C
(non glycol applications)*
Condensing approach
Less than 4°C*
Subcooling
1-16°C
EXV percent open
10-20% open
* approximately 0.5°C for new unit.
Annual Maintenance
Shut down the chiller once each year to check the
following:
WARNING
Hazardous Voltage!
Disconnect all electric power, including remote
disconnects and discharge all motor start/run capacitors
before servicing. Follow proper lockout/tagout procedures
to ensure the power cannot be inadvertently energized.
Verify with an appropriate voltmeter that all capacitors
have discharged. Failure to disconnect power and
discharge capacitors before servicing could result in
death or serious injury.
RTWD HSE version
•
Time before to work on the electrical panel of the unit:
once the AFD is off (confi rmed by the extinction of the
display), it is mandatory to wait one minute before
working on the electrical panel.
•
However, for any intervention in the AFD, the indicated
time on the label of the AFD must be respected.
•
Perform all weekly and monthly maintenance
procedures.
•
Check the refrigerant charge and oil level. Refer to
“Maintenance Procedures”. Routine oil changing is
not necessary on a hermetic system.
•
Have a qualifi ed laboratory perform an oil analysis to
determine system moisture content and acid level.
Note: Due to the hygroscopic properties of the POE oil,
all oil must be stored in metal containers. The oil will
absorb water if stored in a plastic container.
•
Check the pressure drop across the oil fi lter. Refer to
“Maintenance Procedures”.
•
Contact a qualifi ed service organization to leak check
the chiller, to inspect safety controls, and inspect
electrical components for defi ciencies.
•
Inspect all piping components for leakage and/or
damage. Clean out any inline strainers.
•
Clean and repaint any areas that show signs of
corrosion.
•
Test vent piping of all relief valves for presence of
refrigerant to detect improperly sealed relief valves.
Replace any leaking relief valve.
•
Inspect the condenser tubes for fouling; clean if
necessary. Refer to “Maintenance Procedures”.
•
Check to make sure that the crank case heater is
working.
Scheduling Other Maintenance
•
Use a nondestructive tube test to inspect the
condenser and evaporator tubes at 3- year intervals.
Note: It may be desirable to perform tube tests on these
components at more frequent intervals, depending
upon chiller application. This is especially true of critical
process equipment.
•
Depending on chiller duty, contact a qualifi ed service
organization to determine when to conduct a complete
examination of the unit to determine the condition of
the compressor and internal components.
Note: Do not swap R134a by R1234ze without
intervention of Trane Service organization for advice
on technical changes.
Service and Maintenance