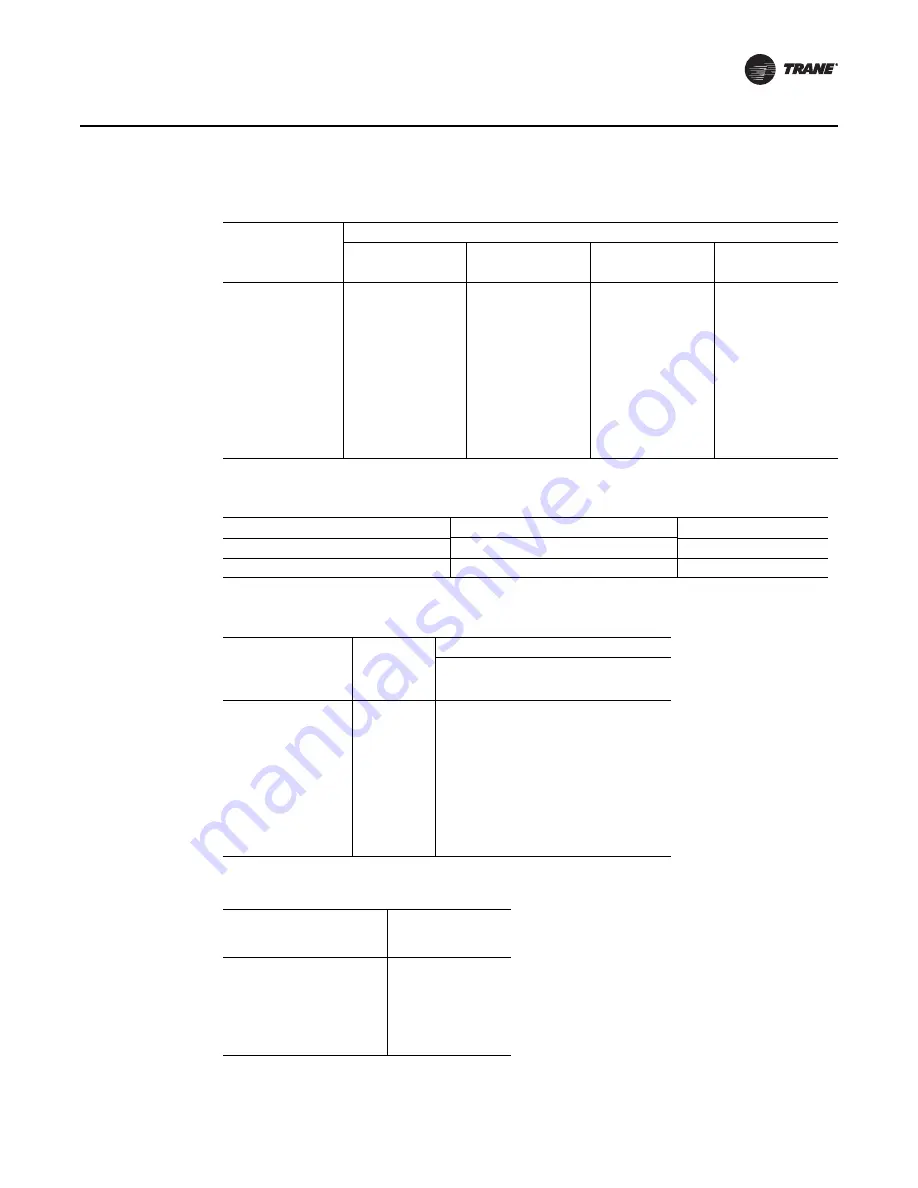
RT-SVX36G-EN
73
Installation
Table 23. Electrical service sizing data —electric heat module (electric heat units only) —
20-130 tons
Voltage
200
FLA
230
FLA
460
FLA
575
FLA
Module kW
30
83.3
72.2
36.1
28.9
50
138.8
120.3
60.1
48.1
70
194.3
168.4
84.2
67.4
90
249.8
216.5
108.3
86.6
110
305.3
264.6
132.3
105.9
130
156.4
125.1
150
180.4
144.3
170
204.5
163.6
190
228.5
182.8
Note:
Electric heat FLA are determined at 208, 240, 480 and 600 volts.
Table 24. Electrical service sizing data evaporative condenser - All tonnages (24-89T)
Condenser Fan
Sump Pump
Sump Heater
Qty
HP
FLA
Qty
HP
FLA
kW
FLA
1
5.4
5.9
1
0.5
1.55
3
3.8
Table 25. Electrical service sizing data — control power transformer
heating and cooling modes — 20-130 tons
Nominal Tons
(Air-cooled/
Evaporative
condensing)
Digit 2
Unit
Function
Voltage
200
230
460
575
20,25,30/24,29,36
A,E,L,S,X
1
1
1
1
20,25,30/24,29,36
F
4
3
2
1
40,50,55,60/48,59,73
A,E,L,S,X
3
2
1
1
40,50,55,60/48,59,73
F
5
4
2
2
70,75/80,89
A,E,L,S,X
5
4
2
2
70,75/80,89
F
8
7
3
3
90,105,115,130
E,L,S,X
5
4
2
2
90,105,115,130
F
8
7
3
3
Table 26. Electrical service sizing data — crankcase heaters
(heating mode on 460/575 volt only) — 20-130 tons
Nominal Tons
(Air-cooled/
Evaporative condensing)
(Add) FLA
20-30/24-36
1
40-60/48-73
2
70-75/80-89
3
90-105
3
115-130
4