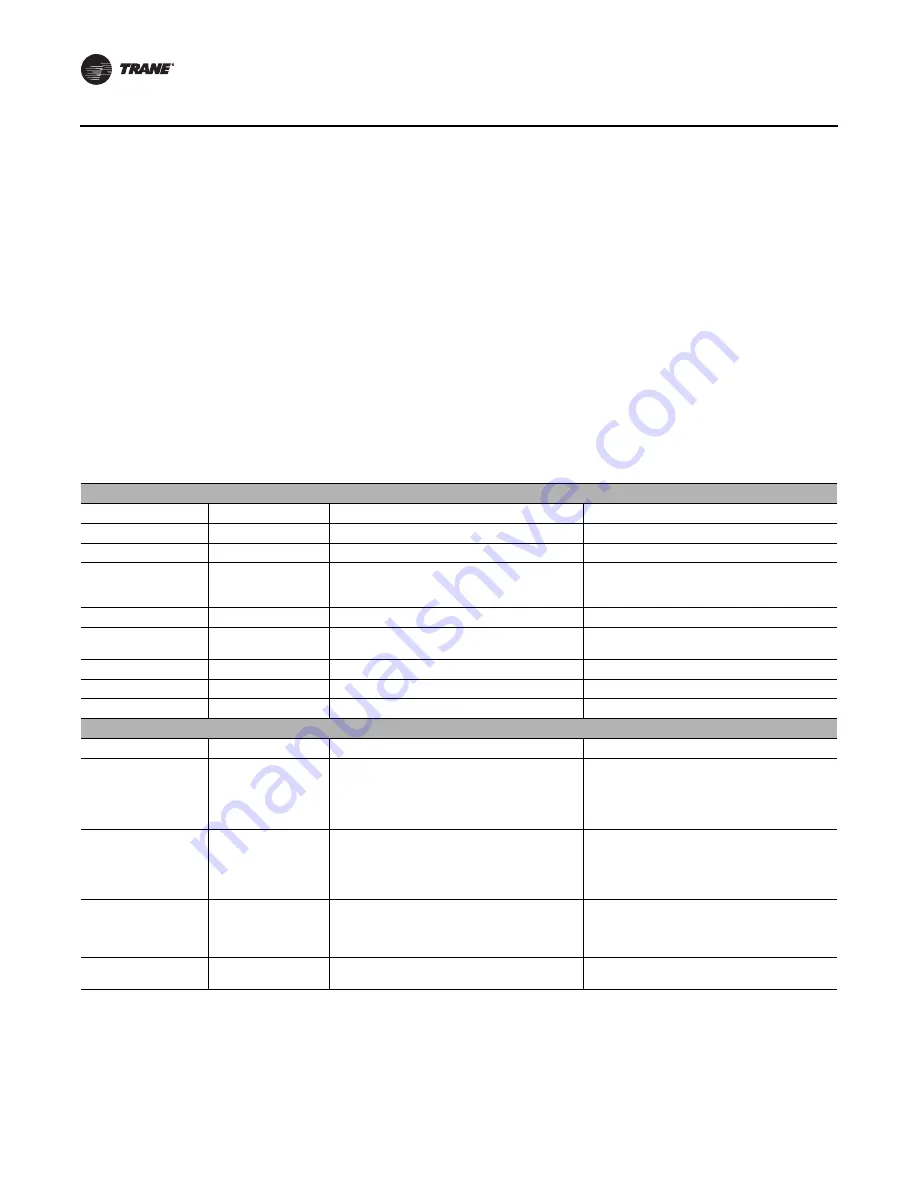
190
RT-SVX36G-EN
Maintenance
Always consult local codes for water treatment and waste water removal requirements. Consult a
water treatment expert for water analysis and chemical treatment methods and recommendations
for specific applications.
If deemed necessary after consultation with local water experts, there are various means of water
treatment available which can be field installed.
Copper Coil Cleaning
With proper water treatment, scale should not form on the coil, and coil cleaning should not be
required. In the event that scale starts to form on the coil, it is imperative that it is removed
immediately. The formation of scale can greatly reduce the performance and reliability of the coil.
To remove any scale that forms use only 100% citric acid based cleaners such as “Now” or other
pure citric acid products.
Important:
Do not use HCL-, muriatic acid, or ammonia-based cleaners as they can adversely
affect copper.
Do not power wash condenser fan. See RT-SVB83*-EN for additional information.
Table 70. Evaporative Condenser Models—Maintenance and Troubleshooting
Maintenance Schedule
Component
Action
Frequency
Comments
Fan Motor
None Required
Non-grease bearings
Sump Pump
Inspect/Clean
1 – 2 times per year
Clean inlet openings to pump
Sump
Inspect/Clean
1 – 2 times per year depending on water
hardness and unit run time
Sump can be drained and hosed out using hose
bib provided at water fill solenoid valve.
Vacuuming scale out is an alternate method.
Sump Float Switch
Inspect
1 – 2 times per year
Float should be free for full float travel
Sump Float
Make Up Valve
Inspect for proper
water level
1 – 2 times per year
Spray Nozzles
Inspect/Clean
1 – 2 times per year
Inspection through access panel
Conductivity Sensor
Inspect/Clean
1 – 2 times per year
Clean sensor to ensure accurate readings
Conductivity Controller
Inspect/Recalibrate
1 – 2 times per year
Recalibrate controller
Troubleshooting
Component
Problem
Check
Fix
Fan Motor
Does not run
Condenser Fan Relay closure and control voltage
indicating a call from compressor control panel
for the condenser fan to operate. Sump Pump
Overload Trip. Fan Motor Overload Trip. Fan fuse
trip.
Check each motor overload and reset if
necessary. Check amp draw for each leg.
Sump Pump
Does not run
Sump Pump Overload Trip Low Water Level or
faulty float switch. Unit in ‘Dry Mode’ Operation
Reset – check amps on each leg to determine if
faulty motor. Check and clean debris around float
switch. Check Ambient thermostat setting and
mode of operation (close on rise). See section 2
for T’stat setup instructions.
Sump Pump
Low Flow
Pump may be operating backwards or impeller
inlet may be slightly blocked.
Change pumping direction by changing any two
legs to the pump motor. Disconnect Power and
remove pump to inspect for possible impeller
obstruction.
Spray Nozzle
Dry area on coil
Check for proper spray pattern over each
quadrant.
Remove debris from clogged nozzle.