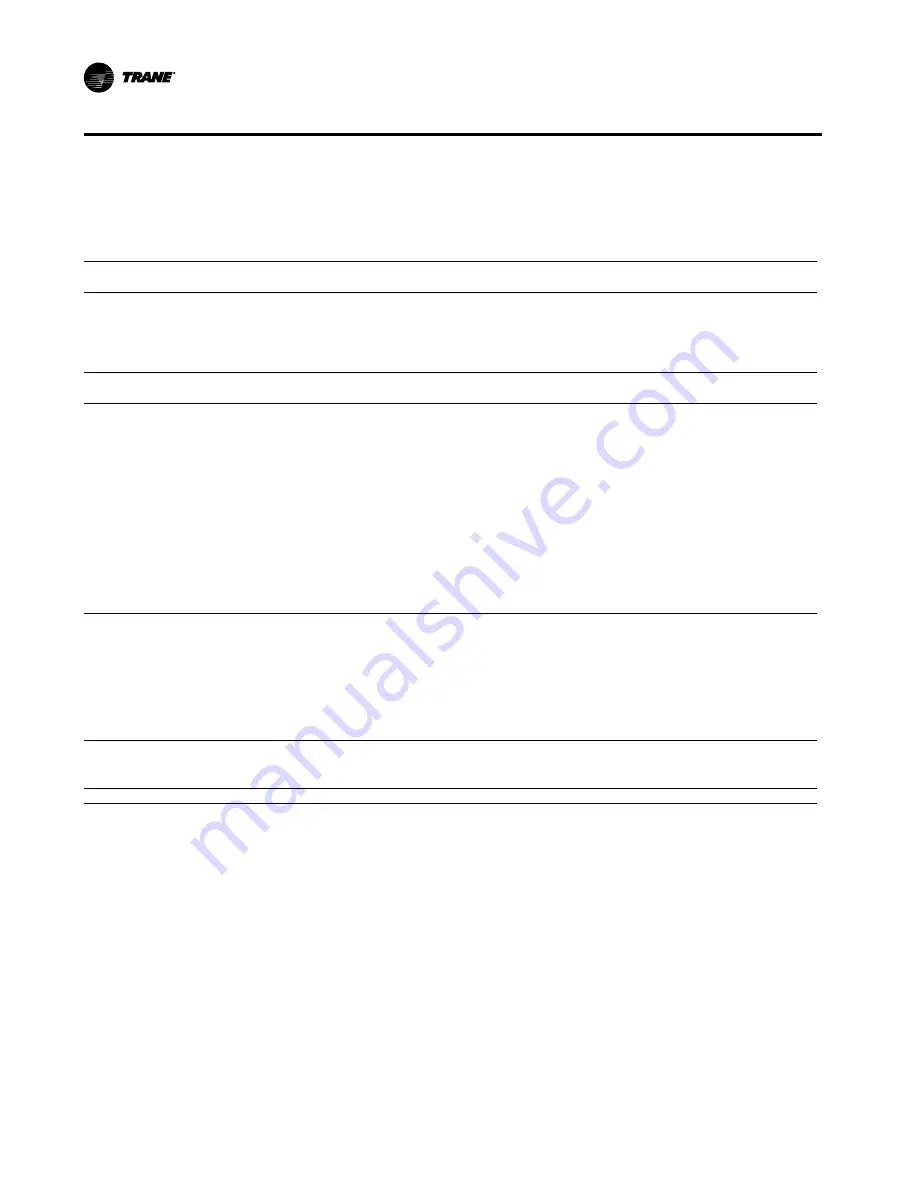
Installation Overview
For convenience, Table 1 summarizes responsibilities that are typically associated with the CVGF chiller
installation process.
Table 1. Installation responsibility chart for CVGF units
Requirement
Trane-supplied,
Trane-supplied,
Field-supplied,
Trane-installed
Field-installed
Field-installed
Rigging
Safety chains
Clevis connectors
Isolation
Isolation pads
Spring isolators
Spring isolators
Electrical
Terminal lugs
Ground connection(s)
Jumper bars
BAS wiring (optional)
IPC wiring
Control voltage wiring
Optional relays and wiring
Water piping
Thermometers
Pressure Relief
Relief valves
Insulation
Insulation (optional)
Insulation
Lifting beam equipment, skates,
rollers, and other lifting
operations
Circuit breakers or non-fused
disconnects (optional)
Circuit breakers or fusible
disconnects (optional)
Temperature sensor
(optional outdoor air)
Remote-mounted starter
(optional)
Chilled-water-pump contactor and
wiring
Condenser-water-pump contactor
and wiring
Flow switches (may be
field-supplied)
Water flow pressure gauges
Isolation and balancing valves
water piping
Pressure relief valves (for water
boxes as required)
Vent line and flexible connector
Unit-mounted starter
(optional)
Vent and drain valves
CVGF-SVX03B-EN
18
General Information
Summary of Contents for CVGF1000
Page 6: ...TRMM Tracer Communications UCP Unit Control Panel CVGF SVX03B EN 6 General Information...
Page 125: ......
Page 126: ......
Page 127: ......