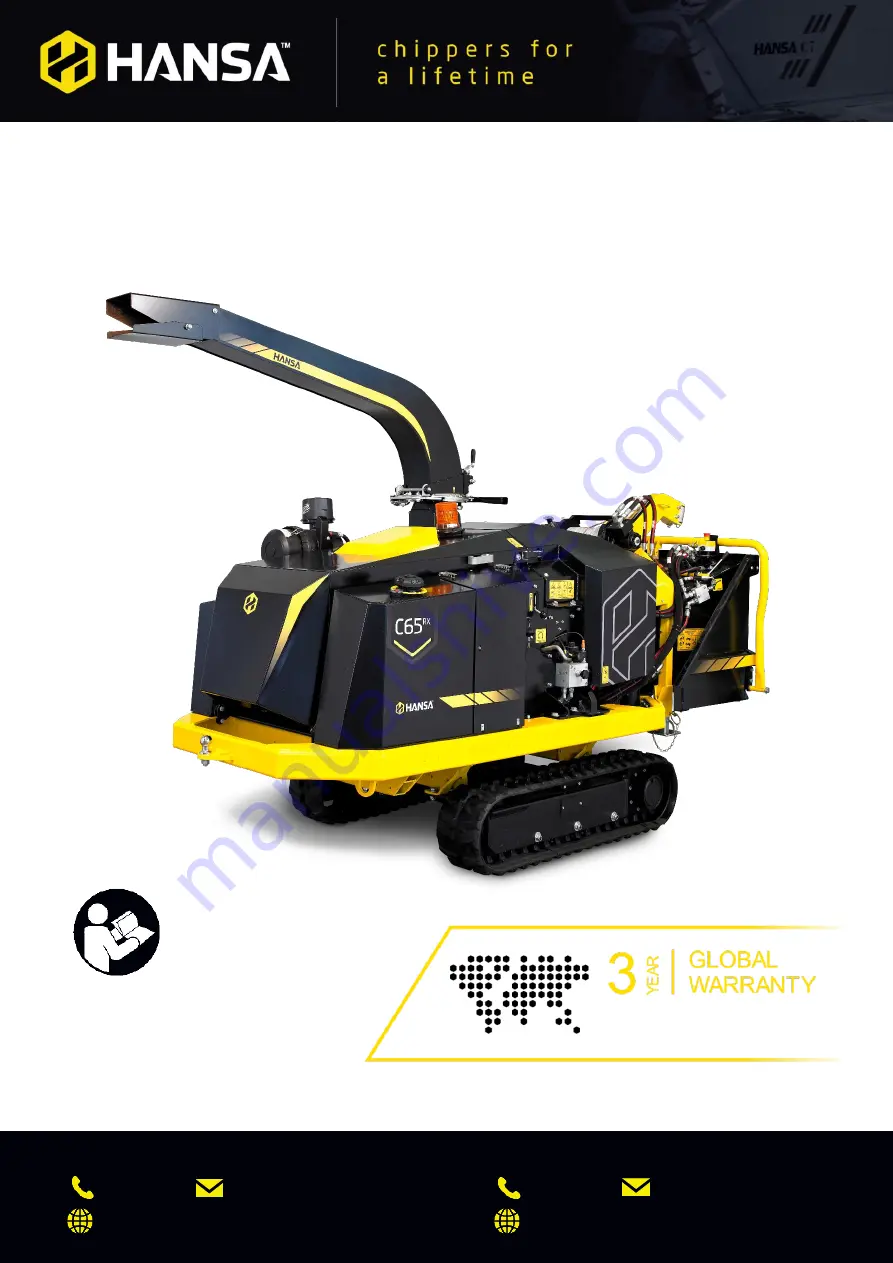
HANSA NEW ZEALAND
+64 7 849 4749 [email protected]
www.hansachippers.com
HANSA AUSTRALIA
1800 426 722 [email protected]
www.hansaproducts.com.au
HANSA
C65RX
Operation, maintenance, and safety manual
All operators must fully read and understand
this operator’s manual
before using the chipper.
Keep this manual for future reference.
Register your Hansa chipper to qualify
www.hansaproducts.com/registration