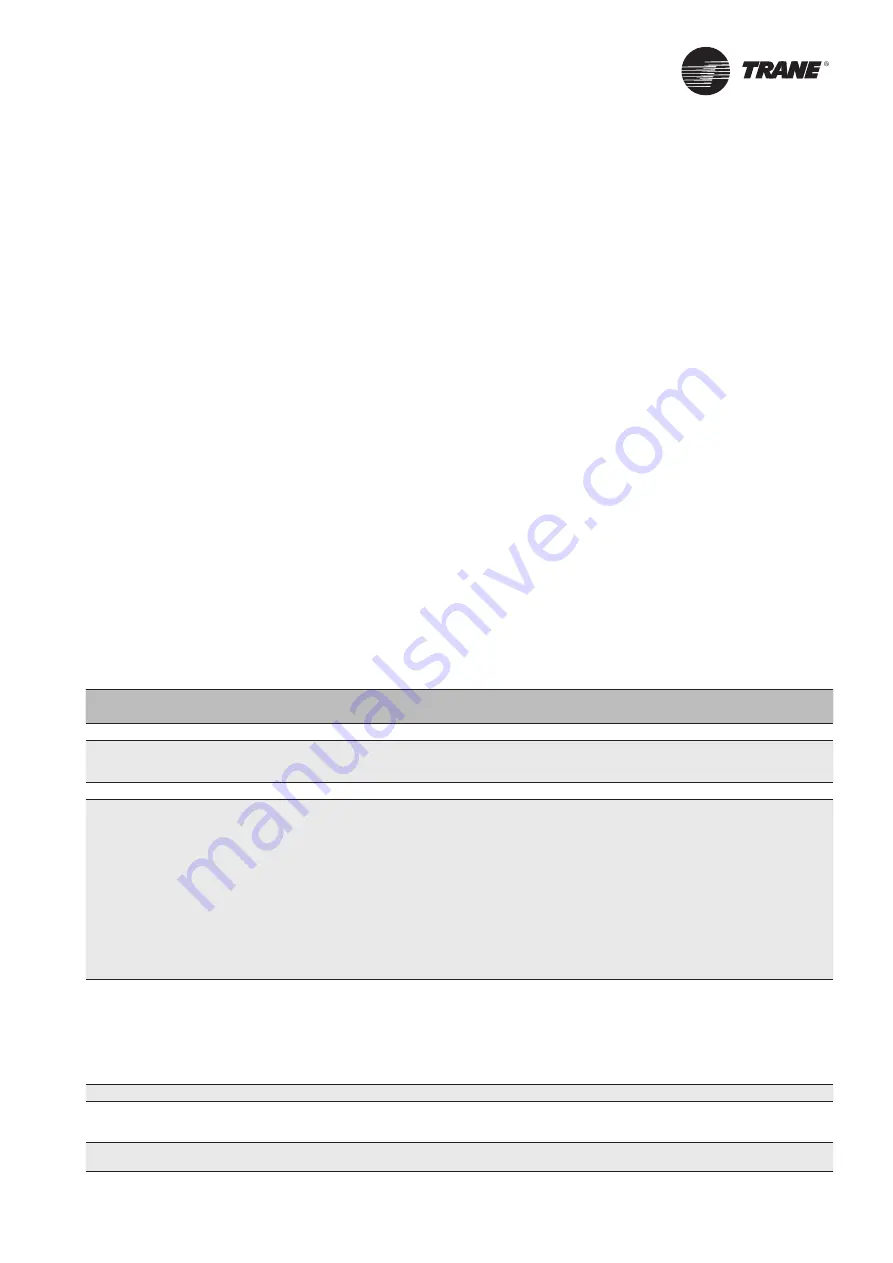
9
RLC-SVX023B-GB
Installation overview and requirements
Contractor responsibilities
A list of the contractor responsibilites typically associated with the installation process is provided in Table 2.
• Locate and maintain the loose parts. Loose parts are located in the control panel.
• Install the unit on a foundation with fl at support surfaces, level within 5 mm and of suffi cient strength to support
concentrated loading. Place the manufacturer-supplied isolation pad assemblies under the unit.
• Install the unit per the instructions outlined in the “Mechanical Installation” section.
• Complete all water piping and electrical connections.
Note: Field piping must be arranged and supported to avoid stress on the equipment. It is strongly recommended
that the piping contractor provide at least 1m of clearance between the pre-installation piping and the planned
location of the unit. This will allow for proper fi t-up upon arrival of the unit at the installation site. All necessary
piping adjustments can be made at that time
• Where specifi ed, supply and install valves in the water piping upstream and downstream of the evaporator and
condenser, to isolate the heat exchangers for maintenance and to balance/trim the system.
• Supply and install fl ow switches or equivalent devices in both the chilled water and condenser water piping.
Interlock each switch with the proper pump starter and Tracer UC800, to ensure that the unit can only operate when
water fl ow is established.
• Supply and install taps for thermometers and pressure gauges in the water piping, adjacent to the inlet and outlet
connections of both the evaporator and the condenser.
• Where specifi ed, supply and install strainers ahead of all pumps and automatic modulating valves.
• Supply and install refrigerant pressure relief piping from the pressure relief to the atmosphere.
• Start the unit under supervision of a qualifi ed service technician.
• Where specifi ed, supply and insulate the evaporator and any other portion of the unit, as required, to prevent
sweating under normal operating conditions.
• For unit-mounted starters, cutouts are provided at the top of the panel for line-side wiring.
• Supply and install the wire terminal lugs to the starter.
• Supply and install fi eld wiring to the line-side lugs of the starter.
Table 2 – Installation Responsibility
Requirement
Trane supplied
Trane installed
Trane supplied
Field installed
Customer supplied
Customer installed
Foundation
Meet foundation requirements
Rigging
Safety chains
Clevis connectors
Lifting beams
Isolation
Isolation pads
Other type of isolators
Electrical
- Circuit breakers or fusible
disconnects (Optional)
- Unit mounted starter
- Wye Delta starter or AFD
(Adaptive Frequency Drive)
- Flow switches (may be
fi
eld
supplied)
- Harmonic
fi
lters (on request
according to customer electrical
network and equipment)
- Circuit breakers or fusible disconnect
- Electrical connections to unit mounted
starter (optional)
- Electrical connections to remote
mounted starter (optional)
- Wiring sizes per submittal and local
regulations
- Terminal lugs
- Ground connections
- BAS wiring (optional)
- Control voltage wiring
- Chilled water pump contactor and
wiring including interlock
- Option relays and wiring
Water piping
Flow switches (may be
fi
eld
supplied)
- Taps for thermometers and gauges
- Thermometers
- Strainers (as required)
- Water
fl
ow pressure gauges
- Isolation and balancing valves in water
piping
- Vents and drain on waterbox valves
- Pressure relief valves for water side
Insulation
Insulation
Insulation
Water piping connection
components
- Grooved pipe
- Grooved pipe to
fl
agged
connection (optional)
Caution on exposure to
refrigerant
Respect recommendation of IOM
addendum
Unit Description