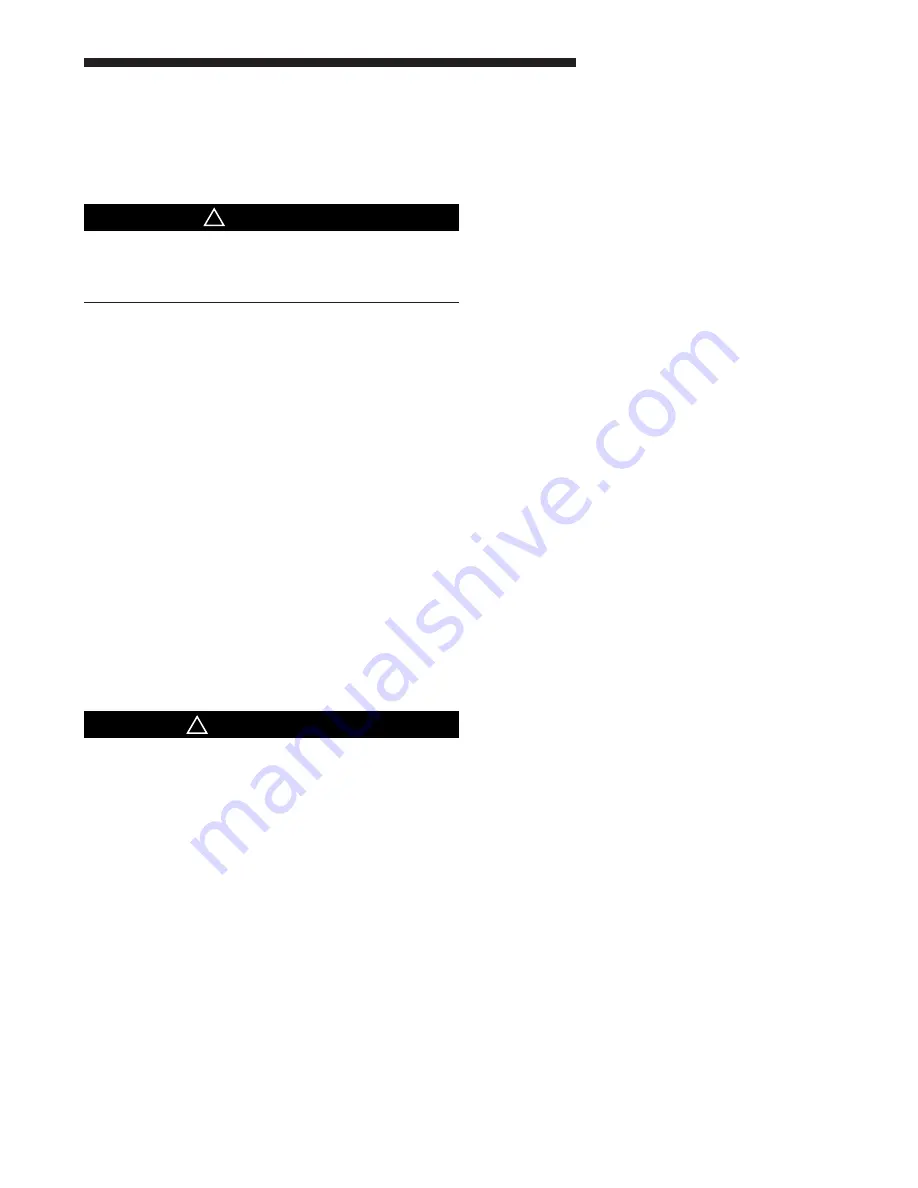
18-CD33D1-4
35
Installer’s Guide
AIRFLOW ADJUSTMENT
Check inlet and outlet air temperatures to make sure
they are within the ranges specified on the furnace rat-
ing nameplate. If the airflow needs to be increased or
decreased, see the wiring diagram for information on
changing the speed of the blower motor.
▲
WARNING
!
Disconnect power to the unit before removing the
blower door.
Failure to follow this warning could result in property
damage, personal injury or death.
This unit is equipped with a blower door switch which cuts
power to the blower and gas valve causing shutdown
when the door is removed. Operation with the door re-
moved or ajar can permit the escape of dangerous fumes.
All panels must be securely closed at all times for safe op-
eration of the furnace.
INDOOR BLOWER TIMING
Heating:
The integrated furnace control module controls
the indoor blower. The blower start is fixed at 45 seconds
after ignition. The FAN-OFF period is field selectable by
dip switches at 60, 100, 140, or 180 seconds. The factory
setting is 100 seconds (See wiring diagram).
Cooling:
The fan delay off period is factory set at 0 sec-
onds. The option for 80 second delay off is field select-
able (See wiring diagram).
ROOM AIR THERMOSTAT
HEAT ANTICIPATOR ADJUSTMENT
Set the thermostat heat anticipator according to the cur-
rent flow measured, or the settings found in the notes
on the furnace wiring diagram (found in the SERVICE
FACTS or inside the furnace casing).
INSTRUCTIONS TO THE OWNERS
▲
WARNING
!
EXPLOSION HAZARD
In the event that electrical, fuel, or mechanical fail-
ures occur, shut off the gas supply off at the manual
gas valve, located on the supply gas piping com-
ing into the furnace, before turning off the electrical
power to the furnace. Contact the service agency
designated by your dealer.
BURNER BOX TEMPERATURE LIMIT DEVICE
All models are equipped with a manual reset temperature
limit located on the burner box. In case of excessive tem-
perature, the limit will open and cause the circuit to open
which shuts off all flow of gas.
CONDITIONS AFFECTING FURNACE OPERATION
1. EXCESSIVE COMBUSTION PRESSURE (WIND IN
EXCESS OF 40 M.P.H.) VENT OR FLUE BLOCK-
AGE
If pressure against induced draft blower outlet be-
comes excessive, the pressure switch will open and
shut off the gas valve until acceptable combustion
pressure is again available.
2. LOSS OF FLAME
If loss of flame occurs during a heating cycle, or
flame is not present at the sensor, the flame control
module will close the gas valve. The flame control
module will then recycle the ignition sequence, then
if ignition is not achieved, it will shut off the gas valve
and lock out the system.
3. POWER FAILURE
If there is a power failure during a heating cycle, the
system will restart the ignition sequence automatical-
ly when power is restored if the thermostat still calls
for heat.
4. GAS SUPPLY FAILURE
If loss of flame occurs during a heating cycle, the
system integrated control module will recycle the ig-
nition sequence, then if ignition is not achieved, the
integrated control module will shut off the gas valve
and lock out the system.
5. INDUCED DRAFT BLOWER FAILURE
If pressure is not sensed by the pressure switch, the
contacts will remain open and not allow the gas valve
to open, therefore the unit will not start. If failure oc-
curs during a running cycle, the pressure switch con-
tacts will open and the gas valve will close to shut the
unit down.
6. CONDENSATE DRAIN BLOCKAGE
If the condensate drain is blocked, either by debris,
improper draining, or by freezing condensate, the
pressure switch will receive a signal warning of the
accumulation of condensate in the heat exchanger
assembly. The pressure switch contacts will open and
remain open, not allowing unit operation. The unit
will not operate until the condensate drain has been
cleared, and the condensate flows freely.
7. RESET AFTER LOCKOUT
When the integrated control module has shut the
system down and gone into lockout, the system must
be manually reset before the unit will restart. To reset,
turn the system power off, then on, then off and then
on again within 30 seconds. This may be done at the
unit’s power source or at the thermostat.
The system
will not reset unless the procedure off-on-off-on is
completed within 30 seconds.