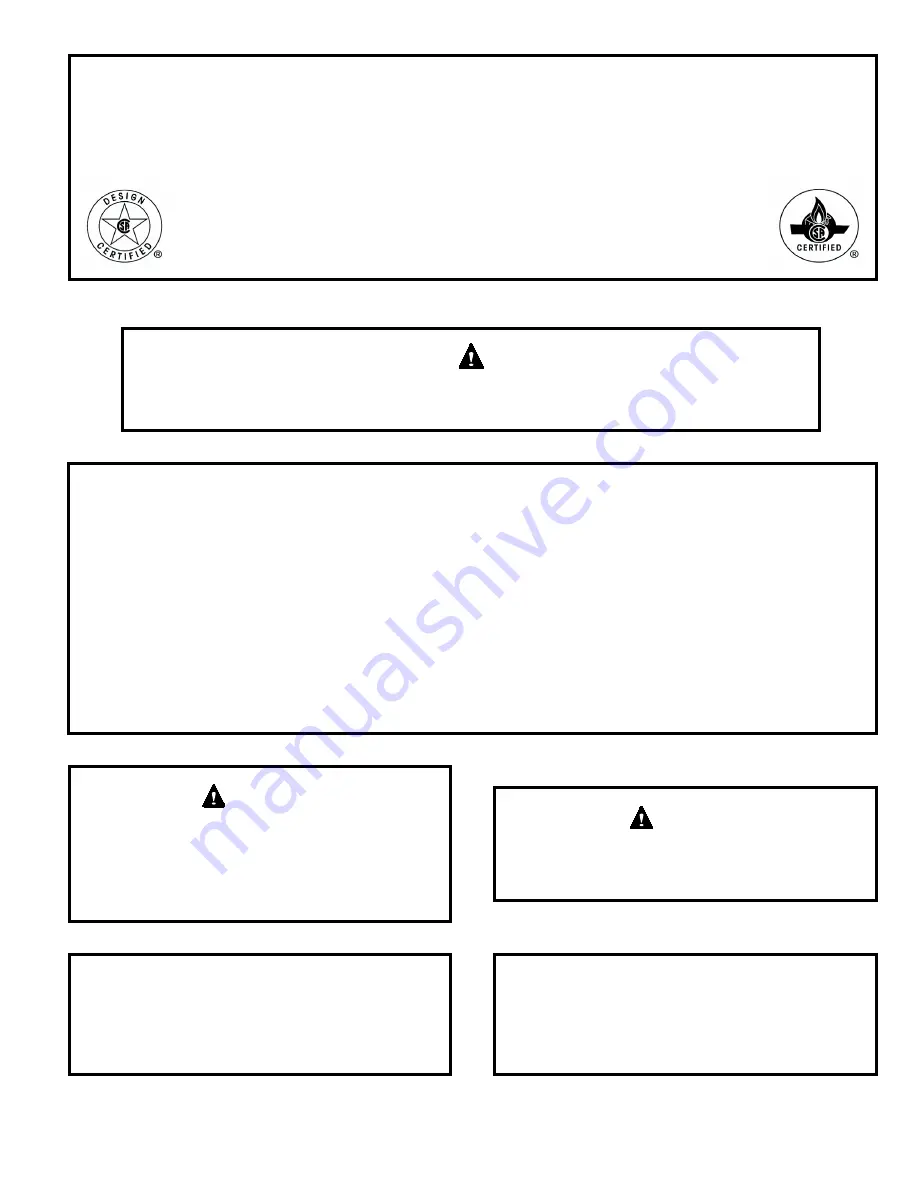
507270-03B
Page 1 of 58
Issue 1904
INSTALLATION INSTRUCTIONS
BG921UH & BG951UH
Warm Air Gas Furnace
Upflow/Horizontal Left and Right Air Discharge
Save these instructions for future reference
(P) 507270-03B
*P507270-03B*
Manufactured By
Blue Summit LLC
8201 C National Turnpike
Louisville, KY 40214
This manual must be left with the homeowner for future reference.
This is a safety alert symbol and should never be ignored. When you see this symbol on labels or in
manuals, be alert to the potential for personal injury or death.
Improper installation, adjustment, alteration, service
or maintenance can cause property damage, personal
injury or loss of life. Installation and service must be
performed by a licensed professional installer (or
equivalent), service agency or the gas supplier.
WARNING
As with any mechanical equipment, personal injury can
result from contact with sharp sheet metal edges. Be
careful when you handle this equipment.
CAUTION
Table of Contents
Unit Dimensions ..........................................................
Parts Arrangement.......................................................
................................................................4
Shipping and Packing List ...........................................4
Safety Information .......................................................4
General ........................................................................
Combustion, Dilution & Ventilation Air .........................
Installation .................................................................
Filters .........................................................................
Duct System ..............................................................
Venting Practices .......................................................
Condensate Piping ....................................................
.................................................................
Electrical ....................................................................42
Unit Start-Up ..............................................................45
Testing for Proper Venting and Sufficient Combustion
Air for Non-Direct Vent Applications ..........................49
Other Unit Adjustments..............................................
Blower Performance BG921UH.................................
Blower Performance BG951UH.................................54
.......................................................................
Planned Service ........................................................
Repair Parts List ........................................................
Summary of Contents for BG921UH
Page 3: ...507270 03B Page 3 of 58 Issue 1904 Parts Arrangement Figure 1 ...
Page 24: ...507270 03B Page 24 of 58 Issue 1904 Figure 25 Figure 26 ...
Page 38: ...507270 03B Page 38 of 58 Issue 1904 Figure 58 Trap Drain Assembly Using 1 2 PVC or 3 4 PVC ...
Page 44: ...507270 03B Page 44 of 58 Issue 1904 Figure 67 Typical Wiring Diagram ...