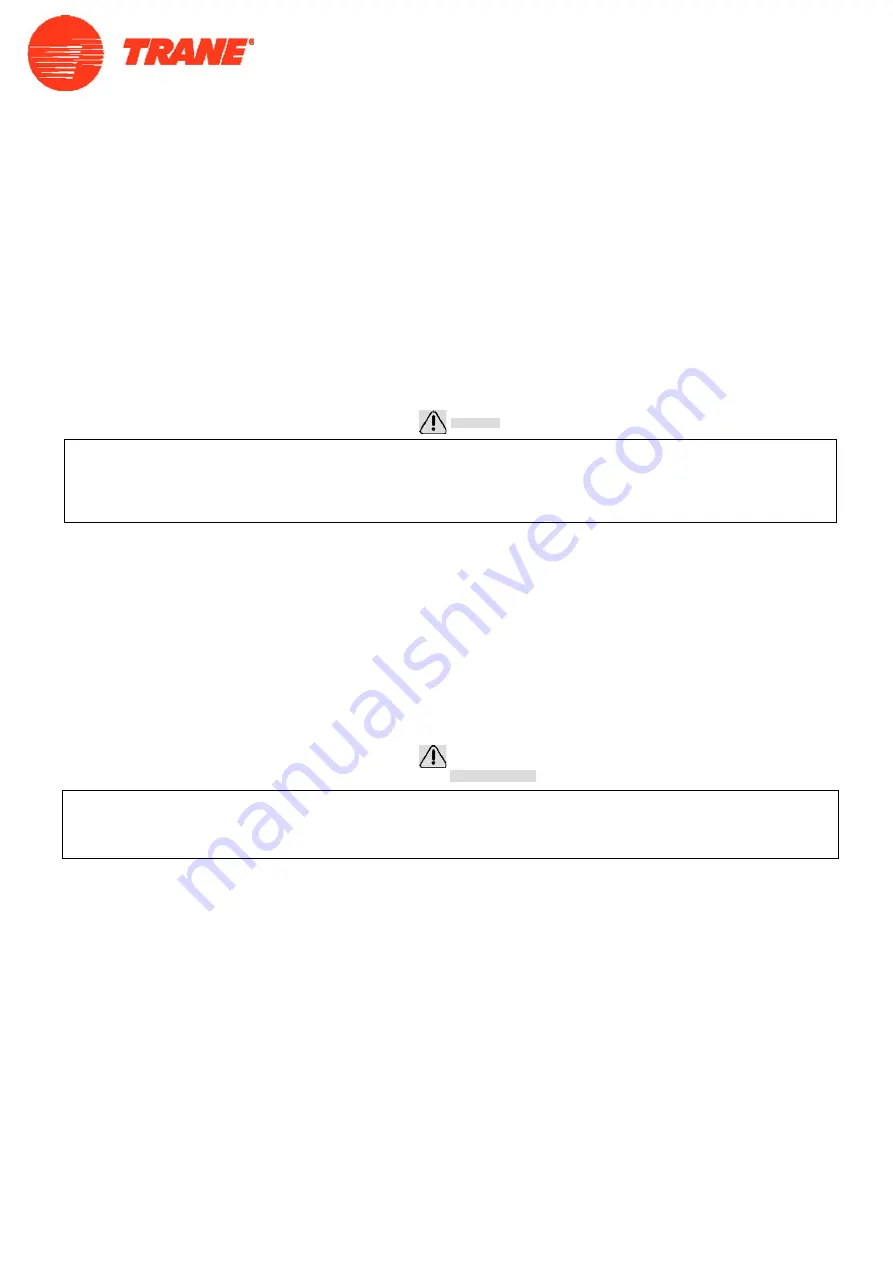
Leak test
The leak test must satisfy specification
1 . Vacuum leak test
1 .1 Evacuate the system from the liquid and gas piping to -100 .7 kPa(5 Torr) .
1 .2 Once reached, turn off the vacuum pump and check that the pressure does not rise for at least 1 minute .
1 .3 Should the pressure rise, the system may either contain moisture (refer to the paragraph “ Vacuum drying
“) or have leaks .
2 . Pressure leak test
2 .1 Break the vacuum by pressurizing with nitrogen gas to a minimum gauge pressure of 0 .2 MPa (2 bar) .
Never set the gauge pressure higher than the maximum operation pressure of the unit, i .e . 4 .0MPa (40bar) .
2 .2 Test for leaks by applying a bubble test solution to all piping connections .
Notice
Make sure to use a recommended bubble test solution from your wholesaler.
Do not use soap water, which may cause cracking of falre nuts (soap water may contain salt, which absorbs
moisture that will freeze when the piping gets cold). and/or lead to corrosion of flared joints (soap water may
contain ammonia which causes a corrosive effect between the brass flare nut and the copper flare).
Vacuum drying
To remove all mositure from the system, proceed as follows:
1 . Evacuate the system for at least 2 hours to a target vacuum of -100 .7 kPa(=-1 .007 bar) .
2 . Check that, with the vacuum pump turned off, the target vacuum is maintained for at least 1 hour .
3 . Should you fail to reach the target vacuum within 2 hours or maintain the vacuum for 1 hour, the system
may contain too much moisture .
4 . In that case, break the vacuum by pressurizing with nigrogen gas to a gauge pressure of 0 .05 MPa (0
.5bar) and repeat steps 1 to 3 unit all moisture has been removed .
5 . The stop valves can now be opened, and/or additional
refrigerant can be charged .
Information
After opening the stop valve, it is possible that the pressure in the refrigerant piping does not rise. This migeh be
caused by e.g. the closed state of the expansion valve in the outdoor unit circuit, but does not present any problem
for correct operation of the unit.
Charging refrigerant
Important information regarding the refrigerant used
This product contains fluorinated greenhouse gases covered by the Kyoto Protocol . Do not vent gases into
the atmopsphere .
Evacuate Indoor Unit and interconnecting pipework to a vacuum pressure of 500 microns and hold for 15 minutes.
The Outdoor unit is supplied with refrigerant HFC-410A (R410A) sufficient for 30m line length .
Calculate additional refrigerant to suit your line length; refer supplied Specification Sheet .
Open the service valve at the Outdoor unit to allow refrigerant to flow throughout the system .
For long line lengths, oil (of the correct type) should be added to the refrigerant system at the rate shown in the
Specification Date table .(see paragraph 9 .5)
Leak check all brazed and fitted joints .
Precautions and general guidelines
When servicing the unit requires the refrigerant system to be opened, treatment and evacuation of refrigerant
must be done in accordance with applicable legislation .
Refrigerant can not be charged until field wiring has been completed .
Refrigerant may only be charged after performing the leak test and vacuum drying .
Summary of Contents for 4TXK6512G1000AA
Page 16: ...2 Dimension 2 1 Dimension 4MXC6518G1000AA 7...
Page 21: ...2 6 Dimension 4MXD6512G1000AA 1 8 5 369 8 5 0 8 9 2 420 1 0 0 0 85 6 4 0 12...
Page 23: ...13...
Page 27: ...1 10 360 2 11 Dimension4MXD6560G1000AA 1262 1200 6 0 0 6 6 0 17...
Page 28: ...1 0 0 0 6 8 2 12 Dimension4MXX6518G1000AA 230 230 2 3 1 8...
Page 29: ...2 13 Dimension4MXX6524G1000AA 19 230 230 1330...
Page 30: ...230 230 1330 2 14 Dimension4MXX6536G1000AA 2 0...
Page 33: ...2 17 Dimension4TXK6512G1000AA...
Page 34: ...23...
Page 35: ...2 18 Dimension4TXK6518G1000AA 24...
Page 36: ...2 19 Dimension4TXK6524G1000AA 25...
Page 38: ...2 21 Dimension4TXK6548G1000AA 27...
Page 39: ...1 3 3 285 3 3 5 2 22 Dimension4TXK6560G1000AA 28...
Page 48: ...0150538189 SW1 O N 1 O N 2 T1A 250VAC F U S E 2 T25A 250VAC FU S E1 4 7 4TXK6512G1000AA 3 7...
Page 75: ...6 0...
Page 79: ...6 3...
Page 82: ...m m o w m m Clamp Clamp accessory Tape White Drain hose Below4mm...
Page 87: ...6 9...
Page 95: ...7 5...
Page 101: ...8 0...
Page 109: ...87...
Page 124: ...100...
Page 129: ...104...
Page 132: ...106...
Page 139: ...112...
Page 142: ...114...
Page 144: ...115...
Page 156: ...126...
Page 159: ...0011800966AL 4TXK6518G1000AA 0011800241C 1U24RS1ERA 129...
Page 160: ...0151800349A 4TXK6536G1000AA 130...
Page 161: ...0151800054BG 4TXK6548G1000AA 0151800054BK 4TXK6560G1000AA 131...
Page 165: ...276 Common control 134...
Page 168: ...The longest 3 minutes 136 O R...
Page 186: ...154...
Page 187: ......