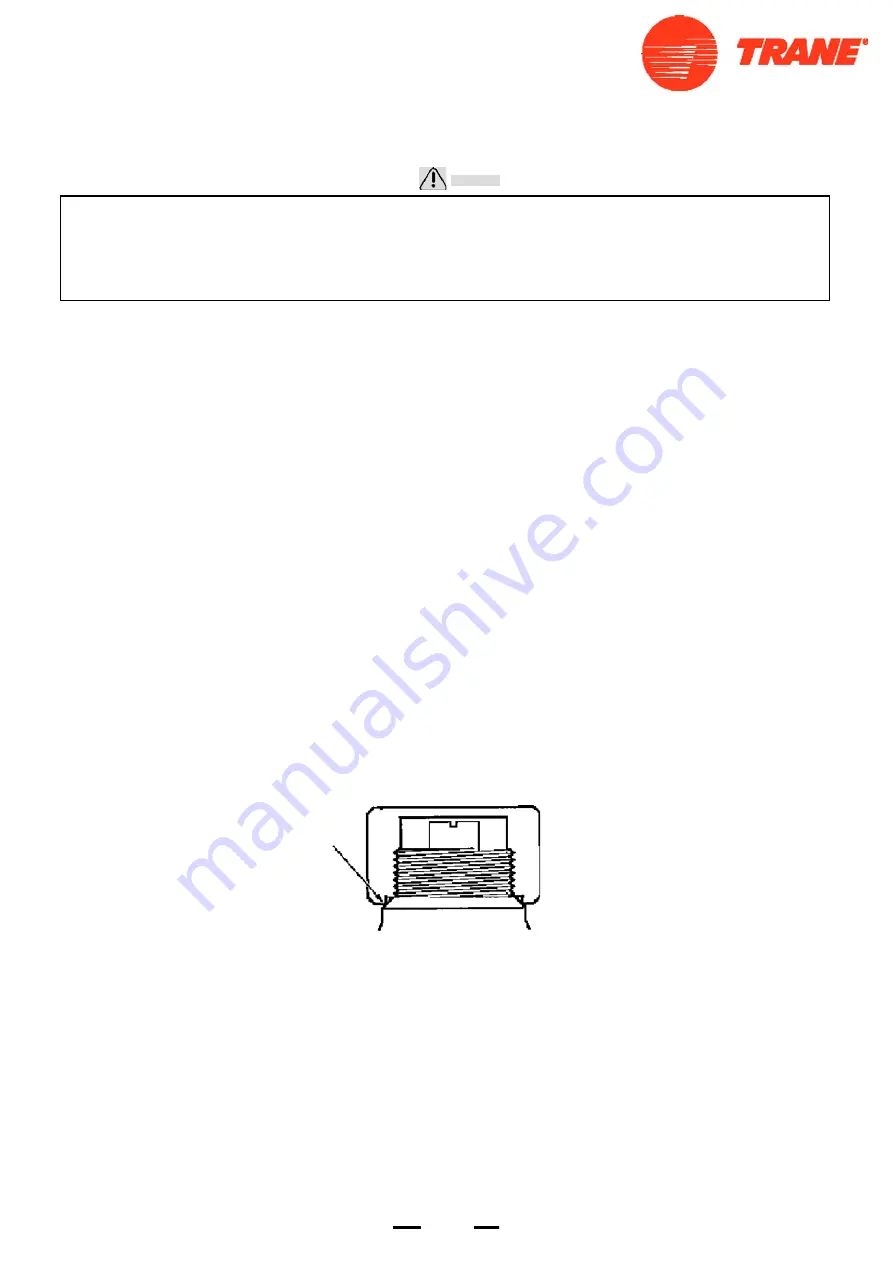
Notice
For new installations, use the standard pipe sizes. When using existiong pipes, size-up is allowed as mentioned
in the table above. Additional restrictions towards allowable pipe lengths, as mentioned in the table 7.3 on page
13, must be taken into account.
Not using the standard lpipe size may result in capacity decrease. The installer must acknowledge this and judge
this very carefully in function of the complete installation.
Existing or pre-installed piping can be used
1 . Piping must comply with the criteria below .
Piping diameter must comply with the limitations as indicated in paragraph “7 .2 . Refrigerant pipe size “ .
Piping length must be withinlimits of the allowable piping length as in paragraph “7 .3 . Allowable pipe
length and height difference” .
Piping must be designed for R410A . See paragraph “6 .2 . Selection of piping material” .
2 . Piping can be reused without cleaning when:
Total 1-way piping length: < 50m .
No compressor breakdown has occurred in the history of the unit to be replaced .
A correct pump down operation can be executed:
- Operate the unit continuously for 30minutes in cooling mode .
- Execute a pump down operation .
- Remove the air conditioning units to be replaced .
Check the contamination inside the existing piping . If you cannot meet all these requirements, the existing
pipes must be cleaned or replaced after removing the air conditioning units to be replaced .
3 . Prepare the flare connections for higher pressure . See paragraph 6 .2
Cautions on handling the stem cap
The stem cap is sealed where indicated by the arrow . Take care not to damage it .
After handling the stop valve, make sure tighten the stem cap securely . For the tightening torque, refer to the table
below .
Check for refrigerant leaks after tightening the stem cap .
Cautions on handling the service port
Always use a charge hose equipped with a valve depressor pin, since the service port is a Schrader type valve .
After handling the service port, make sure to tighten the service port cap securely . For the tightening torque,
refer to the table below .
Check for refrigerant leaks after tightening the service port cap .
1 0 7
Summary of Contents for 4TXK6512G1000AA
Page 16: ...2 Dimension 2 1 Dimension 4MXC6518G1000AA 7...
Page 21: ...2 6 Dimension 4MXD6512G1000AA 1 8 5 369 8 5 0 8 9 2 420 1 0 0 0 85 6 4 0 12...
Page 23: ...13...
Page 27: ...1 10 360 2 11 Dimension4MXD6560G1000AA 1262 1200 6 0 0 6 6 0 17...
Page 28: ...1 0 0 0 6 8 2 12 Dimension4MXX6518G1000AA 230 230 2 3 1 8...
Page 29: ...2 13 Dimension4MXX6524G1000AA 19 230 230 1330...
Page 30: ...230 230 1330 2 14 Dimension4MXX6536G1000AA 2 0...
Page 33: ...2 17 Dimension4TXK6512G1000AA...
Page 34: ...23...
Page 35: ...2 18 Dimension4TXK6518G1000AA 24...
Page 36: ...2 19 Dimension4TXK6524G1000AA 25...
Page 38: ...2 21 Dimension4TXK6548G1000AA 27...
Page 39: ...1 3 3 285 3 3 5 2 22 Dimension4TXK6560G1000AA 28...
Page 48: ...0150538189 SW1 O N 1 O N 2 T1A 250VAC F U S E 2 T25A 250VAC FU S E1 4 7 4TXK6512G1000AA 3 7...
Page 75: ...6 0...
Page 79: ...6 3...
Page 82: ...m m o w m m Clamp Clamp accessory Tape White Drain hose Below4mm...
Page 87: ...6 9...
Page 95: ...7 5...
Page 101: ...8 0...
Page 109: ...87...
Page 124: ...100...
Page 129: ...104...
Page 132: ...106...
Page 139: ...112...
Page 142: ...114...
Page 144: ...115...
Page 156: ...126...
Page 159: ...0011800966AL 4TXK6518G1000AA 0011800241C 1U24RS1ERA 129...
Page 160: ...0151800349A 4TXK6536G1000AA 130...
Page 161: ...0151800054BG 4TXK6548G1000AA 0151800054BK 4TXK6560G1000AA 131...
Page 165: ...276 Common control 134...
Page 168: ...The longest 3 minutes 136 O R...
Page 186: ...154...
Page 187: ......