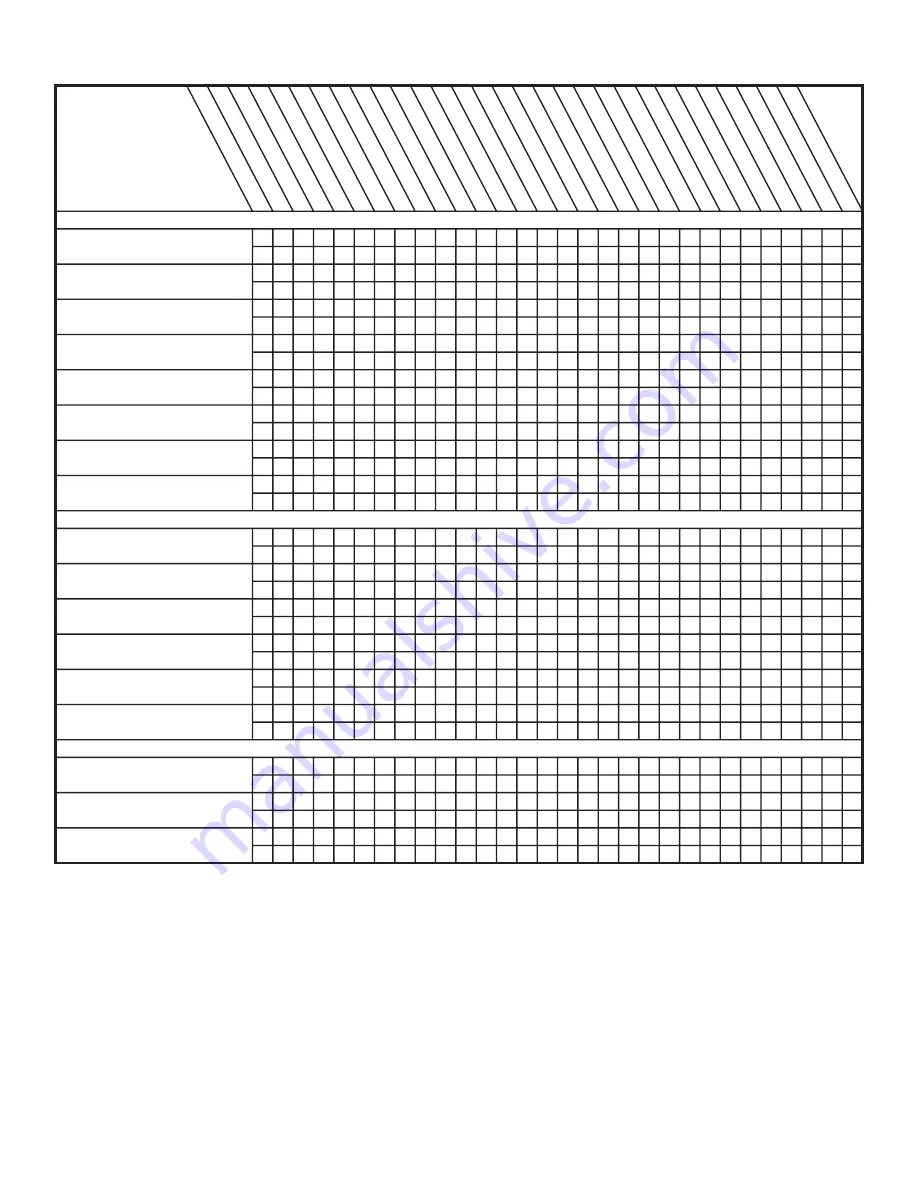
18-AC78D1-6
25
15.2 Troubleshooting
SYSTEM FAULTS
REFRIGERANT CIRCUIT
Head Pressure Too High
Head Pressure Too Low
Suction Pressure Too High
Suction Pressure Too Low
Liquid Refrig. Floodback (TXV/EEV)
Liquid Refrig. Floodback
(Cap. Tube)
I.D. Coil Frosting
Compressor Runs
Inadequate or No Cooling/Htg
ELECTRICAL
Compressor & O.D. Fan
Won’t Start
Compressor Will Not Start
But O.D. Fan Runs
O.D. Fan Won’t Start
Compressor Hums But Won’t Start
Compressor Cycles on IOL
I.D. Blower Won’t Start
DEFROST
Unit Won’t Initiate Defrost
Defrost Terminates on Time
Unit Icing Up
W
HA
T T
O
CH
EC
K M
OD
E
PO
W
ER
S
UP
PLY
HIG
H V
OLT
AG
E W
IRIN
G
CO
MP
RE
SS
OR
IO
L
RU
N C
APA
CIT
OR
STA
RT
C
APA
CIT
OR
STA
RT
R
EL
AY
CO
NTA
CT
OR
C
ON
TAC
TS
LO
W
VO
LTA
GE
W
IRIN
G
CO
NT
RO
L T
RA
NS
FO
RM
ER
TH
ER
MO
STA
T
CO
NTA
CT
OR
C
OIL
LO
W
VO
LTA
GE
FU
SE
ST
UC
K C
OM
PR
ES
SO
R
INE
FF
ICIE
NT
C
OM
P.
RE
F. U
ND
ER
CH
AR
GE
RE
F. O
VE
RC
HA
RG
E
EX
CE
SS
IVE
E
VA
P. L
OA
D
NO
NC
ON
DE
NS
AB
LE
S
RE
S.
O.D
. A
IRF
LO
W
O.D
. A
IR
RE
CIR
CU
LAT
IO
N
TX
V/E
EV
S
TU
CK
O
PE
N
SU
PE
RH
EAT
RE
S.
I.D
. A
IRF
LO
W
RE
F. C
IR.
RE
ST
RIC
TIO
NS
SO
V L
EA
KIN
G
SO
V C
OIL
D
EF
EC
TIV
E
CH
EC
K V
ALV
E L
EA
KIN
G
*
DE
FR
OS
T R
EL
AY
D
EF.
DE
FR
OS
T C
ON
TR
OL
D
EF.
C
H
C
H
C
H
C
H
C
H
C
H
C
H
C
H
C
H
C
H
C
H
C
H
C
H
C
H
C
H
C
H
C
H
P
P
P
P
P
P
P
P
P
P
P
P
P
P
S
S
S
S
S
S
S
S
S
S
S
S
S
S
S
S
S
S
S
S
S
S
S
S
S
S
S
S
P
P
P
P
S
S
S
S
P
P
P
P
S
S
P
P
P
P
P
P
P
P
P
P
P
P
P
P
S
S
S
S
S
S
S
S
P
P
P
P
P
P
P
P
P
P
P
P
P
P
P
P
P
P
P
P
P
S
S
S
S
S
S
S
P
S
S
S
S
S
S
S
S
S
S
S
S
S
S
S
S
P
P
S
S
S
S
S
S
S
S
S
S
S
S
P
P
P
P
P
P
S
S
S
S
S
S
S
S
S
S
S
P
P
S
S
S
S
S
S
S
S
P
P
P
P
P
P
P
S
S
P P
P
P
C - Cooling H - Heating P - Primary Causes S - Secondary Causes
*
- 3 Phase Only