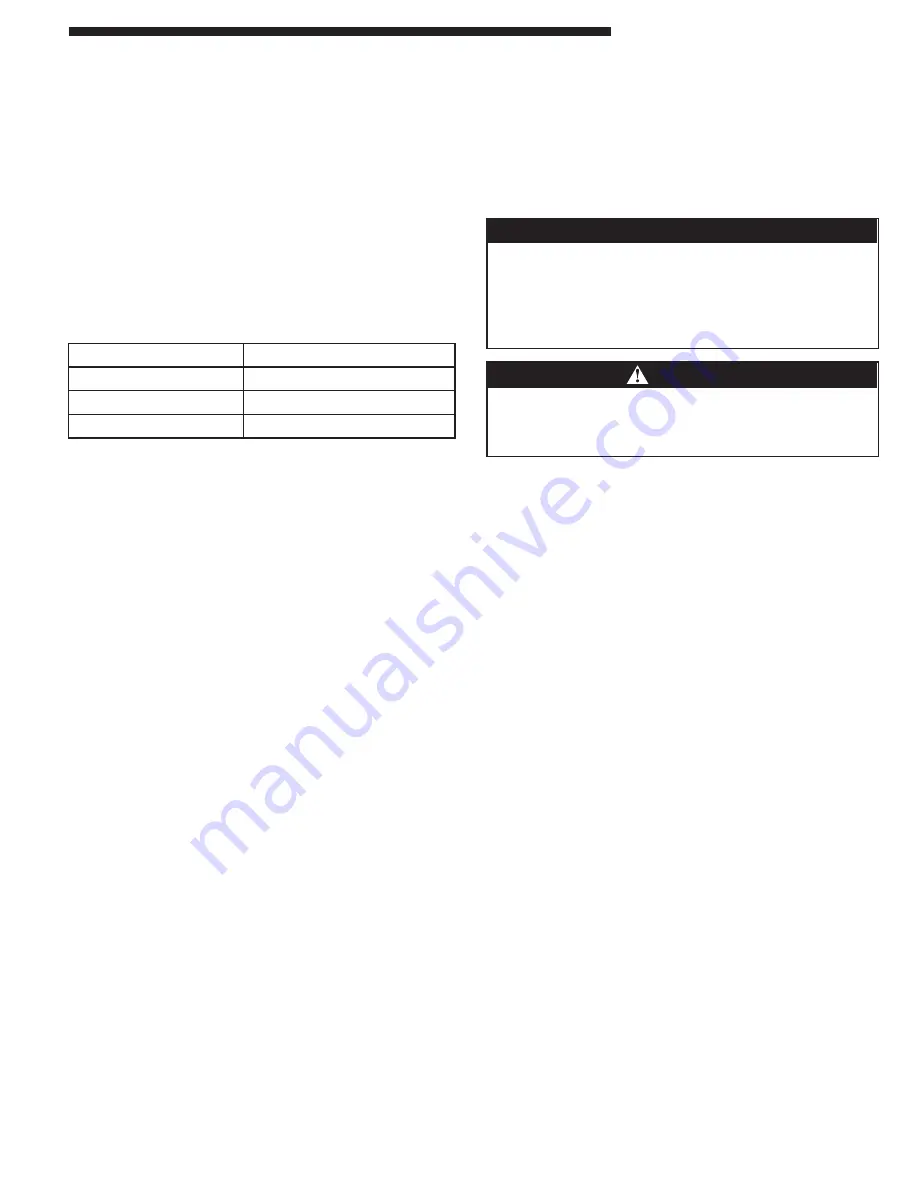
Page 19
Installer’s Guide
Starting the Unit in Cooling Mode
Control Wiring (Class II)
Low voltage control wiring should not be run in conduit with power
wiring unless Class 1 wire of proper voltage rating is used. Route
the thermostat cable or equivalent single leads of No. 18 AWG
colored wire from the thermostat subbase terminals through the
rubber grommet on the unit. See Figures 2, 4, 6, or 8
for the
control entry (24V Entry) location. Make connections as shown
on the unit wiring diagram.
Do not short thermostat wires since this will damage the control
transformer.
Refer to Table 2 for recommended wire sizes and lengths for install-
ing the unit thermostat. The total resistance of these low voltage
wires must not exceed one (1) ohm. Any resistance in excess of 1
ohm may cause the control to malfunction because of the exces-
sive voltage drop.
IMPORTANT:
Upon completion of wiring, check all electrical con-
nections, including factory wiring within the unit.
Make sure all connections are tight. Replace and secure all electri-
cal box covers and access panels before leaving the unit or turning
on the power to the unit.
Pre-Start Quick Checklist
Is the unit properly located and level with the proper
clearance? See Figures 1 to 6. See Step 3-Review
Location and Recommendation Information on page 10.
Is the duct work correctly sized, run, taped, insulated, and
weatherproofed with proper unit arrangement? See
Ductwork Installation section on page 16.
Is the condensate line properly sized, run, trapped, and
pitched? See Condensate Drain Piping section on page
16.
Is the filter of the correct size and quantity? Is it clean and in
place? See Air Filter Installation section on page 16.
Is the wiring properly sized and run according to the unit
wiring diagram? See Electrical Wiring section on page 17.
Are all the wiring connections, including those in the unit,
tight? See Electrical Wiring section on page 17.
Has the unit been properly grounded and fused with the
recommended fuse size? See Electrical Wiring section on
page 17.
Is the thermostat well located, level, and correctly wired?
See Electrical Wiring section on page 17.
Have the air conditioning systems been checked at the service
ports for charge and leak tested if necessary?
Step 5—Unit Startup
Table 2. Thermostat Wire Size and Maximum Length
Do the condenser fan and indoor blower turn free without
rubbing, and are they tight on the shafts?
Has all work been done in accordance with applicable local
and national codes?
Are all covers and access panels in place to prevent air loss and
safety hazards?
Thermostat Heat Anticipator
Set the thermostat heat anticipators to equal the amperage draw
of the W1 thermostat circuit.
CAUTION
Before starting the system on the cooling cycle, turn the comfort
control to
OFF
and close the unit disconnect switch. This is
a precaution against foaming at startup which could damage
the compressor bearings.
Safety Hazard. Do not operate the unit without the evapora-
tor fan access panel or evaporator coil access panel in place.
Reinstall the access panels after performing maintenance
procedures on the fan. Operating the unit without the access
panels properly installed may result in severe personal injury
or death.
s
s
WARNING
NOTE: See the section on “Sequence of Operation” for a de-
scription of the cooling operating sequence.
To start the unit in the cooling mode, set the comfort control to
COOL
and to a setting below room temperature. The condenser fan motor,
compressor and evaporator fan motor will operate automatically.
Operating Pressure Checks
After the unit has operated in the cooling mode for a short period of
time, install pressure gauges on the gauge ports of the discharge
and suction line valves (behind the Compressor access panel).
Check the suction and discharge pressures and compare them to the
normal operating pressures provided in the unit’s
SERVICE FACTS.
NOTE: Do not use the PRESSURE CURVES from the unit's
SERVICE FACTS to determine the unit refrigerant charge. The
correct charge is shown on the unit nameplate. To charge the
system accurately, weigh in the charge according to the unit
nameplate and check subcooling against the Subcooling Charg-
ing Table in the SERVICE FACTS.
Voltage Check
With the compressor operating, check the line voltage at the unit
(contactor is located behind the Control access panel). The volt-
age should be within the range shown on the unit nameplate. If low
voltage is encountered, check the size and length of the supply line
from the main disconnect to the unit. The line may be undersized
for the length of the run.
Cooling Shut Down
Set the comfort control to
OFF
or to a setting above room temperature.
IMPORTANT:
De-energize the main power disconnect ONLY when
servicing the unit. Power may be required to keep the heat pump
compressor warm and to boil off refrigerant in the compressor.
WIRE SIZE
MAXIMUM LENGTH (Ft)
18
75
16
125
14
200
Summary of Contents for 4TCY4024
Page 5: ...Page 5 Installer s Guide Figure 2 4TCY4024 through 4TCY4036 2 of 3...
Page 6: ...Page 6 Installer s Guide Figure 3 4TCY4024 through 4TCY4036 3 of 3...
Page 8: ...Page 8 Installer s Guide Figure 5 4TCY4042 through 4TCY4060 2 of 3...
Page 9: ...Page 9 Installer s Guide Figure 6 4TCY4042 through 4TCY4060 3 of 3...
Page 18: ...Page 18 Installer s Guide Figure 20 Typical 4TCY4 Field Wiring Diagram...
Page 22: ...Page 22 Installer s Guide Notes...