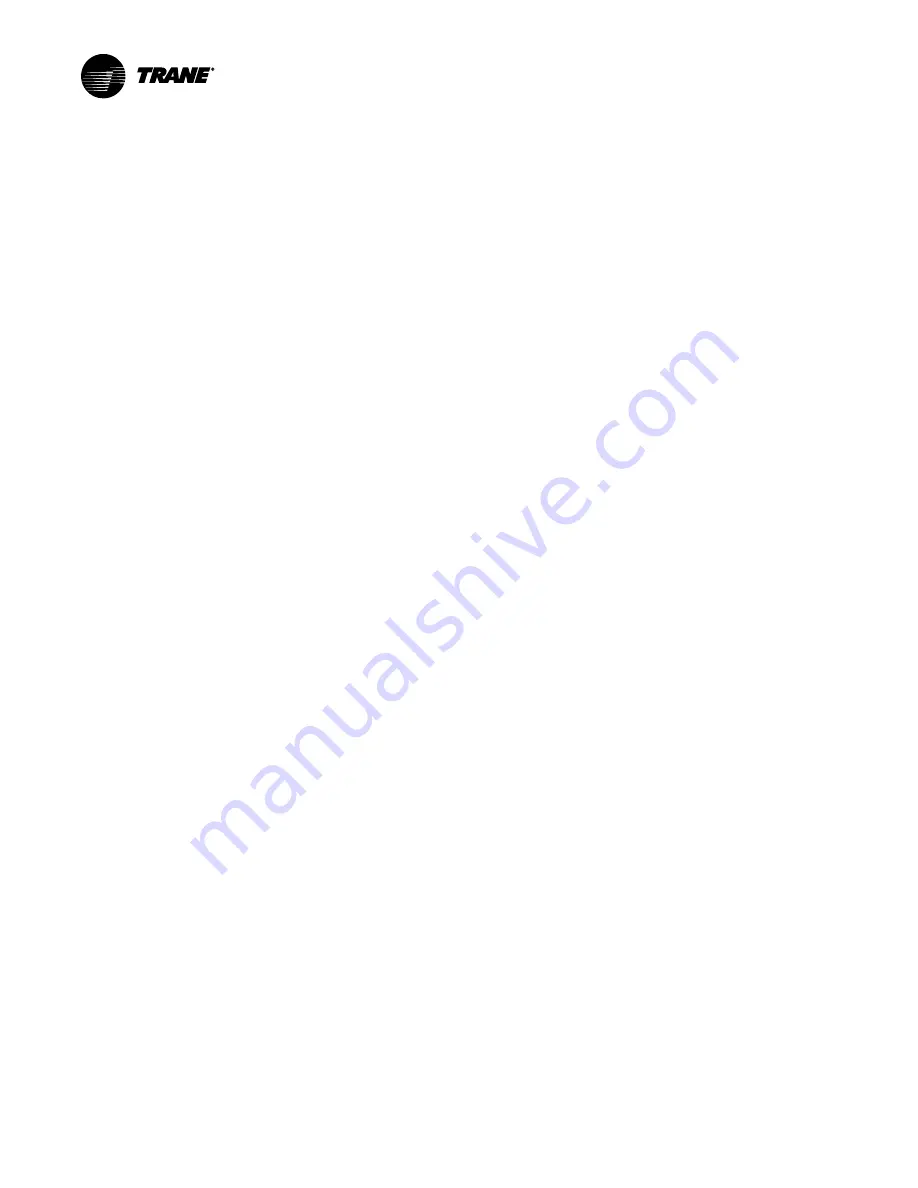
104
CVHE-SVX005B-EN
Appendix D: CenTraVac
™
™
Chiller Annual Inspection List
Follow the annual maintenance instructions provided
in the text of this manual, including but not limited to:
1. C
Co
om
mp
prre
esssso
orr//M
Mo
otto
orr
☐
Motor continuity.
☐
Motor meg test.
☐
Check motor terminals.
☐
Inspect motor terminal board.
☐
Check inlet guide vanes (IGV) for abnormalities.
2. S
Stta
arrtte
err o
orr A
Ad
da
ap
pttiiv
ve
e F
Frre
eq
qu
ue
en
nccy
y
™
™
D
Drriiv
ve
e
☐
Inspect starter contacts.
☐
Check all connections per manufacturer
specifications.
☐
Follow all manufacturer recommendations for
starter or Adaptive Frequency
™
Drive (AFD)
maintenance.
☐
Inspect/clean/service the AFD cooling system
(water- or air-cooled AFD).
☐
Record all applicable starter or starter
component settings.
3. O
Oiill S
Sy
ysstte
em
m
☐
Annual oil analysis (follow recommendations).
☐
Clean and lubricate oil system as required.
☐
Electrical inspection.
☐
Pump motor continuity check.
☐
Run oil pump and check differential oil pressure.
4. C
Co
on
nd
de
en
nsse
err
☐
Inspect for fouling and scaling in tubes.
☐
Check operation of condenser water flow
sensing device.
☐
Factory recommendation to eddy current test
tubes every three years.
5. E
Ev
va
ap
po
orra
atto
orr
☐
Inspect for fouling and scaling in tubes.
☐
Check operation of evaporator water flow
sensing device.
☐
Factory recommendation to eddy current test
tubes every three years.
6. H
He
ea
att R
Re
ecco
ov
ve
erry
y
☐
Inspect for fouling and scaling in tubes.
☐
Check operation of heat recovery water flow
sensing device.
☐
Factory recommendation to eddy current test
tubes every three years.
7. C
Co
on
nttrro
oll C
Ciirrccu
uiittss
☐
Verify control parameters.
☐
Test appropriate sensors for accuracy.
☐
Ensure sensors are properly seated in wells with
thermopaste installed.
☐
Check evaporator leaving water temperature
low temperature cutout setpoint.
☐
Condenser high pressure switch check-out.
☐
Check adjustment and operation of the inlet
guide vane actuator.
8. L
Le
ea
akk T
Te
esstt C
Ch
hiilllle
err
☐
Check purge times and unit performance logs. If
warranted, pressure leak test.
☐
Review oil analysis. If required, submit
refrigerant sample for analysis.
☐
Inspect unit for any signs of refrigerant or oil
leakage.
☐
Check unit for any loose screws on flange,
volutes, or casing.
9. P
Pu
urrg
ge
e U
Un
niitt
☐
Review the purge
Installation, Operation, and
Maintenance
manual and follow maintenance
and/or inspection items identified.
☐
Review purge pump-out data.
☐
Review overall operation of purge and service
as necessary.
10. E
Ex
xtte
erriio
orr
☐
Inlet guide vane linkage.
☐
Clean and touch-up painted surfaces as needed.
☐
Repair deteriorated, torn, or missing insulation.
11. O
Op
pttiio
on
na
all A
Acccce
esssso
orriie
ess
☐
If applicable, lubricate factory-installed gantries.
☐
After the first month of operation, inspect
Heresite
®
or Belzona
®
coated waterboxes;
thereafter, inspect as needed.
☐
Inspect anodes.
☐
Inspect and lubricate hinged waterboxes.
☐
With water flow sensing option, bleed tubing
from waterboxes to transformers.