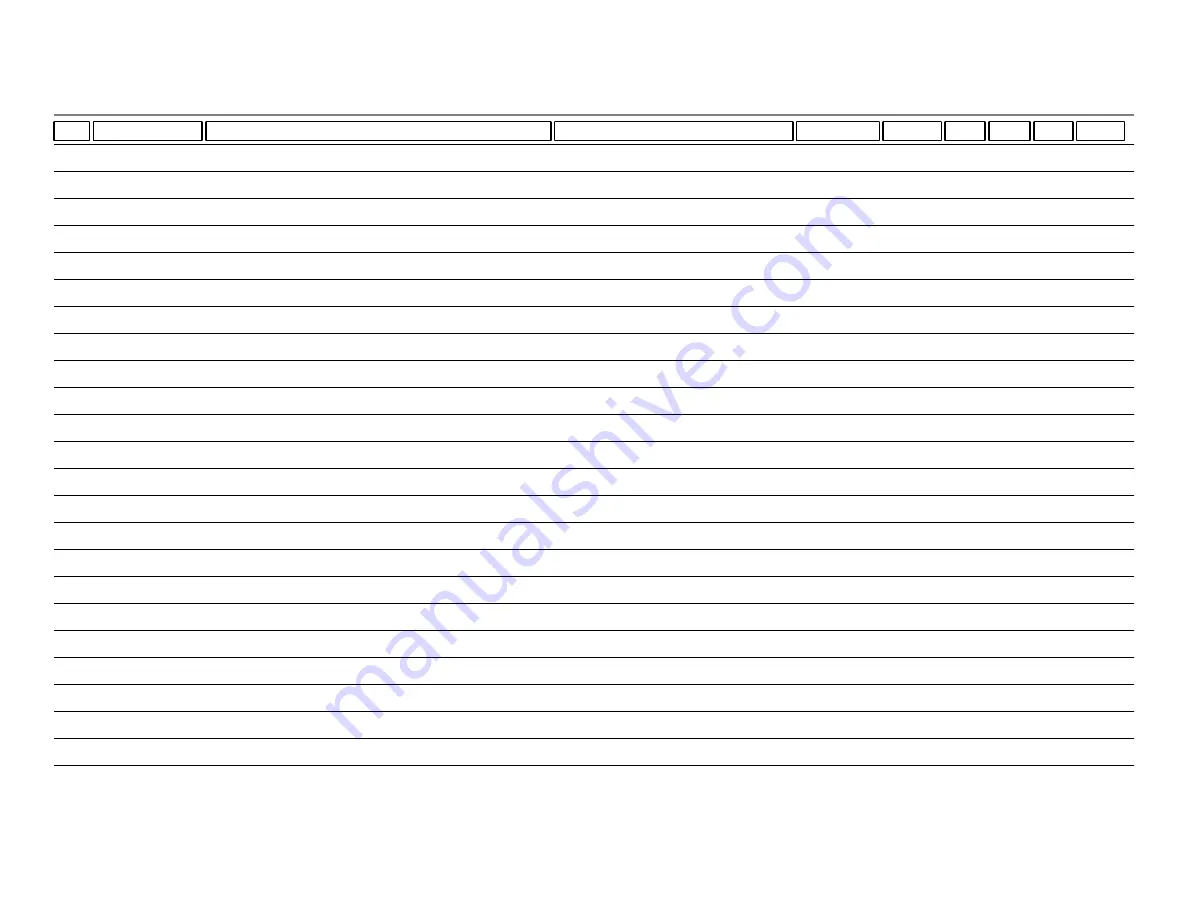
Parts List for Assembly P/N: 29533
Item P/N
Title
Detail
Reference(t)
Qty
UseAs Rev
Stat
Type
29533
Printed 1/31/2019
Rev A
DRIVE ASSY - X AXIS - 1845RX
1845
29
29440-6
CLAMP-LOWER-MOTOR CONNECTOR
1
EA
A
R
DWG
35
LU050010
SADDLE
(1)
EA
A
R
PS
36
27982
CROSS SLIDE
(1)
EA
-
R
PS
37
29494-1
COVER-1845 X AXIS-PULLEY
(1)
EA
A
R
DWG
38
29494-2
COVER-1845 X AXIS-MOTOR-FRONT
(1)
EA
A
R
DOC
39
29494-3
COVER-1845 X AXIS-MOTOR-SIDE-R
(1)
EA
A
R
DWG
40
29494-4
COVER-1845 X AXIS-MOTOR-SIDE-L
(1)
EA
A
R
DWG
41
29494-5
COVER-1845 X AXIS-MOTOR-BOTTOM
(1)
EA
A
R
DWG
42
LS050050
GIB SEAT
(1)
EA
-
R
PS
43
LS050060
GIB SEAT
(1)
EA
-
R
PS
44
27997
GIB-Z AXIS-1845
(2)
EA
B
R
PS
45
27987
GIB-X AXIS-1845
(1)
EA
B
R
PS
46
KR050020
ADJUSTABLE SCREW
(2)
EA
-
R
PS
47
KR050030
ADJUSTABLE SCREW
(1)
EA
-
R
PS
52
25428
WIPER-Z GIB-LEFT REAR & RIGHT FRONT-1845
(2)
EA
A
R
PS
53
25429
WIPER-Z GIB-LEFT FRONT & RIGHT REAR-1845
(2)
EA
A
R
PS
54
27991-1
WIPER-REAR-CROSSLIDE-LEFT-1845
(1)
EA
A
R
PS
55
27991-2
WIPER-REAR-CROSSLIDE-RIGHT-1845
(1)
EA
A
R
PS
56
27992
WIPER-CROSS SLIDE-FRONT-1845
(1)
EA
A
R
PS
57
27988
WIPER-FLAT-SADDLE-1845
(2)
EA
A
R
PS
58
27989
WIPER-VEE-SADDLE-1845
(2)
EA
A
R
PS
59
LU400450
WAY COVER-OUTER-CROSS SLIDE-1845
(1)
EA
A
R
PS
60
LU400450-1
WAY COVER-INNER-CROSS SLIDE-1845
(1)
EA
A
R
PS
61
LU400450-2
SPRING-COVER-CROSS SLIDE-1845
(2)
EA
A
R
PS
SOUTHWESTERN INDUSTRIES, INC.
2615 HOMESTEAD PLACE, RANCHO DOMINGUEZ, CA. 90220
1-310-608-4422 Fax 1-310-764-2668
29533
4
Page 2 of