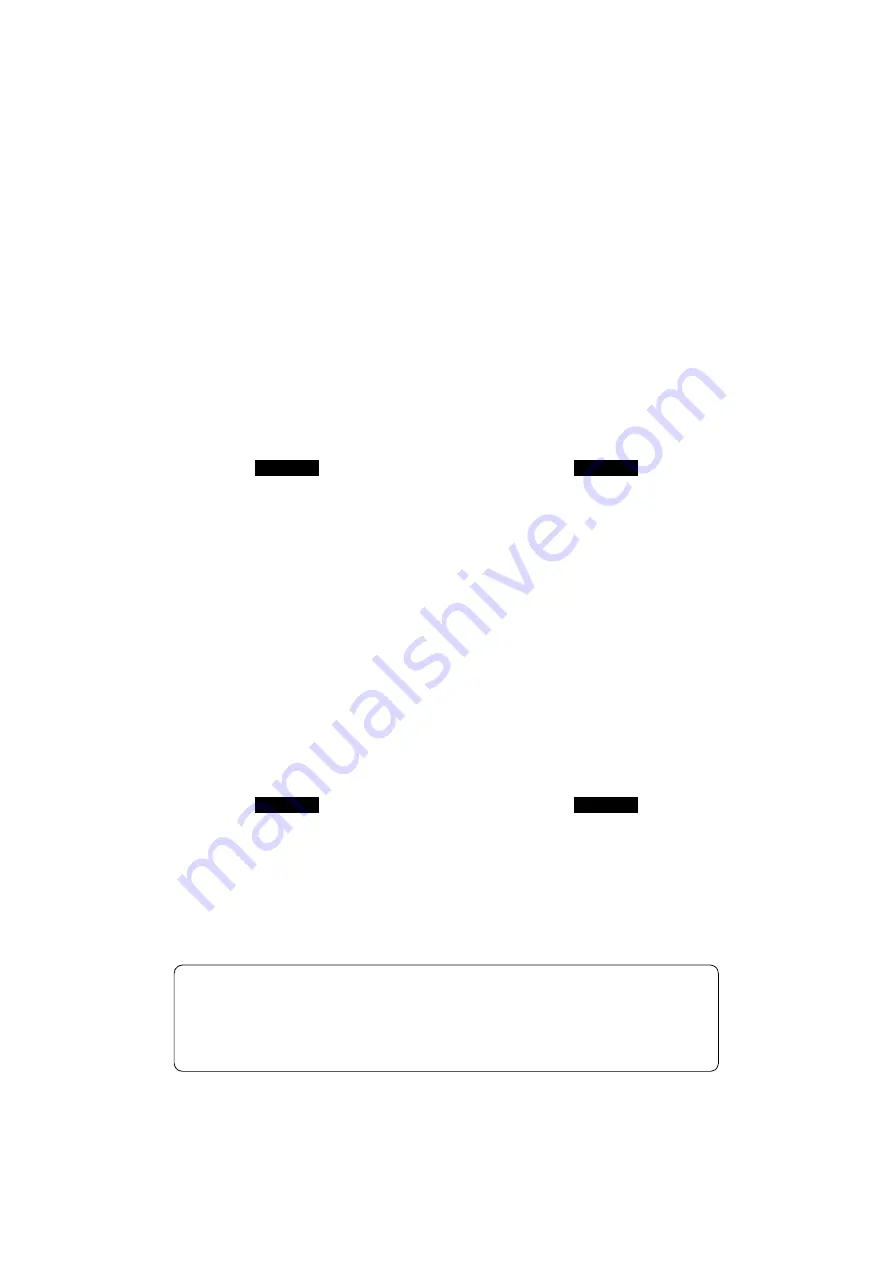
OPERATION MANUAL
Applicable Model
ZL-153
ZL-153S
ZL-153MC
ZL-153SMC
ZL-203
ZL-203S
ZL-203MC
ZL-203SMC
ZL-253
ZL-253S
ZL-253MC
ZL-253SMC
Before starting operation, maintenance, or programming, carefully read the
manuals supplied by Mori Seiki, the NC unit manufacturer, and equipment
manufacturers so that you fully understand the information they contain.
Keep the manuals carefully so that they will not be lost.
Applicable NC Unit
MSG-501
OM-ZLFMSG501-A0E