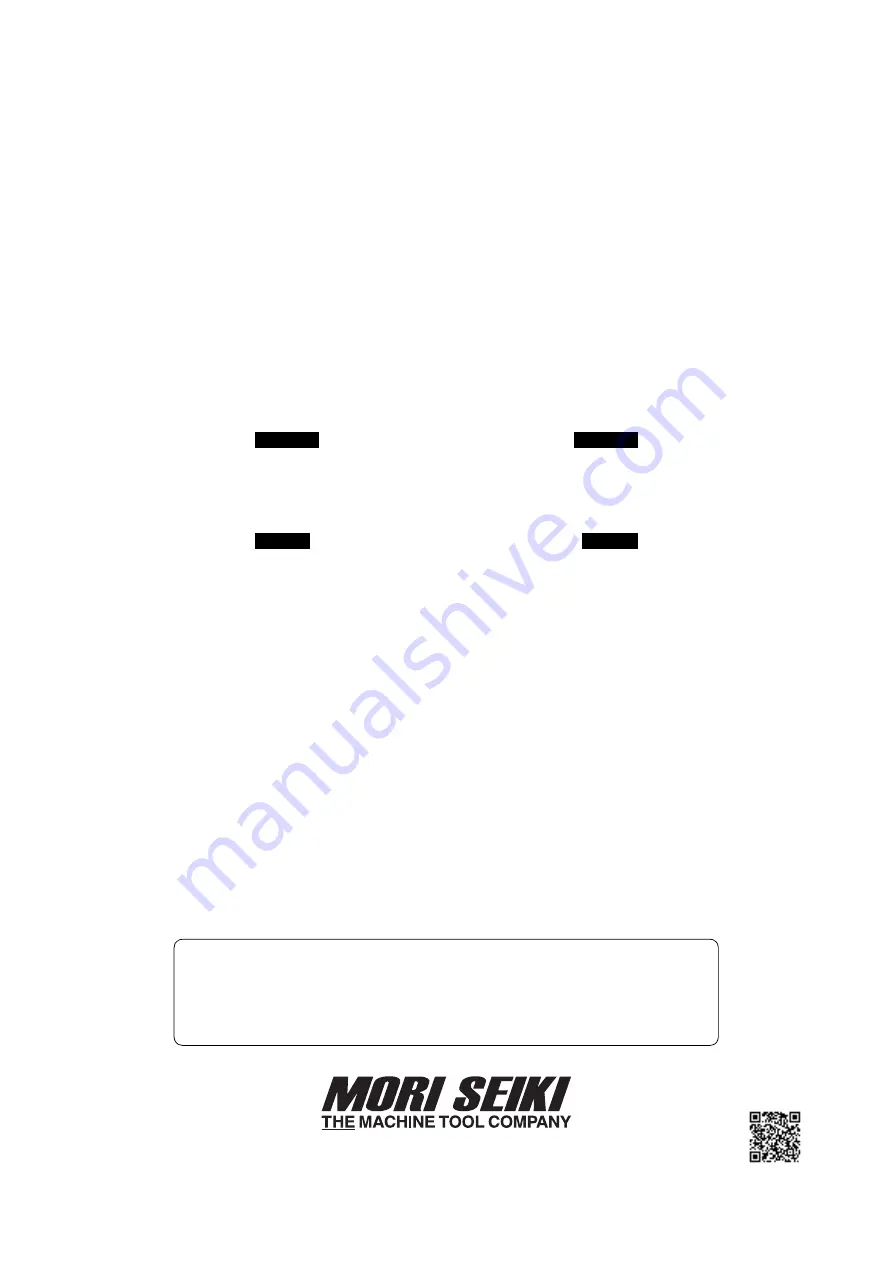
Applicable Model
NC LATHES
Before starting operation, maintenance, or programming, carefully read the
manuals supplied by Mori Seiki, the NC unit manufacturer, and equipment
manufacturers so that you fully understand the information they contain.
Keep the manuals carefully so that they will not be lost.
MM-CENL-H2EN
Applicable NC Unit
MSC-500
MSX-511
MSC-801
MSG-500
MSX-511III MSC-802
MSX-500
MSC-515
MSC-803
MSX-500III MSD-515
MSG-803
MSC-501
MSC-516
MSX-803
MSD-501
MSD-516
MSX-803III
MSD-501II MSD-516II MSG-805
MSG-501
MSC-518
MSX-805
MSX-501
MSD-518
MSX-805III
MSX-501III MSD-518II MSG-806
MSG-502
MSC-521
SEICOS
Σ
21L
MSX-502
MSC-700
MSX-502III MSC-701
MAINTENANCE MANUAL
The manuals for maintenance are comprised of the following
three manuals including this manual:
MAINTENANCE MANUAL, MAINTENANCE INFORMATION,
and INSTALLATION MANUAL.