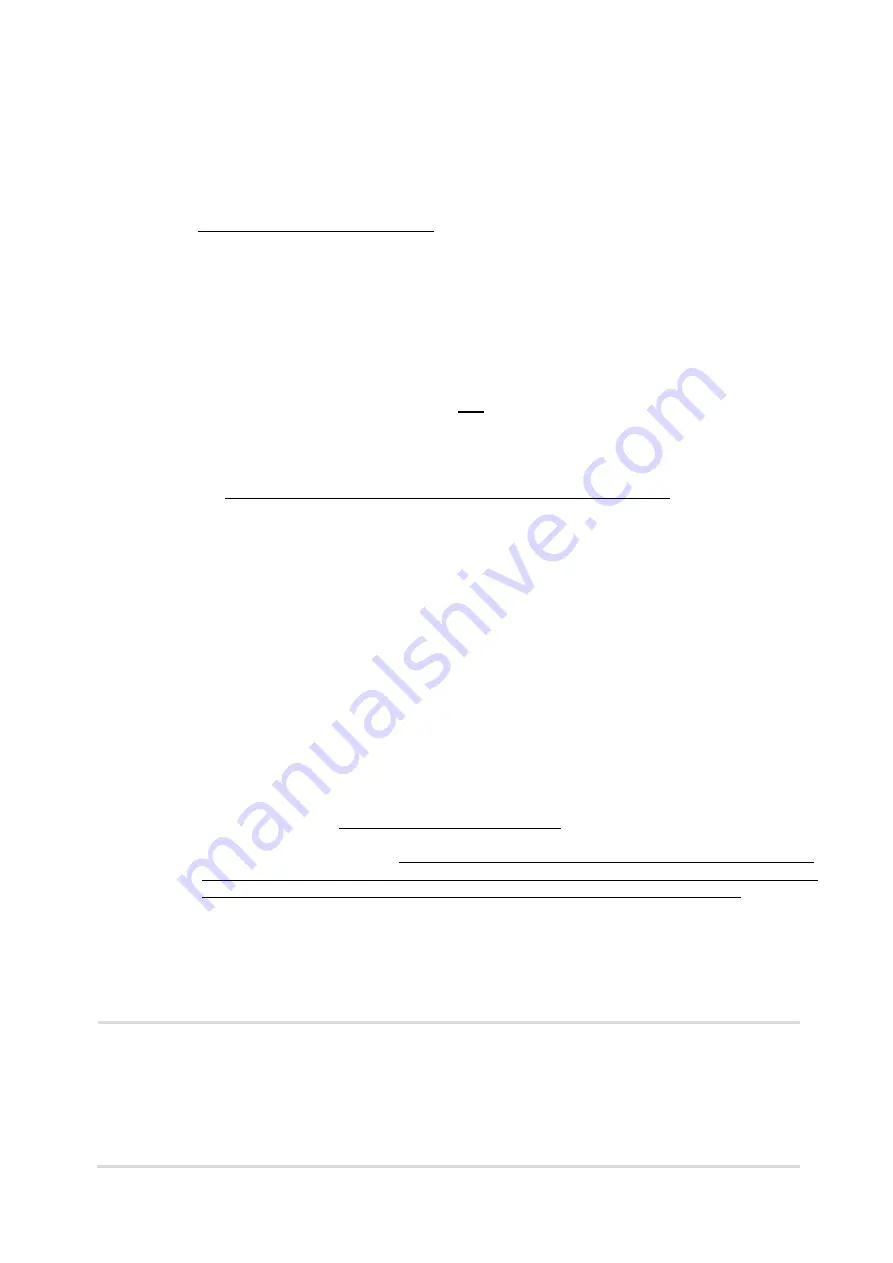
Operator’s manual for the Pentruder MD1 Modular Drill System with MDU9 Modular Drive Unit - Original instructions
Page 39
5.2.7
Drilling at an angle
When drilling at an angle it is important to only use a low feeding power until the whole drill bit
diameter is in the drilled material. See also 5.2.9 Drilling with a big or long drill bit.
5.2.8
Drilling through iron
When hitting iron, we recommend keeping the spindle speed as it is or just turn it down a little and
use less feeding power than in concrete. Make sure that the water flow is quite high when drilling
in iron. By using less feeding power but relatively high speed and having enough water, the drill
bit will not be overloaded.
5.2.9
Drilling with a big or long drill bit
When drilling with a big or long drill bit a big and heavy body is in movement which contains a lot
of energy when rotating. Therefore it is crucial to assemble the drilling machine following the
instructions given in this operator’s manual. The following are steps which are extra important
when drilling with a big or long drill bit.
1.
Fasten the base plate securely with two anchors
of preferable M16 size, or minimum
M12. Otherwise the base can twist under load and cause misalignment between drill bit and
hole.
2.
Tighten all bolts
on the base plate, the rear support and the track / column.
Do not overtighten the two bolts that clamps the track to the base plate. If over tightened, the
track T-slot can be deformed, and then the base-to-track stability is compromised.
3.
Make sure the carriage is properly adjusted to the track / column.
This will eliminate
play.
CE1-70 carriage for square column: See page 21, 4.4.3 Mounting of carriage CE1 on 70 mm
column.
CER-M3-MD1 roller carriage: See page 26, 4.5.4 Mounting of CER carriage, roller type
carriage with manual feed.
CEG-M25 carriage, make sure the three clamp nuts are firmly tightened, but not solid. Clean
and lubricate the steel liner on the track and the green nylon slide on the carriage before
drilling is started.
4.
Clean and lightly grease
the Quick disconnect coupling on the ST3 Spindle Unit (if a QDC
is used), both QDC-adapter and the threads in the drill bit thread adapter (if used). If a fixed
spindle is used this should also be cleaned and lightly greased as well as the thread on the
drill bit or thread adapter (if used).
5.
Start approaching the wall with the drill bit, with a much reduced speed of the drill bit
by using a low gear. Do not use full speed to start with. It is necessary to be very gentle
when the drill bit is fed into the wall. The first 10 mm are crucial for successful drilling when
the drill bit plunges further in. If the drill bit starts with a misalignment, than this misalignment
will grow the deeper the drill goes, ending up in a lot of friction between the drill bit inside and
outside wall, and the hole. It is crucial to get a very good alignment from the start. If the
alignment is good, then the friction between the drill bit and the hole will be greatly reduced,
and the torque needed to drill the hole will be much lower. This will minimize problems with
twisting of the track/column.
6.
Drill gently for at least the first 10 – 20 mm, or more
, then full speed can be applied.
When the drill bit has penetrated about 10 - 20 mm into the wall, full speed can be applied.
!
Important!
•
Please remember that the MG41 and ST2 puts out enormous torque
(see chart on page 46), and with an operator which is not used to
this high torque, there will be problems with twisting of the
track/column.
•
The motor will not stop because of the high drill pressure, it will drive
the drill bit with very high torque and the result will be a twist in the
track, and misalignment of drill bit in relation to the hole.