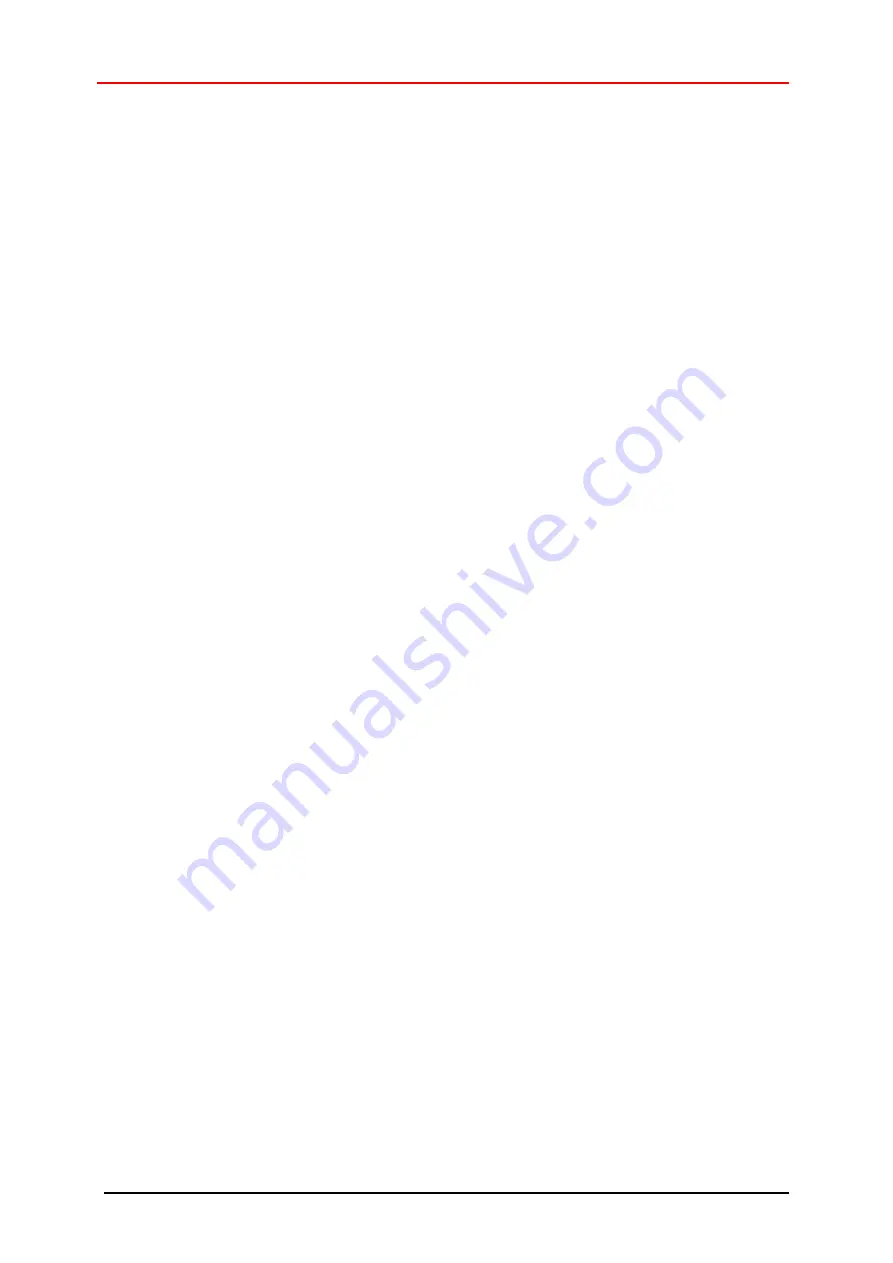
Basic safety information
TR-Electronic GmbH 2022, All Rights Reserved
Printed in the Federal Republic of Germany
Page 12 of 35
TR-EMO-BA-GB-0023 v00
04/20/2022
2.6 Conditions
Optional attachments, such as e.g. mechanical brakes, are not designed in accordance with the re-
quirements on functional safety and are therefore not part of the safety functions
STO (Safe Torque Off) or SS1 (Safe Stop 1).
In the event of malfunction, overrunning of the drive can be significantly prolonged or the drive can
even accelerate. To ensure an active delay of the system, an additional braking system must be pro-
vided.
In safe condition, message output C1 = 24 VDC and drive torque-free, the end stage is blocked by the
internal connection. Operating voltage is still supplied to the drive. The power to the system must
therefore be switched off, when working on the electrical part of the drive.
The prerequisite for safe operation is correct fitting of the drive in the system/ machine. In all cases,
the system/machine manufacturer must perform a system/machine-specific risk assessment.
The system/machine manufacturer and the operator are responsible for ensuring that the system or
machine complies with the applicable safety requirements.
As proof, the system or machine must be validated by the manufacturer in respect of the safety func-
tions.
All requirements on installation, commissioning and operation must be fulfilled for correct fitting of the
drive in the system. These are specified in the respective documents/chapters.
2.7 Integrated safety functions
2.7.1 Mode of operation
A redundant shutdown path is opened with the help of the integrated safety functions Safe Torque Off
(STO) or Safe Stop (SS1) through opening of the control circuit I11/I12 or I11/I21. No further torque
can be generated and the motor shaft is switched torque-free.
The safety function SS1 also enables an automatic torque switch-off with a time delay.
The following states are signaled to the higher-level control system via message outputs C1 and C2:
C1 = 24 VDC: safe state, the drive is torque-free.
C2 = 24 VDC: Error in safety module
Via PROFINET the safe state is displayed by ERROR “400“ in PNU 947.
In addition, the drive and safety states are signaled by corresponding LEDs.
It is guaranteed that an individual error will not lead to loss of the safety function. Internal errors are
detected by means of cyclic self-monitoring, at the latest when the system is next switched off and on
again. Depending on the application, this must be performed periodically as part of a maintenance
plan.
The integrated safety function enables the user to safely prevent motor generation of torque. The fol-
lowing functions are implemented in this connection: