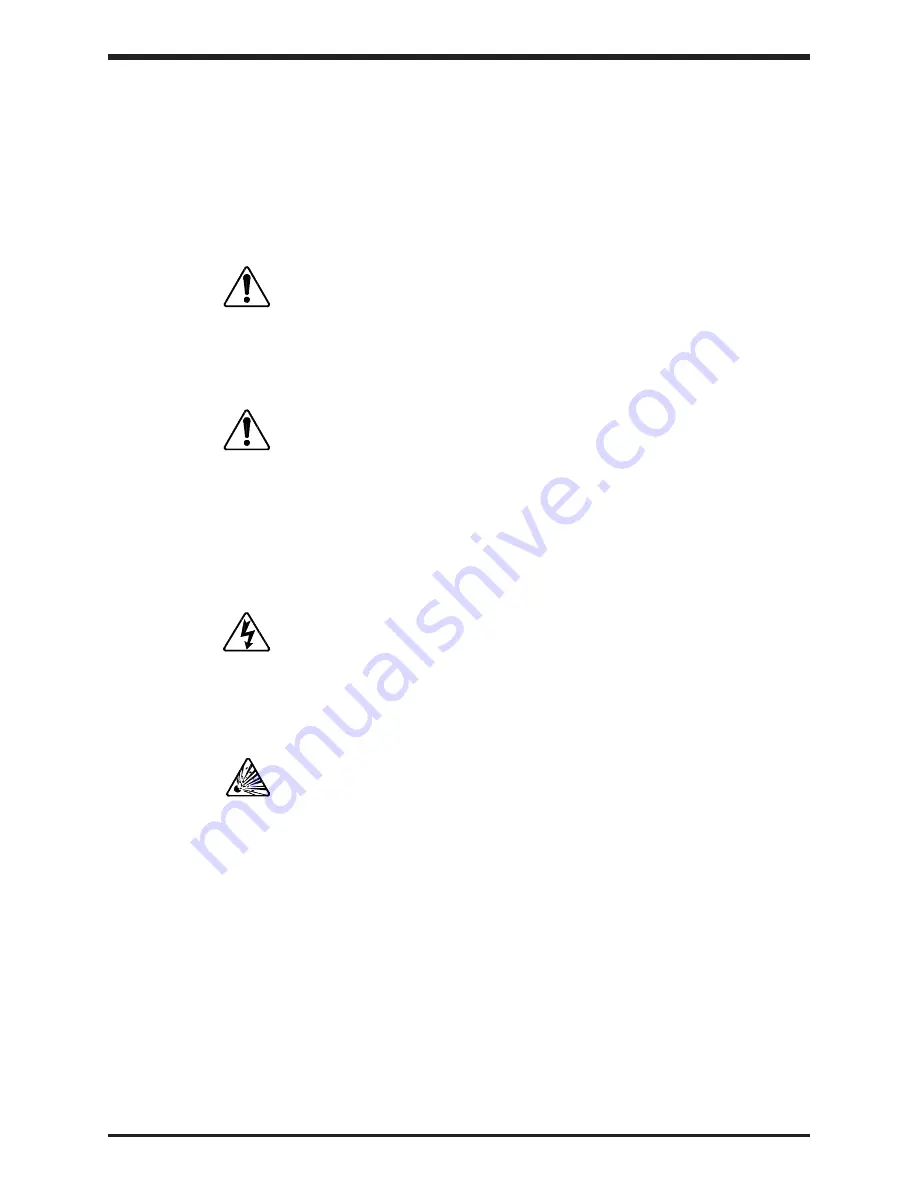
TOSHIBA
GENERAL SAFETY INSTRUCTIONS
Safety Symbols appear in this manual in the following ways:
1)
Danger symbol - The danger symbol is an exclamation mark enclosed in a triangle which
precedes the 3/16" high letters spelling the word "DANGER". The Danger symbol
indicates an imminently hazardous situation which, if not avoided, will result in death or
serious injury. This signal word is to be limited to the most extreme situations:
2)
Caution symbol - The caution symbol is an exclamation mark enclosed in a triangle which
precedes the 3/16" high letters spelling the word "CAUTION". The Caution symbol
indicates a potentially hazardous situation which, if not avoided, may result in minor or
moderate injury. It may also be used to alert against unsafe practices:
Other
warning symbols may appear along with the Danger and Caution symbol and are used to indicate
a potentially hazardous situation which, if not avoided, could result in death or serious injury:
1)
Electrical warnings - The electrical warning symbol is a lighting bolt mark enclosed in
a triangle. The Electrical warning symbol is used to indicate high voltage locations and
conditions that may cause serious injury or death if the proper precautions are not
observed:
iii
DANGER
CAUTION
2)
Explosion warnings - The explosion warning symbol is an explosion mark enclosed in
a triangle. The Explosion warning symbol is used to indicate locations and conditions
where molten, exploding parts may cause serious injury or death if the proper
precautions are not observed:
For the purpose of this manual and product labels, a
Qualified Person is one who is familiar with the
installation, construction, operation and maintenance of the equipment and the hazards involved. In
addition, this person must:
1)
Carefully read the entire operation manual.
2)
Be trained and authorized to safely energize, de-energize, clear faults, ground, lockout
and tag circuits and equipment in accordance with established safety practices.
3)
Be trained in the proper care and use of protective equipment such as safety shoes,
rubber gloves, hard hat, safety glasses, face shields, flash clothing, and etc. in
accordance with established safety practices.
4)
Be trained in rendering first aid.
efesotomasyon.com -Toshiba inverter,drive,servo,plc