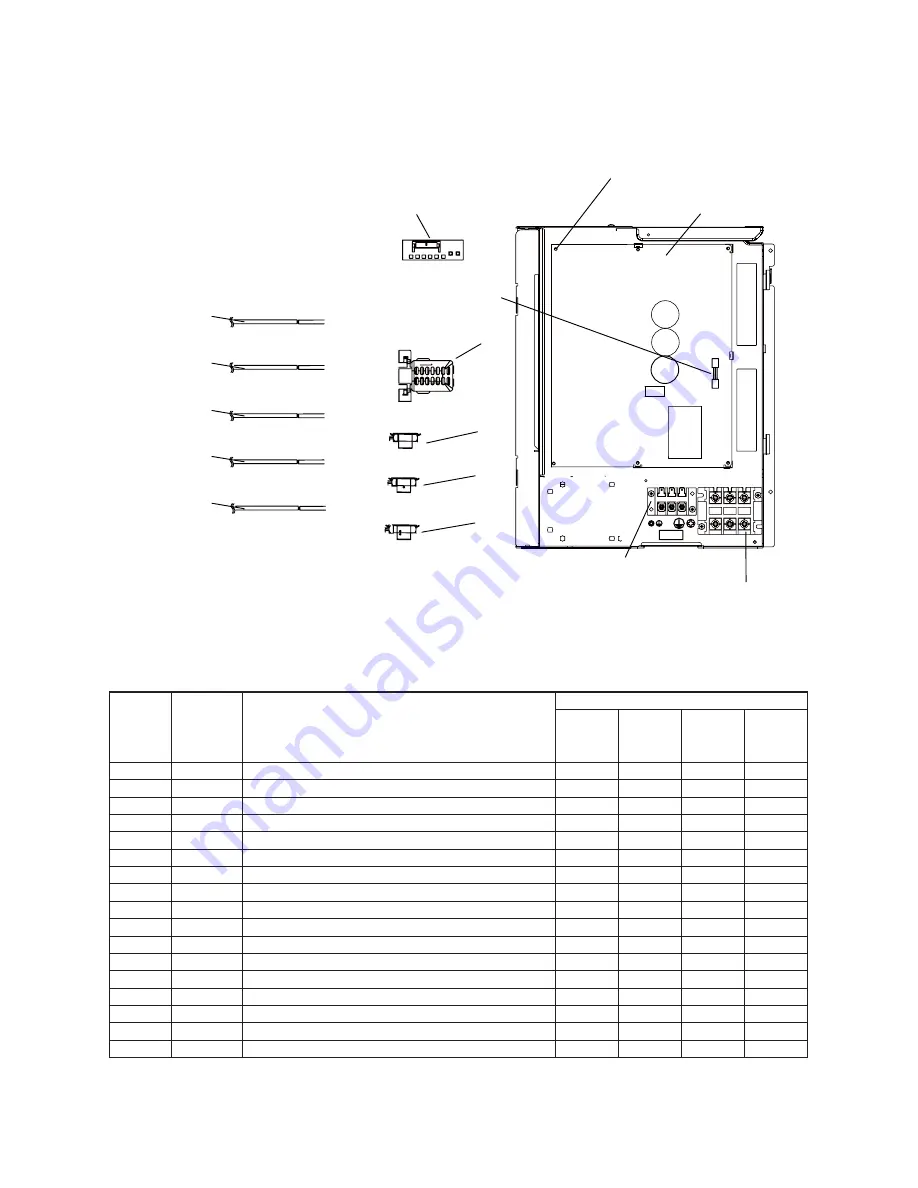
– 124 –
14-2. Inverter Assembly
703
704
705
706
707
PC BOARD A
SS
Y, MCC-1646
702
HOLDER,
S
EN
S
OR(TO)
70
9
710
HOLDER,
S
EN
S
OR(TE)
716
717
S
PACER, COLLAR
S
PACER, BU
S
H
701
714
TERMINAL BLACK,3P 20A
715
TERMINAL BLACK,3P 60A
713
711
HOLDER,
S
EN
S
OR(TD)
712
HOLDER,
S
EN
S
OR(T
S
)
S
EN
S
OR, TD
S
EN
S
OR, TL
S
EN
S
OR, TE
S
EN
S
OR, TO
S
EN
S
OR, T
S
FU
S
E(10A)
PC BOARD A
SS
Y, MCC-1705
70
8
Location
No.
Part No.
Q’ty/Set RAV-GP
701
702
70
3
704
705
706
707
708
709
710
711
712
71
3
714
715
716
717
4
3
16V659
4
3
16V550
4
3
150
3
51
4
3
150
3
55
4
3
150
3
59
4
3
150
3
69
4
3
150
3
70
4
3
150
3
5
3
4
3
16
3
055
4
3
F6
33
25
4
3
F6
33
21
4
3
F6
33
22
4
3
160589
4
3
160607
4
3
160609
4
3
16
3
059
4
3
16
3
066
PC BOARD ASSY, MCC-1705
PC BOARD ASSY, MCC-1646, DS
SENSOR, TD
SENSOR, TL
SENSOR, TE
SENSOR, TO
SENSOR, TS
SENSOR, TS
HOLDER, SENSOR (TO)
HOLDER, SENSOR (TE)
HOLDER, SENSOR (TD)
HOLDER, SENSOR (TS)
FUSE, 10A
TERMINAL BLOCK,
3
P, 20A
TERMINAL BLOCK,
3
P, 60A
SPACER, BUSH
SPACER, COLLAR
801AT-E
801AT-TR 801ATJ-E
1101AT-E
1401AT-E
1101AT-TR
1401AT-TR
1101ATJ-E
1401ATJ-E
1
1
1
1
1
1
1
1
1
1
1
1
1
1
1
1
1
1
1
1
1
1
1
1
1
1
1
1
1
1
1
1
1
1
1
1
1
1
1
1
1
1
1
1
1
1
1
1
1
1
1
1
1
1
1
1
1
1
1
1
Description
Summary of Contents for RAV-GM 1101UT-E
Page 30: ... 30 2 CONSTRUCTION VIEWS EXTERNAL VIEWS 2 1 RAV GP801AT ...
Page 31: ... 31 2 2 RAV GP1101AT GP1401AT ...
Page 36: ... 36 4 WIRING DIAGRAM 4 1 RAV GP801AT 220 240V 50Hz P 3 3 Fuse 25A 250V Fuse 10A 250V ...
Page 37: ... 37 4 2 RAV GP1101AT GP1401AT 220 240V 50Hz P 3 3 3 Fuse 25A 250V Fuse 10A 250V ...