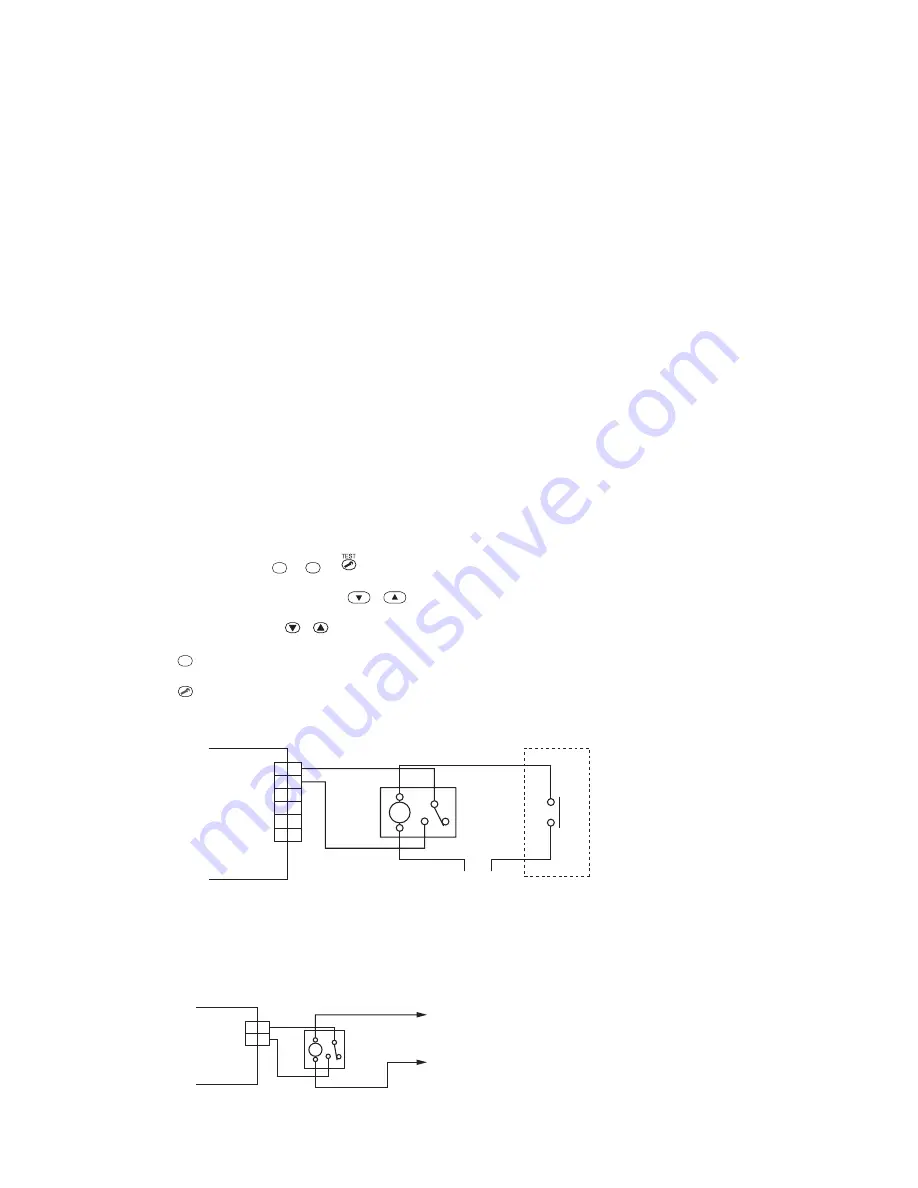
– 35 –
Leaving-ON prevention control
[Function]
• This function controls the indoor units individually. It is connected with cable to the control P.C. board of
the indoor unit.
• In a group control, it is connected with cable to the indoor unit (Control P.C. board), and the CODE No.
2E
2E
2E
2E
2E
is set to the connected indoor unit.
• It is used when the start operation from outside if unnecessary but the stop operation is necessary.
• Using a card switch box, card lock, etc, the forgotten-OFF of the indoor unit can be protected.
• When inserting a card, start/stop operation from the remote controller is allowed.
• When taking out a card, the system stops if the indoor unit is operating and start/stop operation from the
remote controller is forbidden.
1. Control items
1) Outside contact ON : The start/stop operation from the remote controller is allowed.
(Status that card is inserted in the card switch box)
2) Outside contact OFF : If the indoor unit is operating, it is stopped forcedly.
(Start/Stop prohibited to remote controller)
(Status that card is taken out from the card switch box)
* When the card switch box does not perform the above contact operation, convert it using a relay with b
contact.
2. Operation
Handle the wired remote controller switch in the following procedure.
* Use the wired remote controller switch during stop of the system.
1
Push concurrently
SET
+
CL
+
buttons for 4 seconds or more.
2
Using the temperature setup
/
button, specify the CODE No.
2E
2E
2E
2E
2E
.
3
Using the timer time / button, set
0001
0001
0001
0001
0001
to the setup data.
4
Push
SET
button.
5
Push
TEST
button. (The status returns to the usual stop status.)
3. Wiring
Power peak-cut from indoor unit
When the relay is turned on, a forced thermostat-OFF operation starts.
1
2
1
2
3
4
3
4
5
6
5
6
CN61
T10
(YEL)
Relay (procured locally)
Indoor control P.C. board
Note) Determine the cable length between the indoor control P.C. board and the relay within 2m.
* In the figure, the contact indicates
a status that the card is taken out.
Power supply
Outside contact (Card switch box, etc: Procured locally)
1
2
1
2
EXCT
(2P plug: RED)
CN73
Relay (procured locally)
Note) Determine the cable length between the indoor or
outdoor control P.C. board and the relay within 2m.
Relay coil signal
Indoor control P.C. board
• Wiring example