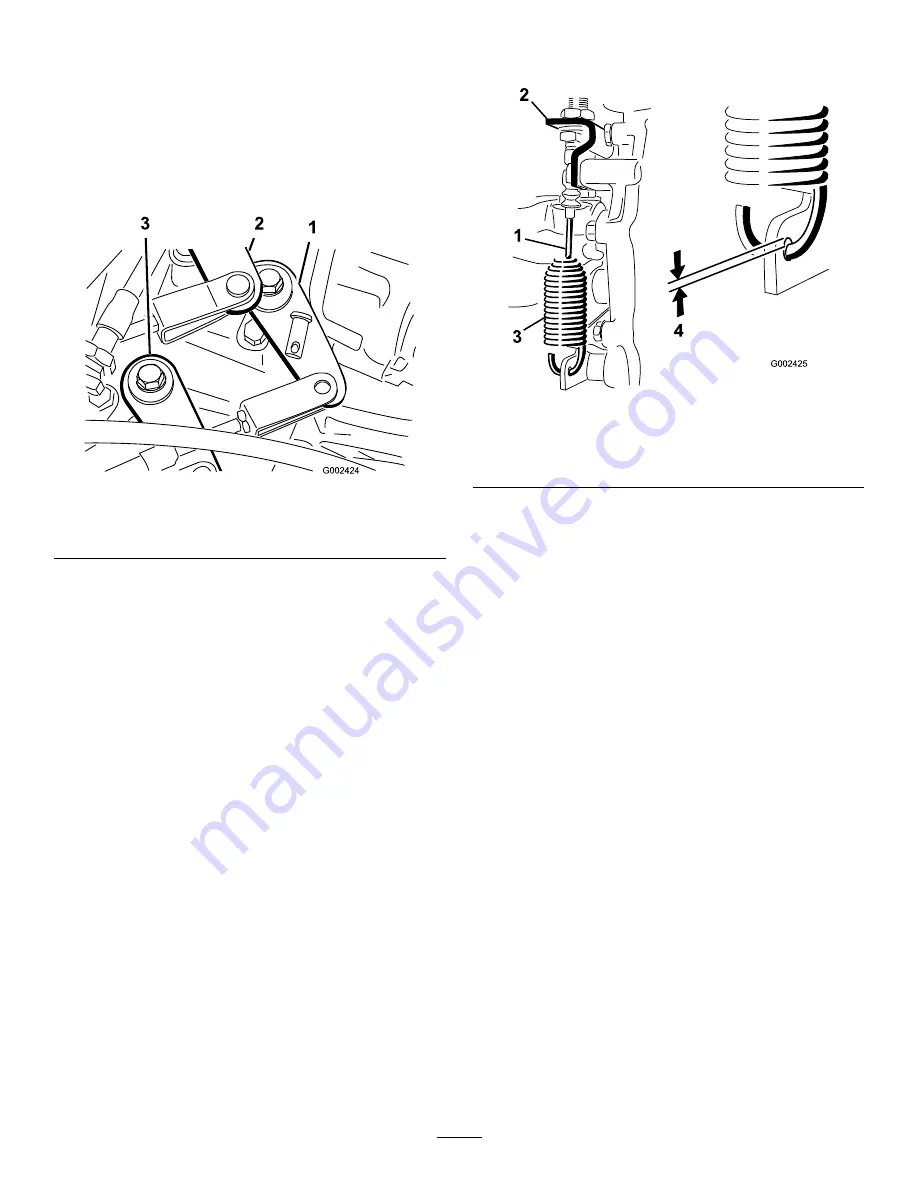
Adjusting the Shift Cables
Service Interval:
After the first 10 hours
Every 200 hours
1. Move shift lever to the Neutral position.
2. Remove the clevis pins securing the shift cables to
the transaxle shift arms (Figure 55).
Figure 55
1.
Shift arm (1st—Rev.)
3.
Shift arm (High—low)
2.
Shift arm (2nd—3rd)
3. Loosen the clevis jam nuts and adjust each clevis
so cable free play is equal forward and backward
relative to the hole in the transaxle shift arm (with
the transaxle lever free play taken up in the same
direction).
4. Install the clevis pins and tighten the jam nuts when
finished.
Adjusting the High–Low Cable
Service Interval:
Every 200 hours
1. Remove the clevis pin securing the High–Low cable
to the transaxle (Figure 55).
2. Loosen the clevis jam nut and adjust the clevis
so that the clevis hole aligns with the hole in the
transaxle bracket.
3. Install the clevis pin and tighten the jam nut when
finished.
Adjusting Differential Lock
Cable
Service Interval:
Every 200 hours
1. Move the differential lock lever to the Off position.
2. Loosen the jam nuts securing the differential lock
cable to the bracket on the transaxle (Figure 56).
Figure 56
1.
Differential lock cable
3.
Spring
2.
Transaxle bracket
4.
0.01 to 0.06 inch (0.25 to
1.5 mm) gap
3. Adjust the jam nuts to obtain a 0.01 to 0.06 inch
(0.25 to 1.5 mm) gap between the spring hook and
the O.D. of the hole in the transaxle lever.
4. Tighten the jam nuts when finished.
Inspecting the Tires
Service Interval:
Every 100 hours
Operating accidents, such as hitting curbs, can damage a
tire or rim and also disrupt wheel alignment, so inspect
tire condition after an accident.
Check the tire pressure frequently to ensure proper
inflation. If the tires are not inflated to the correct
pressure, the tires will wear pre maturely.
Figure 57 is an example of tire wear caused by under
inflation.
47