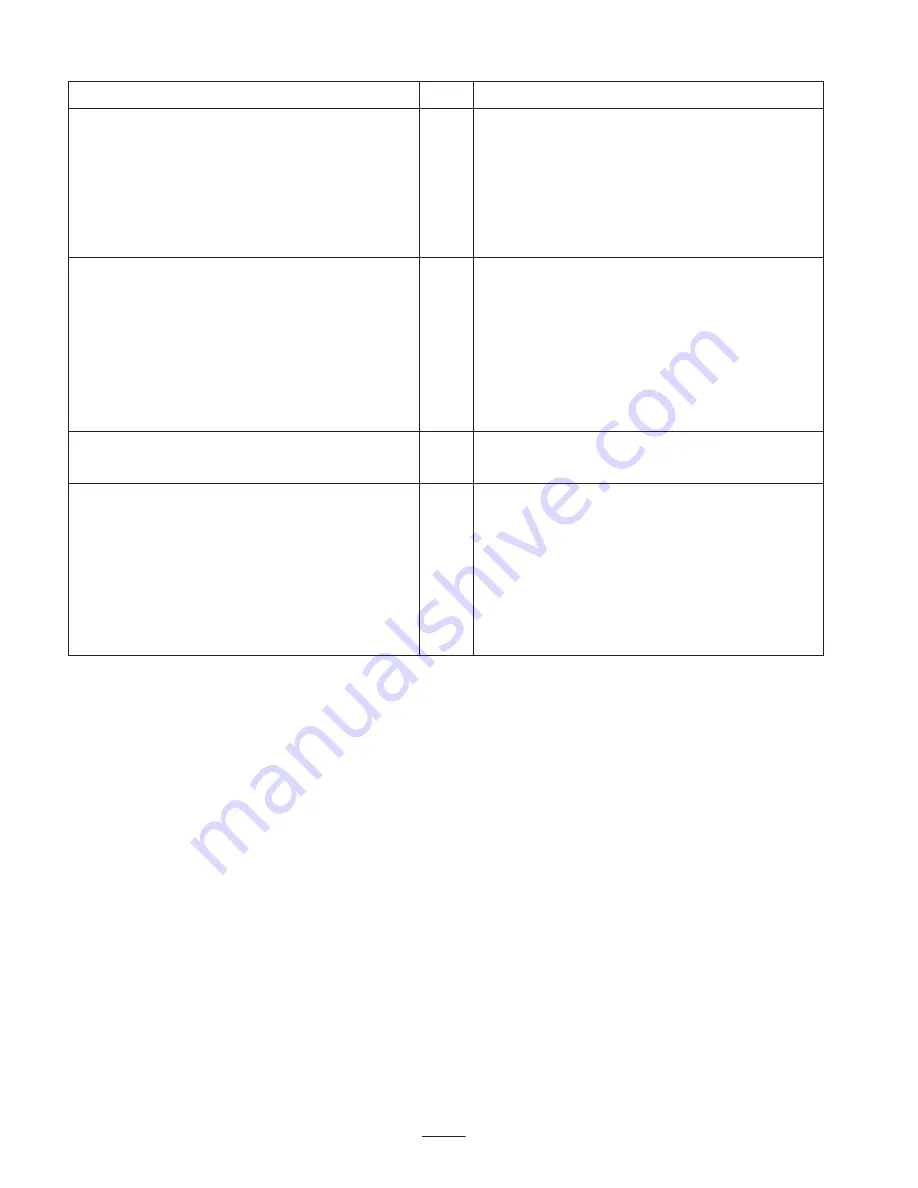
8
Description
Use
Qty.
Hopper Assembly
Welded Mounting Pin
Hair Pin Cotter – for 1/2” Shaft
Hair Pin Cotter – for 1/4” Shaft
Carriage Bolt 5/16 – 18 x 1” Ig.
Flange Locknut 5/16–18
1
2
2
2
2
2
Install Hopper Assembly
Shield – Top
Shield – Wide
Shield – Narrow
Flat – Short
Flat – Long
Screw #10 – 24 x 1” Ig.
Flange Nut #10 – 24
1
1
1
1
2
8
8
Install in Chute Opening of Hopper
Decal – Warning
Decal – Valve Operation
1
1
Mount on Seat Frame
Wheel Weight
Threaded Rod
Lockwasher
Flatwasher
Hex Nut
Installation Instructions
Parts Catalog
1
2
4
2
6
1
1
Mount to Left Wheel
Note: Refer to Traction Unit Operator’s Manual for left
side weight requirements.
Optional Equipment
Bracket Kit
Weight Kit
Part No. 92–9670
Part No. 24–5780
Summary of Contents for Groundsmaster 200 Series
Page 19: ...19...