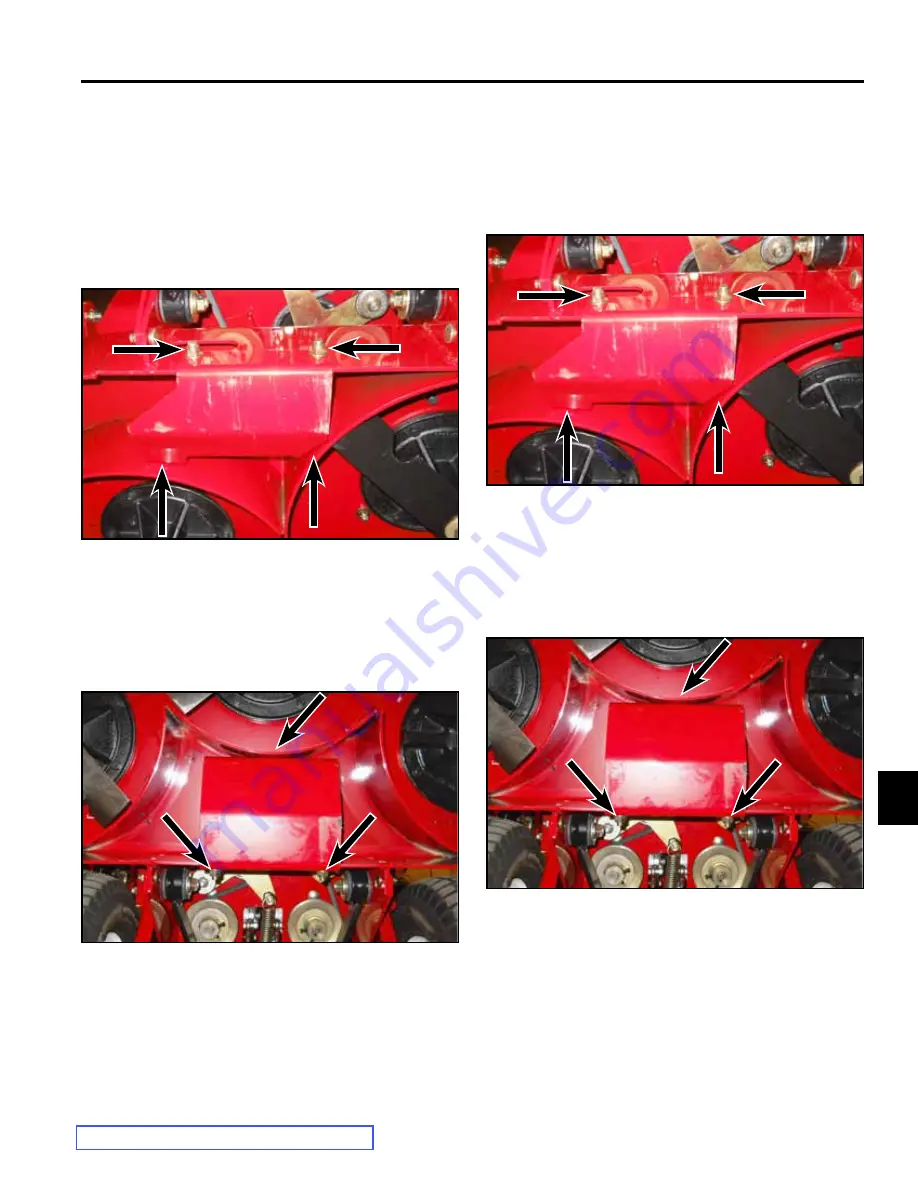
MOWER DECK
7-33
36” & 40” Toro GrandStand Service Manual
7
Skid Plate Removal
Skid Plate Installation
2.
40” Deck Only:
Secure the skid plate to the mower
deck using the three sets of carriage bolts and nuts
(Fig. 663).
1. Raise the machine to access the underside of the
mower deck.
2.
36” Deck Only:
Remove the four sets of carriage
bolts and nuts securing the skid plate to the mower
deck (Fig. 660).
1.
36” Deck Only:
Secure the skid plate to the mower
deck using the four sets of carriage bolts and nuts
(Fig. 662).
Fig. 660
DSCN-3502a
3.
40” Deck Only:
Remove the three sets of carriage
bolts and nuts securing the skid plate to the mower
deck (Fig. 661).
Fig. 661
DSCN-3310a
Fig. 662
DSCN-3502a
Fig. 663
DSCN-3310a
Summary of Contents for GrandStand 74534
Page 1: ...Toro 36 40 GrandStand Service Manual LCE Products ...
Page 3: ...ABOUT THIS MANUAL THIS PAGE INTENTIONALLY LEFT BLANK ...
Page 9: ...TABLE OF CONTENTS vi 36 40 Toro GrandStand Service Manual THIS PAGE INTENTIONALLY LEFT BLANK ...
Page 67: ...CHASSIS 3 48 36 40 Toro GrandStand Service Manual 3 THIS PAGE INTENTIONALLY LEFT BLANK ...
Page 111: ...CONTROLS 4 44 36 40 Toro GrandStand Service Manual 4 THIS PAGE INTENTIONALLY LEFT BLANK ...
Page 133: ...ENGINE 5 22 36 40 Toro GrandStand Service Manual 5 THIS PAGE INTENTIONALLY LEFT BLANK ...
Page 265: ...ELECTRICAL 8 44 36 40 Toro GrandStand Service Manual 8 THIS PAGE INTENTIONALLY LEFT BLANK ...
Page 268: ...Toro 36 40 GrandStand Service Manual Form Number 492 9236 ...