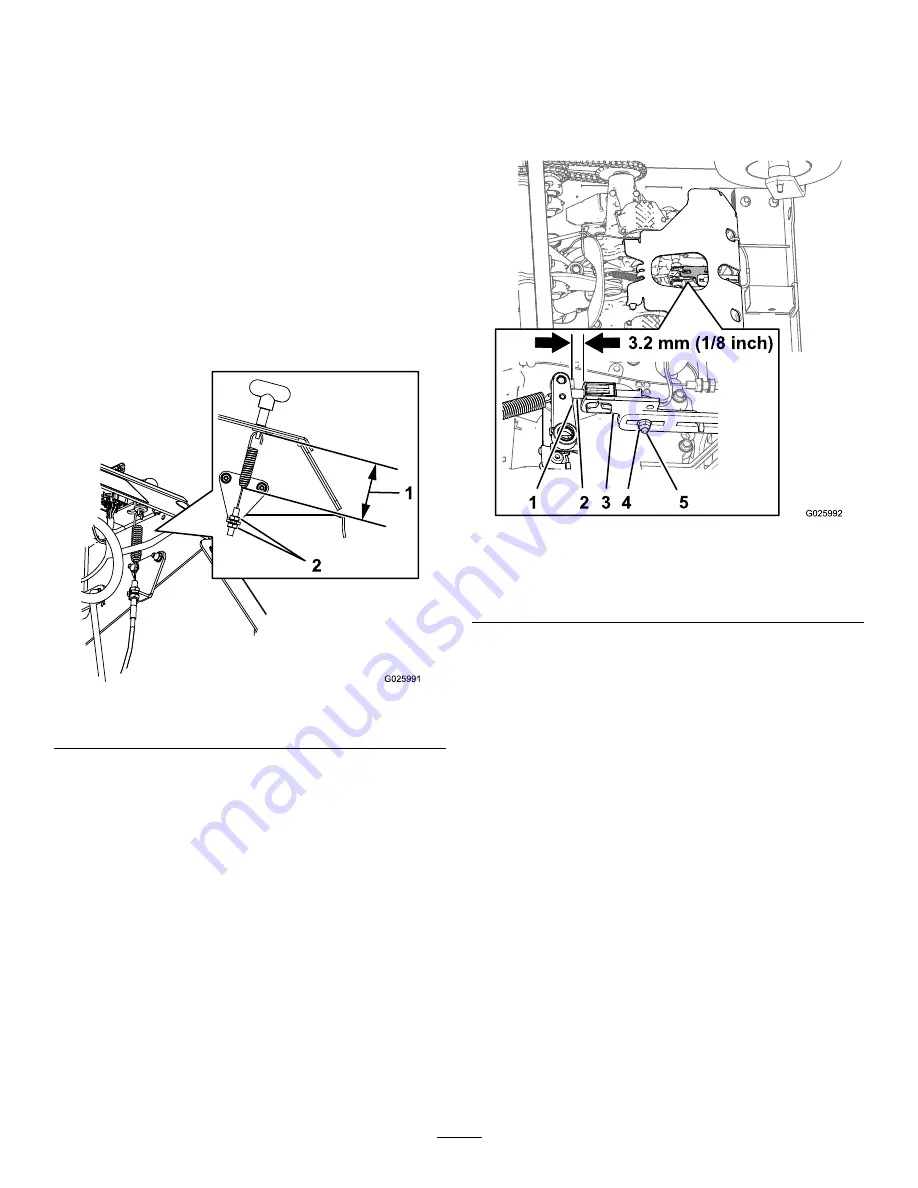
Brake Maintenance
Adjusting the Parking Brake
If the parking brake does not hold securely, an adjustment
is required.
1.
Park the machine on a level surface.
2.
Turn the key in the ignition switch to the O
FF
position
and wait for all moving parts to stop.
3.
Check the air pressure in the drive tires.
Note:
If needed, adjust to the recommended inflation;
refer to
Checking the Air Pressure in the Tires (page
.
4.
Loosen the jam nut on the brake cable under the
console (
).
Figure 52
1.
7.9 cm (3–1/8 inch)
5.
Set the parking brake (
).
6.
Adjust the jam nut position until 7.9 cm (3–1/8 inch)
from the bottom of the link to the bottom of the spring
(
).
7.
Secure the adjustment of the cable by tightening the
jam nuts (
8.
Check the parking brake; if necessary, repeat steps
through
Adjusting the Brake Switch
1.
Park the machine on a level surface.
2.
Turn the key in the ignition switch to the O
FF
position
and wait for all moving parts to stop.
3.
Prior to adjusting the brake switch, ensure the parking
brake is properly adjusted; refer to
Parking Brake (page 41)
.
4.
Set the parking brake.
5.
Check the distance between the parking brake-switch
bracket to the brake arm of the transmission (
Note:
The distance should be 3.2 mm (1/8 inch).
Figure 53
1.
Brake arm (transmission)
4.
Locknut
2.
Plunger (brake switch)
5.
Carriage bolt
3.
Brake-switch bracket
6.
If adjustment is required, preform the following:
A.
Loosen the locknut and carriage bolt securing the
parking brake switch bracket (
).
B.
Adjust the position of the brake-switch bracket
until the gap (
) between the switch
bracket and the brake arm is 3.2 mm (1/8 inch)
C.
Tighten the locknut and carriage bolt (
securing the brake-switch bracket to 1017 to 1243
N-cm (90 to 110 lb-in).
41
Summary of Contents for 23518
Page 53: ...Schematics Electrical Diagram Rev A 53...
Page 54: ...Electrical Schematic Rev A 54...
Page 55: ...Hydraulic Diagram Rev A 55...