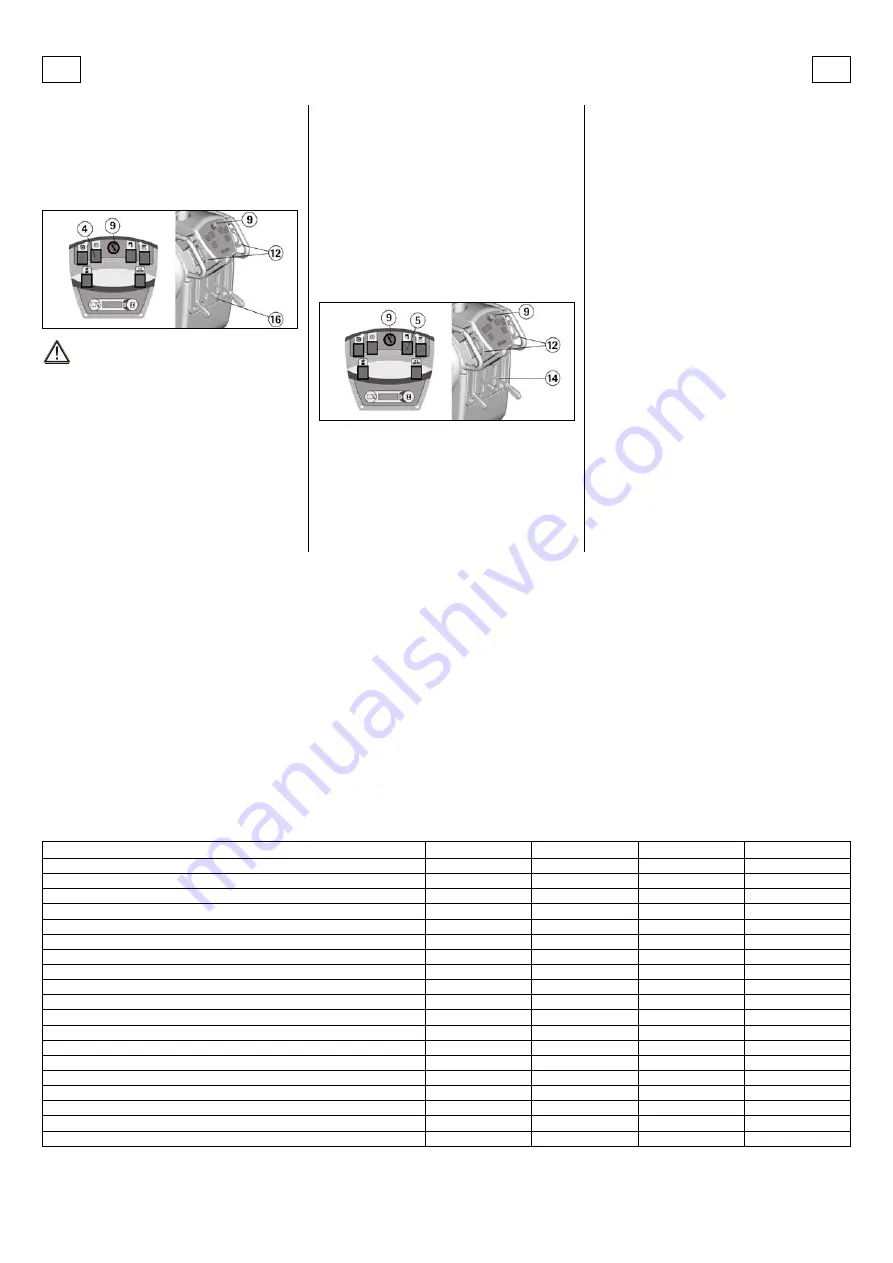
GB
GB
14
THE TRACTION MOTOR DOES NOT WORK
1. Switch off and on again the machine.
2. Release the brake (16) until the signal lamp (4)
comes off.
3. Act upon the levers drive control (12).
If the problem persists, please contact the authorized
technical assistance.
ATTENTION:
Never leave the batteries discharged for a long time.
THE DETERGENT SOLUTION ON THE BRUSHES IS
NOT SUFFICIENT
1. Check that the solution valve lever (14) is open.
2. Check the level of the liquid in the solution tank.
3. Check that solution filter is clean (see under par-
agraph “CLEANING OF THE SOLUTION FILTER”).
4. The machine is equipped with solenoid valve,
therefore act upon the levers drive control (12) to let
come down the detergent solution and check that
the signal lamp (5) comes on.
5. If the machine is equipped with the 3S system
(see under “3S SYSTEM SOLUTION SAVING SYSTEM”)
(optional), check that the switch of the detergent
solution supply is activated by choosing between the
traditional adjustment system through the solution
valve or the system of fixed optimum supply.
6. If the detergent solution still does not come
down, clean the filter inside the solution tank. Empty
the solution tank, remove the fitting of the water
outlet by taking off the two screws which fix it to
the tank. Clean the inside filtrating part of the fit-
ting from eventual dirt. Pour some water into the
tank and clean it. Reassemble the fitting onto the
solution tank.
If the problem persists, please contact the authorized
technical assistance.
THE MACHINE DOES NOT CLEAN PROPERLY
1. The brushes do not have the suitable bristle di-
mension: contact the authorized technical assistance.
2. The brushes have got worn bristles. Check the
brushes wear condition and eventually replace them
(the brushes have to be replaced when the bristles
have reached a height of about ½”/15mm).
To replace brushes, see instructions at paragraph
“BRUSHES DISASSEMBLY” and “BRUSHES ASSEMBLY”.
3. The detergent solution is insufficient: open more
the solution valve.
4. Check that the liquid detergent is in the recom-
mended percentage.
5. Increase the brushes base pressure (see at para-
graph "ADJUSTMENT OF THE BRUSHES PRESSURE").
Contact the authorized technical assistance for ad-
vice.
THE SQUEEGEE DOES NOT DRY PERFECTLY
1. Check that the squeegee rubbers are clean.
2. Check the adjustment of the height and the in-
clination of the squeegee (see section “ADJUSTMENT
OF THE SQUEEGEE” in “BEFORE USE”).
3. Check that the suction hose is correctly inserted
in the proper seat on the recovery tank.
4. Clean the suction filter.
5. Replace the rubbers if worn out.
6. Check that the suction motor switch is on.
EXCESSIVE FOAM PRODUCTION
Check that low foam detergent has been used. Even-
tually add small quantities of anti foam liquid into
the recovery tank.
Please be aware that a bigger quantity of foam is
produced when the floor is not very dirty. In this ca-
se please dilute detergent solution.
PROGRAMMED MAINTENANCE
INTERVENTION
DAILY
20 HOURS *
200 HOURS *
1000 HOURS *
RECOVERY TANK CLEANING
•
SUCTION FILTER CLEANING
•
SOLUTION TANK FILTER CLEANING
•
BRUSHES CLEANING
•
BRUSHES DISASSEMBLY AND CLEANING
•
SQUEEGEE CLEANING
•
FRONT SQUEEGEE RUBBER REPLACEMENT
•
REAR SQUEEGEE RUBBER REPLACEMENT
•
SPLASH GUARD RUBBER REPLACEMENT
•
CHECK SQUEEGEE ADJUSTMENT
•
SQUEEGEE HOSE CLEANING
•
SOLUTION TANK CLEANING
•
CHECK BATTERIES ELECTROLYTE
•
CHECK OF THE BRAKE
•
TRACTION MOTOR CHECK
•
BRUSHES MOTOR CHECK
•
SUCTION MOTOR CHECK
•
CHECK BRUSHES BASE GROUP
•
SCREW TIGHTENING
•
* The hours refer to the ones indicated on the display (see under paragraph ”HOUR METER").
Summary of Contents for 99732 BD 32/26
Page 2: ......