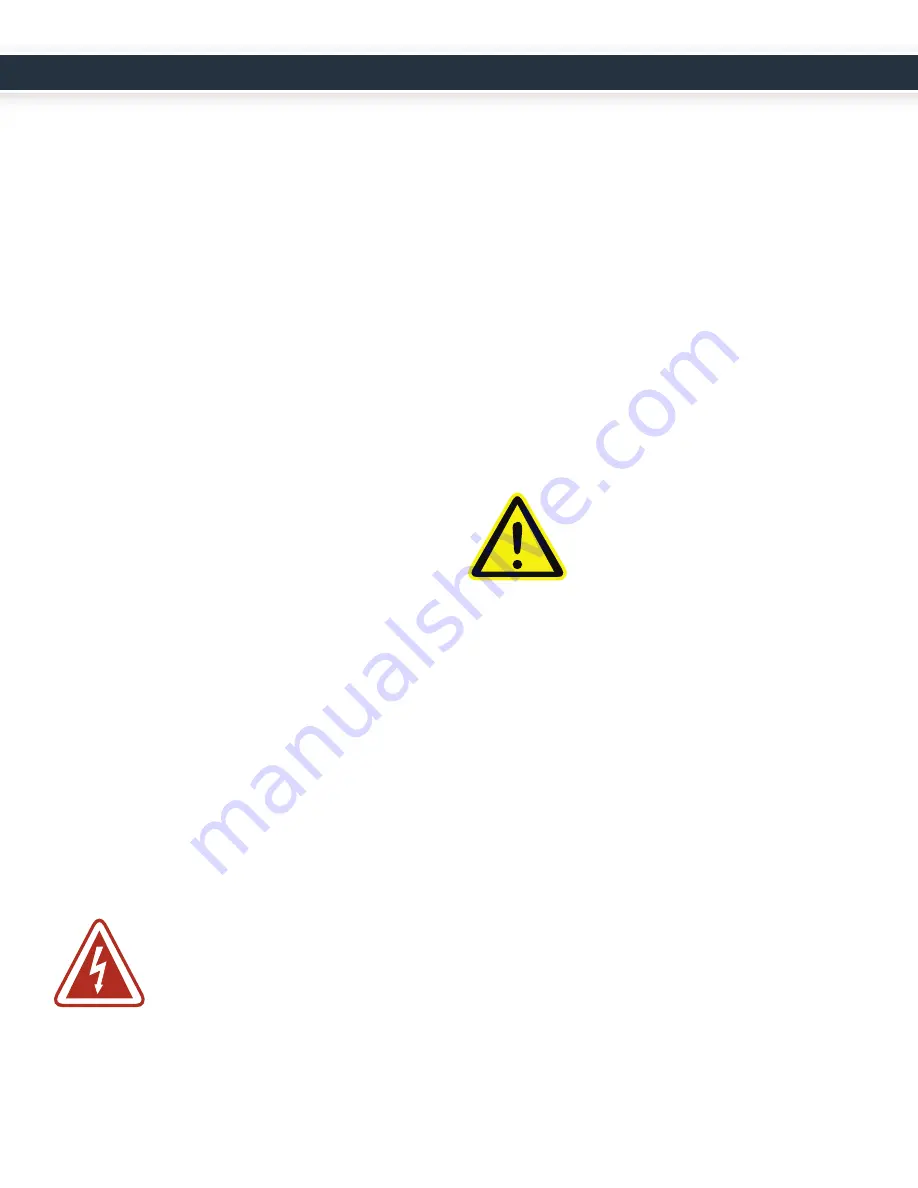
you:
a. Change tools;
b. Change parts or adjust the work piece;
c. Clear away chips or debris – always use a chip
scraper or brush;
d. Make an adjustment to the part, fixture, or take
measurements;
9.
Keep work area well lit. Ask for additional light if
needed.
10.
Use proper grinding wheels for the job.
11.
Chips and dust from certain materials (e.g.,
magnesium) can be flammable. Fine dust from
normally non-flammable materials can be flammable
or even explosive.
12.
Chips and dust from certain materials can be toxic.
Vapors from certain overheated materials can be toxic.
Always check a Materials Safety Data Sheet (MSDS) of
suspect materials. Refuse machining work requests of
unknown materials.
13.
If you are in any doubt you must seek guidance from a
professionally qualified expert rather than risk injury to
yourself or to others.
14.
Always stop the grinder and check to ensure the
machine is in stop mode before adjusting the tool or
work piece.
15.
Use adequate safeguarding around the operating
envelope.
It is the responsibility of the employer to provide and
ensure point of operation safeguarding per the following:
•
OSHA 1910.212 - General Requirements for All
Machines
•
ANSI B11.09-2010 Safety Requirements for Grinding
Machines
•
ANSI B11.TR3-2000 Risk Assessment and Risk
Reduction - A Guideline to Estimate, Evaluate, and
Reduce Risks Associated with Machine Tools
ELECTRICAL SAFETY
Power Input:
The power input should be
unplugged before working in the electrical
cabinet.
Grounding:
Power inputs must be grounded.
During installation it is not enough to assume that the
ground line of a wall outlet is properly grounded. Check
continuity between the machine frame and true earth
ground (water pipe or similar) to ensure a good ground
connection.
Electrical Panel:
NEVER operate the grinder with the
cabinet door open.
Retained Electrical Power:
Electronic devices within the
electrical cabinet may retain dangerous electrical voltages
after the power has been removed.
Electrical Service:
Certain service and troubleshooting
operations require access to the electrical cabinet while
the electrical power is on. Only qualified electrical
technicians should perform such operations.
In preparation for installing the Tormach 2-Axis Semi-
Automatic Personal Surface Grinder PSG 612 Surface
Grinder you will need to identify a workspace that is large
enough to accommodate the machine foot print. Select a
workspace that is relatively level and away from exposure
to moisture or vibrations.
CAUTIOn: TORMACH STROnGlY
RECOMMEnDS InSTAllATIOn AnD
ASSEMBlY BE COMPlETED WITH THE
ASSISTAnCE OF AnOTHER PERSOn.
REQUIRED TOOLS AND ITEMS
During the installation process you will need the following
items:
For Lifting
•
A forklift, engine hoist, or other mechanical lifting
device rated for the weight of the machine.
•
A chain or clevis rated for at least 1500 pounds.
For Assembly
•
Machine Foot Assemblies (Included)
•
Crowbar
•
Level
UNPACKING
The Tormach PSG 612 will arrive in a shipping crate or
pallet jack designed to be moved with a forklift at the base.
UM10159_PSG612_OPERATORS_MAnUAl_0718A
6
7
UM10159_PSG612_OPERATORS_MAnUAl_0718A
Summary of Contents for PSG 612
Page 2: ......
Page 35: ...33 UM10159_PSG612_Operators_Manual_0718A...
Page 36: ...6 TORMACH INC 1071 UNIEK DR WAUNAKEE WI 53597...