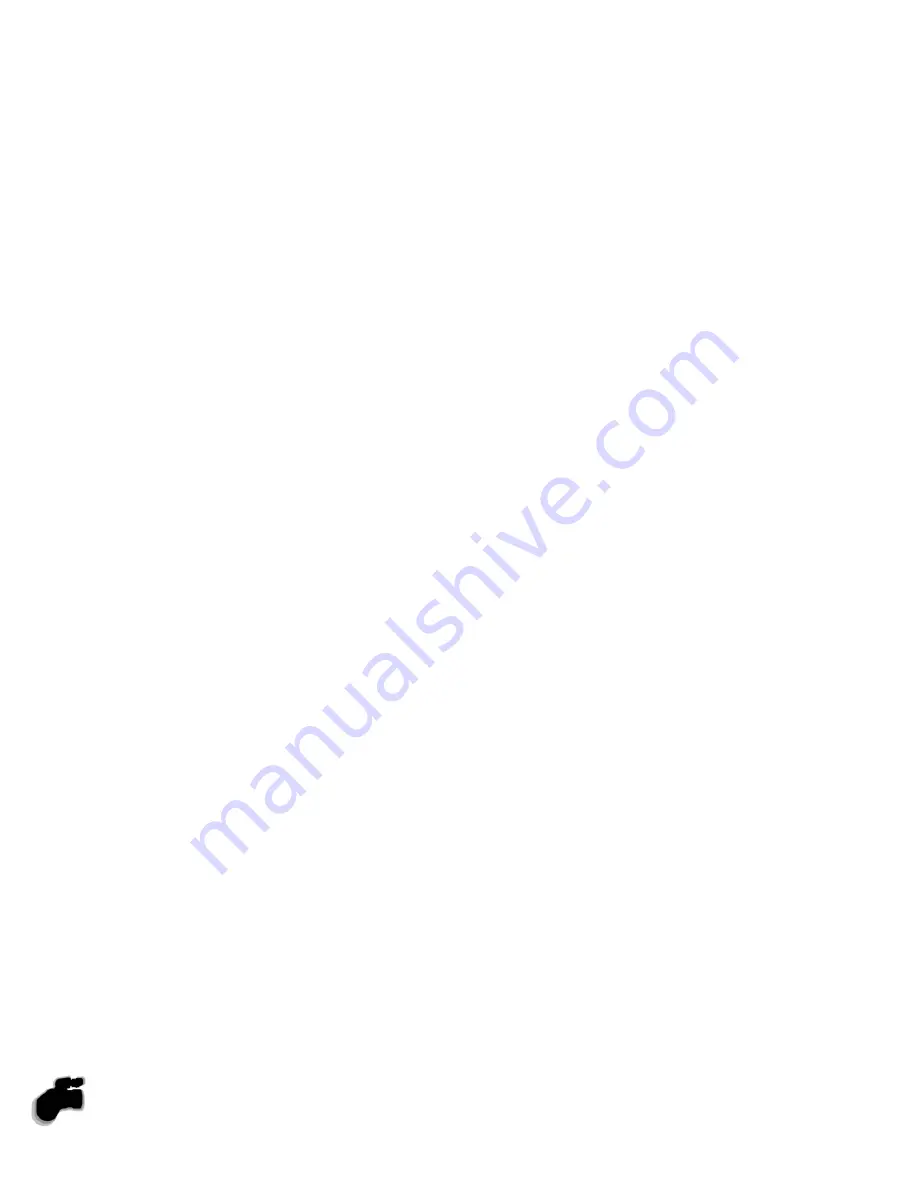
4
CONTENTS
TTZ SERIES
OPERATIONAL AND SPARE PARTS MANUAL
INTRODUCING TORC, LLC.
5
SECTION I
IMPORTANT SAFETY INSTRUCTIONS
6
SECTION II
INSTRUCTIONS BEFORE USE
8
2-1 Working Pressure
2-2 Hydraulic Connections
2-3 Electrical Connections
2-4 Air Connections
SECTION III
OPERATION
10
3-1 General
3-2 Connecting the System
3-3 Inserting the Ratchet Link
3-5 Setting Torque
3-5 Setting Pressure
3-6 Applying Torque
3-7 Operating the Torque Machine
3-8 Loosening Procedures
SECTION IV
TORC, LLC. POWER PACKS
15
4-1 General
4-2 Remote Control
4-3 Operation
SECTION V
PREVENTIVE MAINTENANCE
17
5-1 Preventive Maintenance - Torque Machines
5-2 Preventive Maintenance - Hydraulic Power Packs
SECTION VI
TROUBLESHOOTING
19
APPENDICES
23
A TTZ Tool Parts List
B TT Z Low Clearance Li nk Parts List
C TT Z Slim Link Part s List
D TTZ Dimensional Data