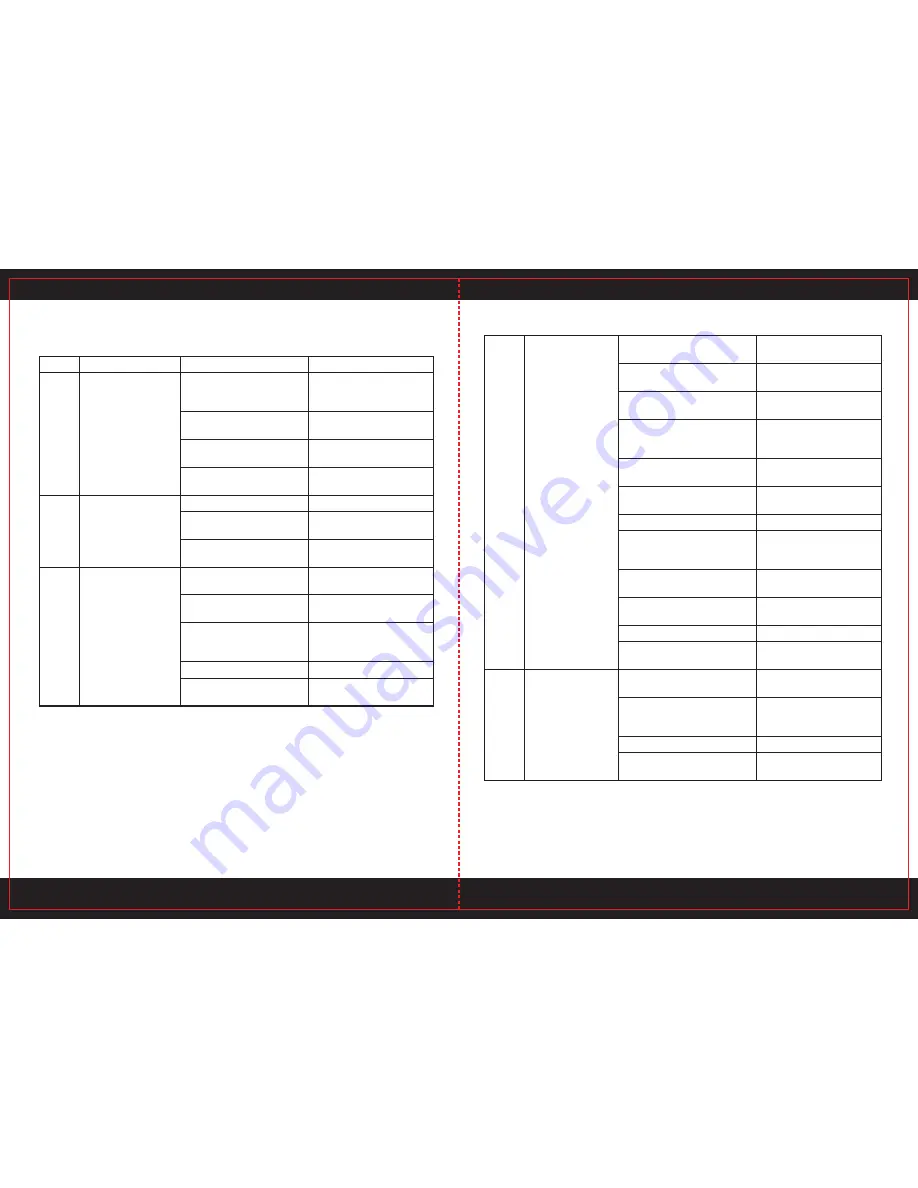
The Techniques Breakdown and Analysis
No.
Breakdown
Analysis
Solutions
1
Work piece is not cut
thoroughly
The cutting current is too
low
Adjust ‘Cutting thickness
Mode Switch’ to ‘Thick
Mode’
The cutting speed is too
rapid
Slow down the cutting
speed
Torch electrode or nozzle is
burn out
Replace electrode or noz-
zle
Cut thickness exceeds the
limit of the cutter
Replace with high-power
cutter
2
Slag drop out from
the Cutting Mouth of
Work Piece
Cutting Speed is too slow
Accelerate cutting speed
Cutting Electrode or Nozzle
is burnt
Replace electrode or noz-
zle
Cutting current is too high
Adjust cutting thickness
mode to ‘thin’ mode
3
Pilot is not stable
during operation
Compressed gas is too low
or too high
Adjust pressure
Electrode of cutting torch
or nozzle is burnt
Replace electrode or
nozzle
Connection between
cutting cable and work
piece is poor
Connect firmly
Cutting speed is too slow
Adjust speed
Input AC voltage is too low
Adjust power supply or
voltage
4
Cutting thickness is
not up to the rated
standard
Slag drop out from
the Cutting Mouth
of Work Piece
Pilot is not stable
during operation
Input compressed air pres-
sure is too low or too high
Adjust air pressure
Input compressed air flow is
too low
Adjust air flow
Cutting speed is too quick
Slow cutting speed
Material of work piece is not
symmetry with the thickness
standard
Adjust
Nozzle or electrode is burnt
Replace nozzle or elec-
trode
Nozzle type is not right
Replace with a suitable
nozzle
Cutting mouth is not vertical
Adjust cutting mouth angle
Gas leak from the gas circuit,
making the true cutting flow is
not enough
Examine and repair the
gas circuit
Input power supply is a bit
low
Adjust the power supply
Input or output lead is too
thin or pressure is too big
Widen down-lead
Cutting speed is too slow
Adjust speed
Input AC voltage is too low
Adjust power supply or
voltage
5
Cut is a bit declin-
ing
Nozzle or electrode is burnt
Replace nozzle or elec-
trode
The installation position of
nozzle and electrode is not at
the same axes
Install again correctively
Cutting speed is too high
Adjust cutting speed
Nozzle axes is not plumb with
the plane
Adjust the torch angle
17
18
Summary of Contents for POWER CUT 25K
Page 1: ......