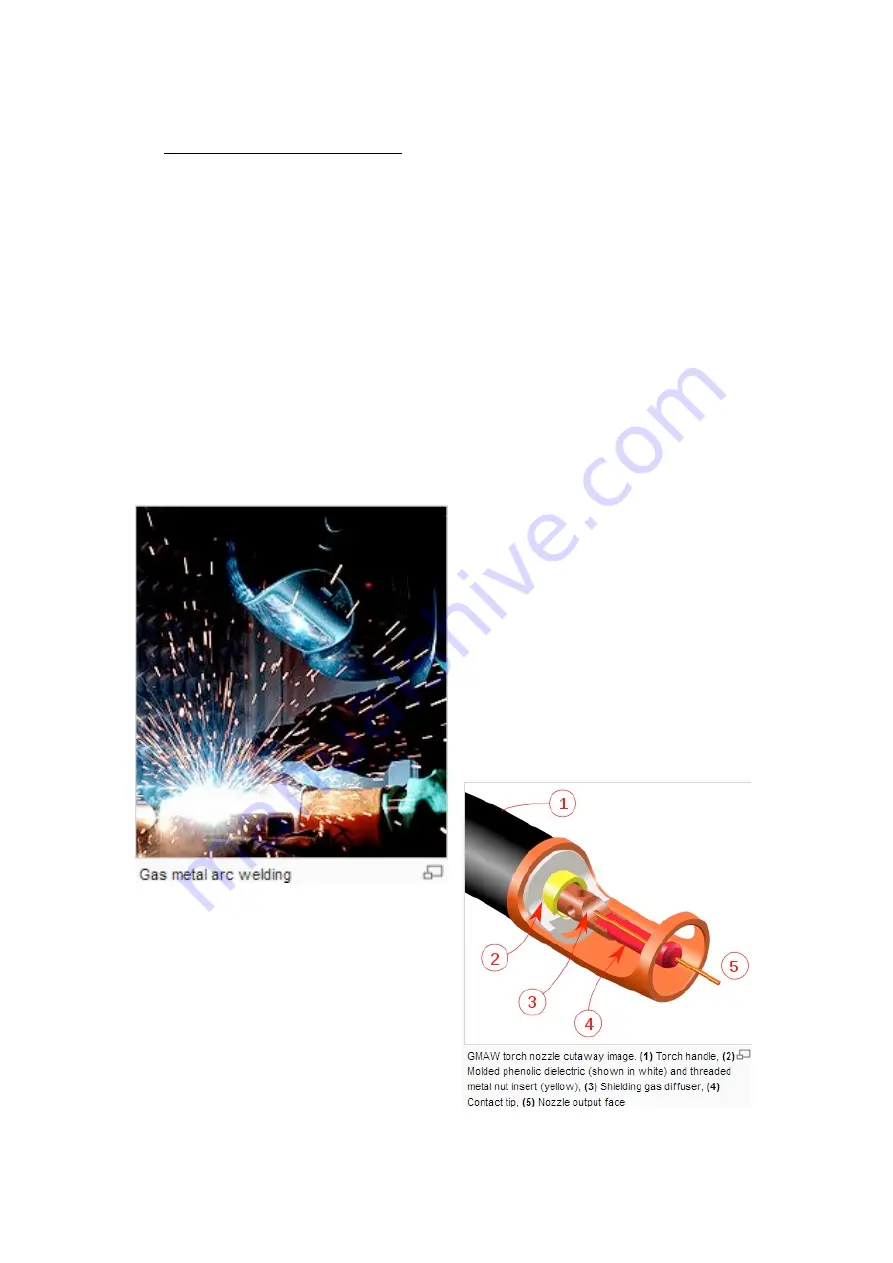
Gas metal arc welding
Gas
metal
arc
welding
(GMAW),
sometimes referred to by its subtypes
metal inert gas (MIG) welding or metal
active gas (MAG) welding, is a
semi-automatic or automatic arc welding
process in which a continuous and
consumable wire electrode and a shielding
gas are fed through a welding gun. A
constant voltage, direct current power
source is most commonly used with
GMAW, but constant current systems, as
well as alternating current, can be used.
There are four primary methods of metal
transfer in GMAW, called globular,
short-circuiting, spray, and pulsed-spray,
each of which has distinct properties and
corresponding advantages and limitations.
Welding gun and wire feed unit
The typical GMAW welding gun has a
number of key parts—a control switch, a
contact tip, a power cable, a gas nozzle,
an electrode conduit and liner, and a gas
hose. The control switch, or trigger, when
pressed by the operator, initiates the wire
feed, electric power, and the shielding gas
flow, causing an electric arc to be struck.
The contact tip, normally made of copper
and sometimes chemically treated to
reduce spatter, is connected to the
welding power source through the power
cable and transmits the electrical energy
to the electrode while directing it to the
weld area. It must be firmly secured and
properly sized, since it must allow the
passage of the electrode while maintaining
an electrical contact. Before arriving at the
contact tip, the wire is protected and
guided by the electrode conduit and liner,
which help prevent buckling and maintain
an uninterrupted wire feed. The gas nozzle
is used to evenly direct the shielding gas
into the welding zone—if the flow is
inconsistent, it may not provide adequate
protection of the weld area. Larger nozzles
provide greater shielding gas flow, which
is useful for high current welding
operations, in which the size of the molten
weld pool is increased. The gas is
supplied to the nozzle through a gas hose,
which is connected to the tanks of
shielding gas. Sometimes, a water hose is
also built into the welding gun, cooling the
gun in high heat operations. The wire feed
unit supplies the electrode to the work,
driving it through the conduit and on to the
contact tip. Most models provide the wire
at a constant feed rate, but more
advanced machines can vary the feed rate
in response to the arc length and voltage.
Some wire feeders can reach feed rates
as high as 30.5 m/min (1200 in/min), but
feed rates for semiautomatic GMAW
typically range from 2 to 10 m/min
(75–400 in/min)
Summary of Contents for MIG-200
Page 1: ......
Page 20: ...ASSEMBLY DIAGRAM The structure of ADVAN MIG 250 reference only ...
Page 26: ......