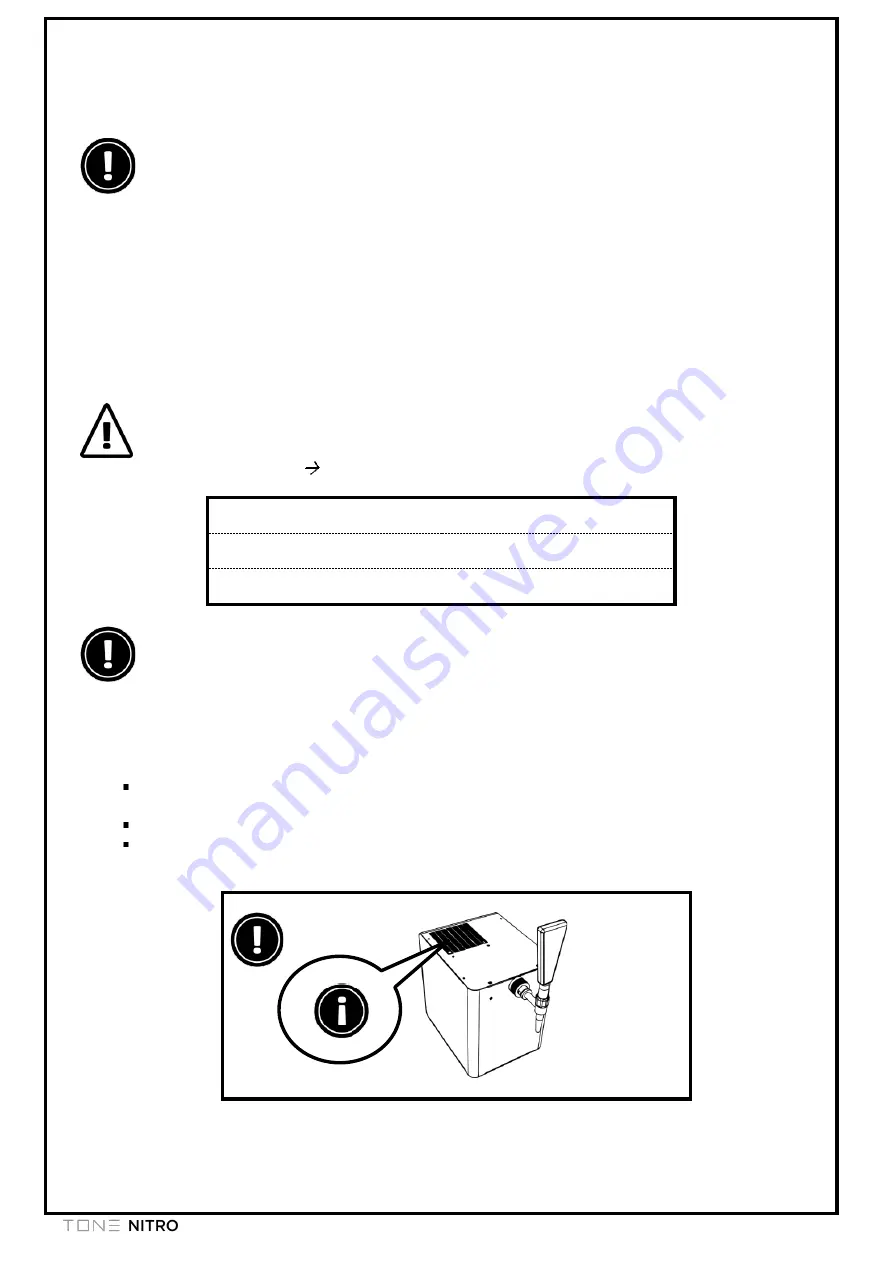
Page 7 of 39
3 REQUIREMENTS FOR THE LOCATION OF OPERATION
3.1 General requirements
The respective valid national regulations regarding the place of installation must be observed.
Since the
TONE Nitro
is basically a dispensing system, please also observe the technical
regulations for beverage dispensing systems TRSK 400 "Installation of beverage dispensing
systems".
Attention: Low voltage can damage the compressor. The same applies if several units are
supplied with power via one power connection.
The power plug must be freely accessible.
3.2 Electrical connections
see technical specification
Voltage
230 V
∼
+/- 10% 50 Hz
Power
300 W
Fuse protection
max. 16 A
3.3 Location of operation
Adequate ventilation and extraction must be ensured. For this purpose, the distance to the next
wall should be at least 30 cm.
Attention:
Never cover and/or block the air slots. Otherwise there will be insufficient cooling capacity
and the cooling system may fail.
Never place the unit near heat sources or direct sunlight.
Under no circumstances should liquid enter the upper opening of the unit, otherwise there
is a danger of short circuit!
!