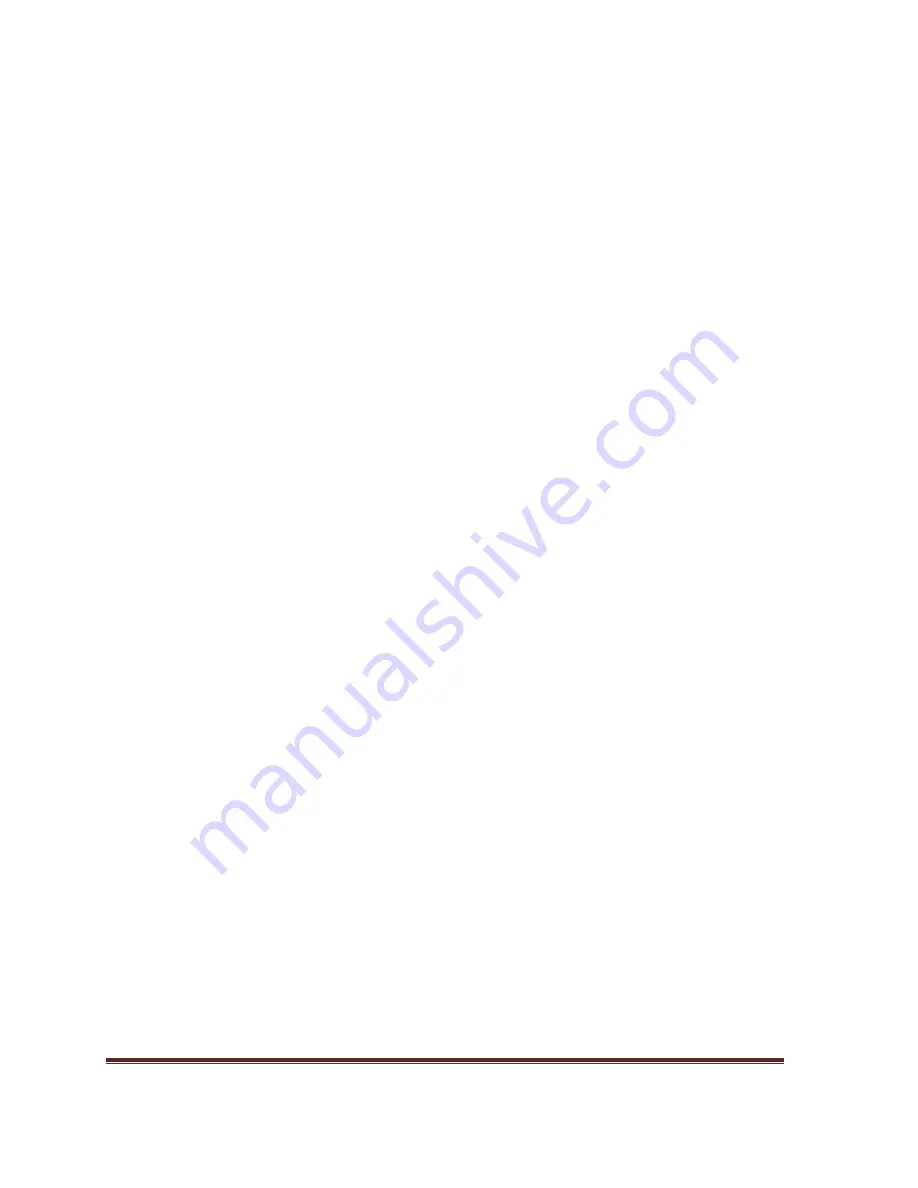
Operator’s Manual
11
Lifting
When lifting the machine, observe the following instructions:
•
Designate a skilled person to guide you for the lifting procedure.
•
You must be able to see or hear this person.
•
Use only suitable and certified hoisting gear, lifting tackle and load-bearing equipment with
sufficient lifting capacities.
•
Only use the attachment points described in the operator's manual.
•
Attach the machine securely to the hoisting gear.
•
Ensure that no one is nearby or under the machine.
•
Do not climb onto the machine.
Loading the machine
•
Loading ramps must be able to bear the load and be in a stable position.
•
Make sure that no one can be endangered if the machine slips away or tips over or if
machine parts suddenly move upward or downward.
•
Put the operating controls and moving parts in their transport position.
•
Secure the machine with load-securing straps so that it cannot tip over, fall down or slide
away. Only use the attachment points described in the operator's manual.
Transport vehicle
Use only suitable transport vehicles with sufficient load-carrying capacity and suitable
tie-down lugs.
Transporting the machine
Secure the machine on the transport device against tilting, falling or slipping. Only use the
lashing points listed in the operating instructions. Also observe the country-specific
regulations, standards and guidelines.
Restarting
Machines, machine parts, accessories or tools that were detached for transport purposes
must be re-mounted and fastened before restarting. Only operate in accordance with the
operating instructions.
2.5 Operating safety
Explosive environment
Never operate the machine in a potentially explosive environment.
Work environment
Familiarize yourself with your work environment before you start work. This includes e.g.
the following items:
•
Obstacles in the work and traffic area.
•
Load-bearing capacity of the ground.
•
The measures needed to cordon off the construction site from public traffic in particular.
•
The measures needed to secure walls and ceilings.
•
Options available in the event of an accident.