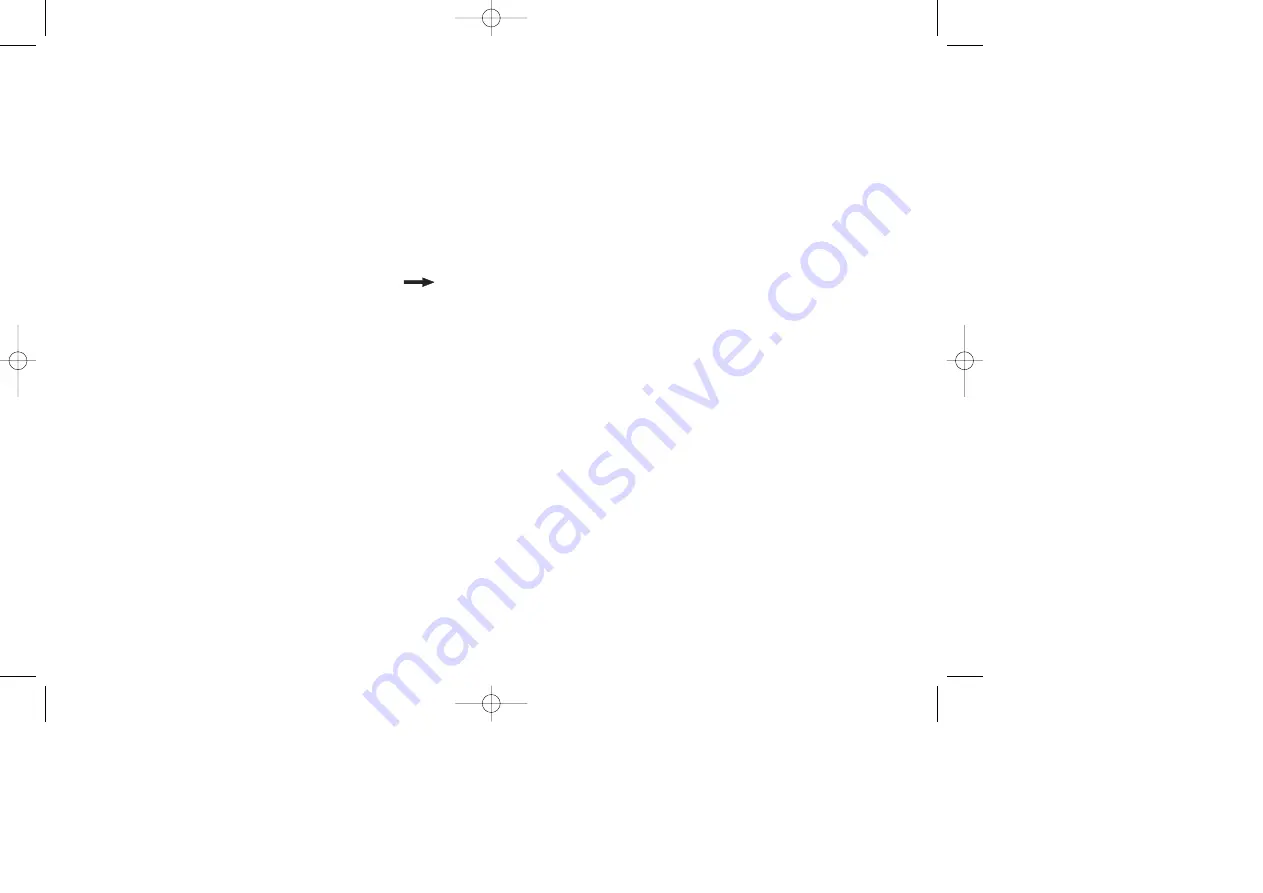
9
Safety instructions
The operator may only carry out the maintenance and repair work descri-
bed in this operating manual
Maintenance and service work not described in this operating manual
may only be carried out by trained specialists following instruction by
R
IVETEC
on the basis of the service instructions which also exist.
See
the address on
last
page for more information on service instructions
and training.
Note
The manufacturer accepts no liability for damage resulting from
incorrect repairs or the use of spare parts from other sources.
At the time of leaving the workplace, do not leave the riveting tool with
pressure on.
A guarantee is void, if any repair work carried out on the riveting tool has
lead to any damage of the riveting tool.
The riveting tool
RL
50 has been checked and manufactured according to
European guidelines. The declaration of conformity can be found on the
second last page.
Maintenance and servicing
Service instructions
Guarantee
Declaration of conformity
Ms50_gb_241001_neu.qxd 30.10.2001 9:01 Uhr Seite 9
Summary of Contents for RIVETEC RL 50
Page 44: ......