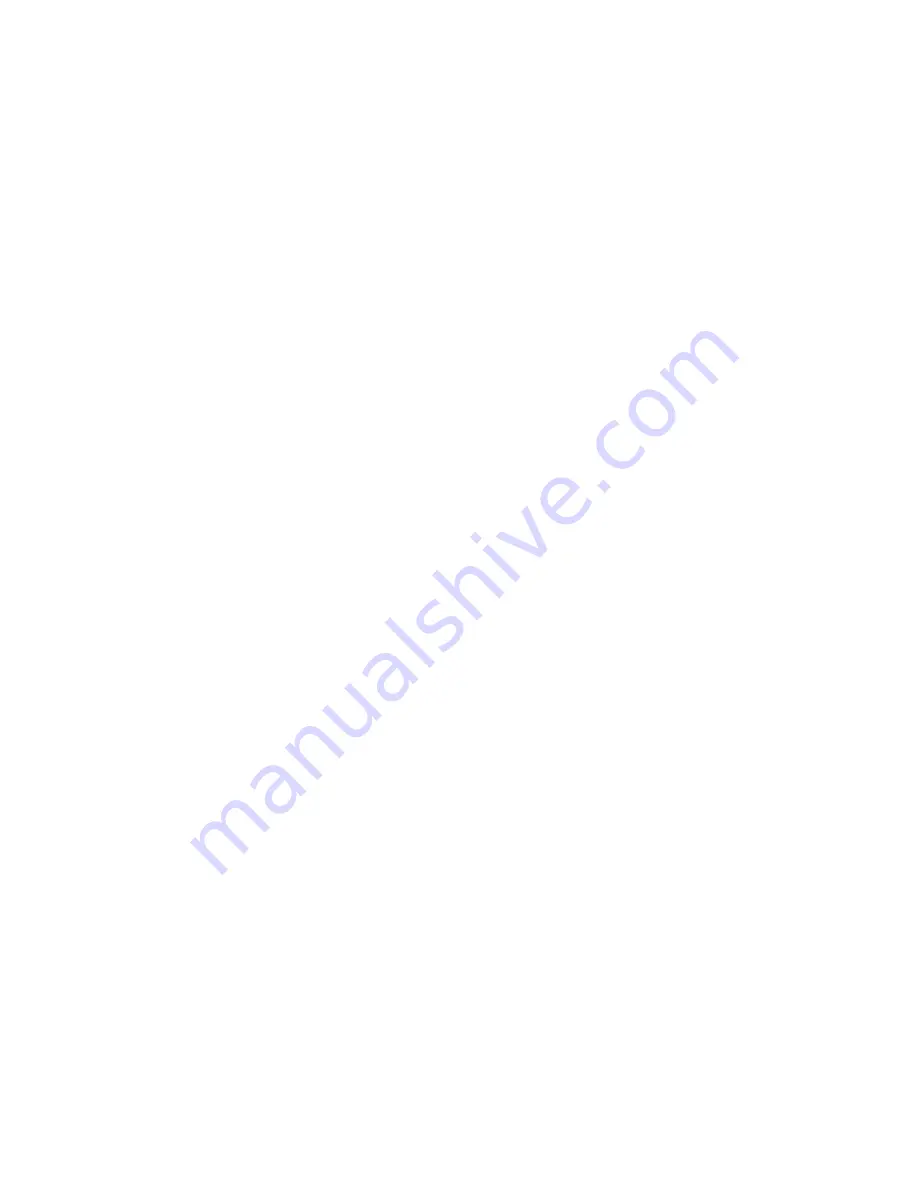
54
◆
Frequency flush (ProPAC3) is activated early because of the changes in product flow rate caused by
varying product line pressure – adjust the Flush Start (% Decrease).
15.
Additive Pulse Detection (PAC3) or No Additive Pulse (ProPAC3) is displayed.
It is possible the additive flow meter pulse counts from the Titan flow meter are not received by the
microprocessor following an injection request. This problem could cause the solenoid to remain
energized (open) for an extended period of time in an attempt to complete the injection request. If the
microprocessor does not count or detect pulses from the Titan flow meter within 30 seconds of the receipt
of a valid injection request, the alarm will activate. This condition could also cause damage to the
solenoid coil.
◆
Failure of the additive pump and motor to be permitted ON when product pulses are sent to the injector
– check pump and motor.
◆
Failure of the Hall-Effect Sensor – check 12VDC output.
◆
Failure of the additive flow meter to turn freely – check for free turning.
◆
Check flow meter connector (P16 on PAC3, P11 on ProPAC3).
◆
Loss of additive pump pressure – check pressure (125-150 PSIG).
◆
Closed Ball Valve – make sure Ball Valve is open.
◆
Check Valve installed in the wrong direction – open and check.
◆
Solenoid failure - check connector (P4 on PAC3, P3 on ProPAC3) on the motherboard.
Tips:
Open the Test Port and make a test injection. If additive pours through the injector without being
registered on the injector (batch injection shows 0.0), either the Hall-Effect sensor is bad or the meter
gears are stuck. If no additive flows through the injector, the solenoid has probably failed.
16.
Alarm High (PAC3) or Solenoid Leak Detection (ProPAC3) is displayed.
This alarm will activate when the batch count (count up from zero to the programmed Additive Set value)
exceeds 2 times the scaled Additive Set.
◆
Damaged seals in the solenoid or the presence of a foreign object inhibiting valve closure – check and
replace solenoid.
◆
Product under pressure may leak in a reverse direction through the injector additive flow meter, falsely
indicating additive flow – make sure the Ball Valve and Check
◆
Valves are installed properly.
◆
Air in the additive supply lines may cause “gear rocking” in the additive flow meter, this rocking is
registered in the injector as a leak – install a riser tube in the additive supply tubing.
◆
The microprocessor’s solid-state relay that is used to energize the solenoid control valve has failed –
use another microprocessor to test.
17.
Secondary Alarm (PAC3) or Fail Safe Alarm (ProPAC3) is displayed.
Although it is unlikely, it is possible there could be a failure of the microprocessor programming or other
event that could cause the injector to flow additive anytime the additive pump was pressurized. This
alarm circuitry is totally independent of the microprocessor and is incorporated into the design of the
motherboard. The alarm circuitry monitors the energized state of the solenoid control valve. If the
circuitry detects the solenoid has been energized continuously, for approximately 45 seconds, the circuitry
will terminate power to the solenoid, thereby, terminate the flow of additive.
◆
Failure of the microprocessor – check and replace microprocessor.
18.
No Product Pulse (ProPAC3) is displayed.
When the microprocessor detects a permissive input and flow switch input, and does not receive a product
pulse input within 120 seconds, the alarm will activate.
◆
Failure of Input Modules – check Input Module 1, 2 and, 3. Make sure the product pulse is within the
specifications for the high/low voltage (AC or DC voltage) and frequency for the Input Module.
Summary of Contents for ProPAC-3
Page 39: ...39 ...