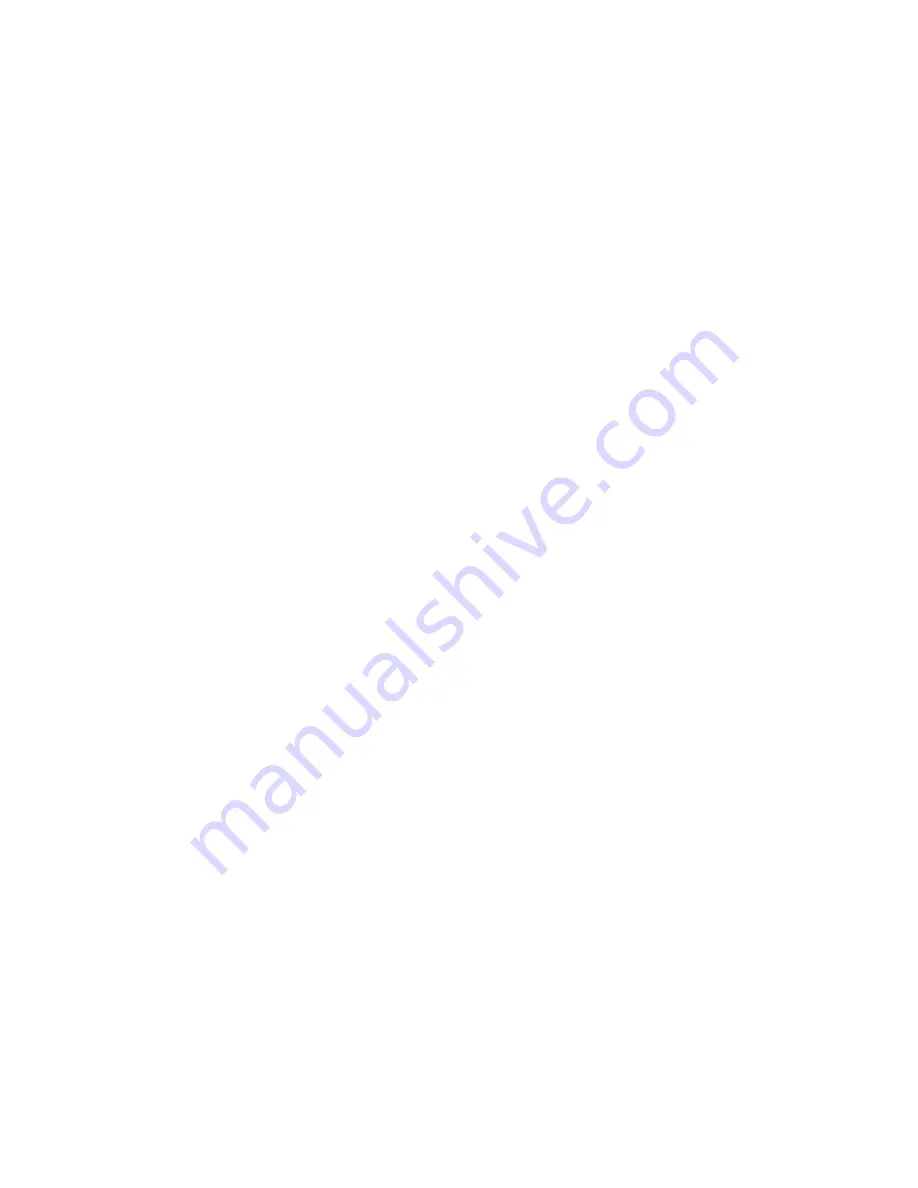
53
10.
Inconsistent calibration.
◆
Flow meter gears damaged – inspect and replace gears.
◆
Improper calibration check procedure – read Section 4 Field Calibration Instructions.
◆
Inconsistent pressure differential during calibration test – make sure the differential does not fluctuate
greatly during calibration test
11.
Power is applied to the injector, but the display does not light up.
◆
AC wiring incorrect – check power and ground wiring. Check power on other injectors.
◆
Auto Switch is in “Off” position – make sure the switch is in “On” position.
◆
Fuse (Fuse1) on the motherboard has blown – check and replace the fuse.
◆
Loose AC Connector (P1 on PAC3, P4 on ProPAC3) on the motherboard – check connector.
◆
Loose Switch Connector (P2 on PAC3, P5 on ProPAC3) – check connector.
◆
The microprocessor is not inserted properly – check connection.
◆
The microprocessor Display unit has failed – replace other microprocessor for test.
12.
The PAC3/ProPAC3 Display is on, but the injector does not inject.
Press the injector Test Button, if the unit injects properly, then look for the following:
◆
During loading – check if the LED on the Input Module is blinking. Make sure the product pulse is
within the specifications for the high/low voltage (AC or DC voltage) and frequency for the Input
Module.
◆
Loss or reduced additive pump pressure – check pump pressure (125-150 PSIG typical)
◆
Closed Ball Valve on injector or at the rack – open it.
◆
Solenoid not energized properly – check connector (P4 on PAC3, P3 on ProPAC3) on the motherboard.
◆
The flow meter gears are not turning freely – check for free turning.
◆
Solenoid Control Valve coils failed – check the AC voltage to the coil.
13.
Alarm Low Flow1 (PAC3) or Additive Flow Problem (ProPAC3) is displayed.
Conditions whereby additive flow is occurring, but at a reduced flow rate. It is likely a second injection
request may be received by the PAC3/ProPAC3 microprocessor, while the injector is attempting to
complete a previous injection request. If the injector is unable to complete 3 consecutive injection
requests, the alarm will activate. Anytime the solenoid is energized continuously for > 30 seconds,
thereby, attempting to complete just one injection request, the injector will activate the alarm.
◆
Reduced additive pump pressure – check pressure (125-150 PSIG typical) when several injectors are in
used simultaneously.
◆
Closed or restricted Ball Valve – make sure Ball Valve is fully open.
◆
Additive viscosity too high – check viscosity curves.
◆
Strainer clogged – check strainer with power off and pressure removed.
14.
Alarm Low Flow2 (PAC3) or Additive Quantity Alarm (ProPAC3) is displayed.
Although it is unlikely, it is possible an under injection of additive can be made, without the injector
entering Alarm Low Flow1 or Additive Flow Problem. This feature detects the actual quantity of additive
injected over a programmed number of injection requests (cycles) and compares the actual quantity with
the calculated quantity. Note: ProPAC3 allows the user to program Additive Quantity Low % and High
% meanwhile PAC3 only allows Low %.
◆
Additive Pre-Load (ProPAC3) feature is enabled and the product load is terminated soon after the start
of the product load. Under this condition, the additive quantity may be high (depending on the program
setting for the Quantity High %) – unpredictable.
◆
Excessive product is flushed (ProPAc3) at the end of a load. This condition may adversely affect the
additive/product ratio by making the additive quantity out of programmed specifications – make sure the
amount of Flush Volume entered matches the actual volume from the injection point to the end of load
arm.
Summary of Contents for ProPAC-3
Page 39: ...39 ...