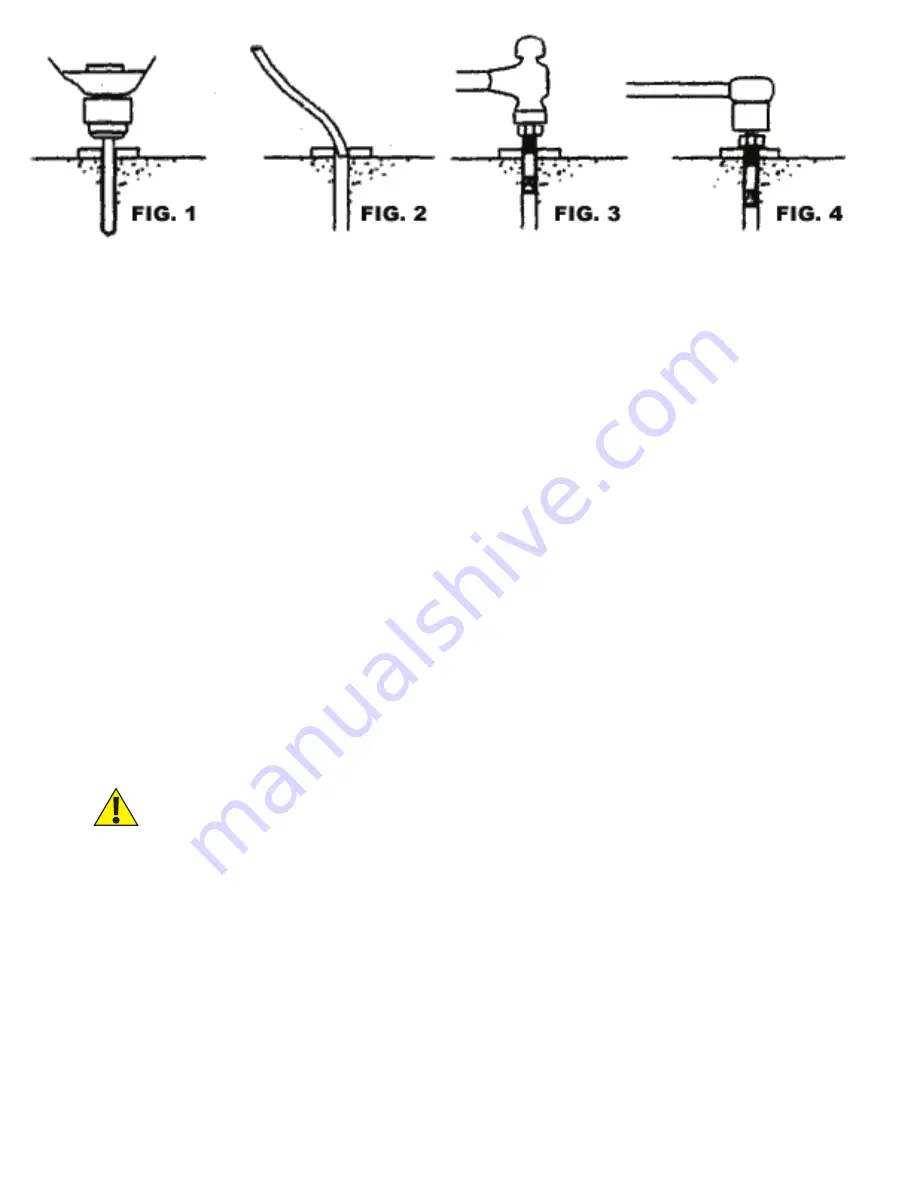
7
4.3 ANCHORING TIP SHEET
1.
Use a concrete hammer drill with a carbide tip, solid drill bit the same diameter as the
anchor, 3/4”. (.775 to .787 inches diameter).
Do not use excessively worn bits or bits
which have been incorrectly sharpened.
2.
Keep the drill perpendicular to the concrete while drilling.
3.
Let the drill do the work. Do not apply excessive pressure. Lift the drill up and down
occasionally to remove residue to reduce binding.
4.
Drill the hole for anchor bolt completely through the concrete. If an error is made during
the installation of these anchors, this will allow for the anchor bolt to be driven down
into the ground, so that a new anchor may be installed in place (fig.1).
5. Be sure to clean all dust from hole.
(fig. 2).
6. Place a flat washer and hex nut over threaded end of anchor, leaving approximately 1/4
inch of thread exposed above the nut (fig.3). Carefully tap anchor into the concrete until
nut and flat washer are against base plate. Be sure to only tap the top of the anchor and
not the nut. This could cause damage to the threads of the anchor.
7. Tighten the nut (fig. 4) to
85 ft-lbs
of torque.
DO NOT USE AN IMPACT WRENCH TO TIGHTEN ANCHORS!
Summary of Contents for HD4P-12000
Page 27: ...23 LIFT WILL NOT RAISE...
Page 28: ...24 MOTOR WILL NOT RUN...
Page 29: ...25 LIFT WILL NOT STAY UP...
Page 30: ...26 WILL NOT RAISE LOADED LIFT...
Page 31: ...27 LIFT LOWERS SLOWLY OR NOT AT ALL...
Page 32: ...28 8 DIAGRAMS PARTS LIST FIG 1 85...
Page 35: ...31 FIG 4...
Page 36: ...32 FIG 5...
Page 40: ...36...
Page 42: ...NOTES...
Page 43: ...NOTES...