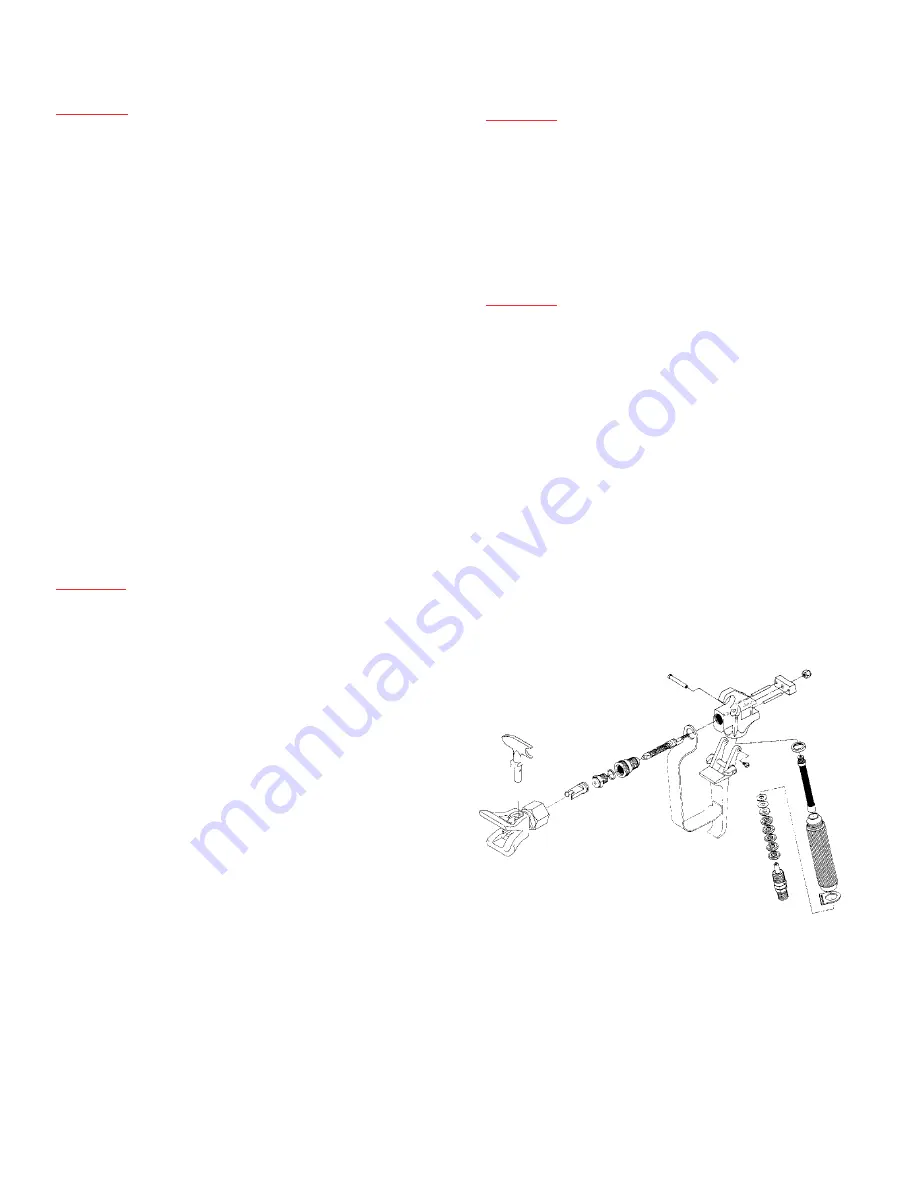
Pressure Switch Replacement
See Figure 7
WARNING:
Before proceeding, follow the Pressure
Relief Procedure outlined on page 5. Additionally, follow
all other warnings to reduce the risk of an injection
injury, injury from moving parts or electric shock.
1. Remove socket head cap screws.
2. Remove electrical cover plate #60, located near pressure
switch and disconnect two red wires from clutch starter
#58. See pg. 20.
3. Remove screw #27 from pressure switch adjustment
knob and slide knob off.
4. Remove screw #27 located on side of gear box housing
#53 and using a 1/8" allen wrench remove set screw
#56, until pressure switch #231 is able to slide down
through. Feed electrical wires down at the same time.
5. Insert new switch assembly #231). See Figure 8, p. 22)
into housing while carefully working the wires into the
switch box. Using needle nose pliers, reconnect wires
to motor starter.
6. Making sure that the switch assembly is fully inserted,
tighten set screw #56 with a 1/8" allen wrench until the
switch assembly is secure. Reattach adjustment knob
#26. See pg. 20.
7. Inspect O-Rings #232 and #233 on switch assembly.
8. Install insulator plate #66 and plate #60. See pg. 20.
9. The pressure switch is factory calibrated so no
adjustment is required.
Service/Replacement of the
Pressure Relief Prime Valve
WARNING:
Before proceeding, follow the Pressure Relief
Procedure outlined on Page 5. Additionally, follow all
other warnings to reduce the risk of an injection injury,
injury from moving parts or electric shock.
1. Remove the Dowel Pin (#226) from Bypass Valve Handle
(#227).
2. Remove Handle (#227) and Bypass Cam (#225).
3. Using a wrench, loosen Bypass Housing (#218) and
unscrew.
4. Unscrew Bypass Retainer (#224) and remove Bypass Valve
Stem (#220).
5. Inspect ball on end of Stem (#220) and O-Ring (#219). Clean
or replace if worn.
6. Screw completed assembly into Filter Block (#207). Tighten
securely with wrench.
7. Install Bypass Cam (#225) over Bypass Retainer (#224),
lubricate with grease. Line up Dowel Pin (#226) on Cam
(#227) with hole on Filter Block (#207).
8. Using Dowel Pin (#226) line up Stem (#220) with hole on
Handle (#227). Secure Handle with Dowel Pin (#226).
9. IMPORTANT: If Handle (#227) rotates 360° check Pin on
Cam (#225).
Service / Replacement
of Filter
WARNING:
Before proceeding, follow the Pressure Relief
Procedure outlined on Page 5. Additionally, follow all
other warnings to reduce the risk of an injection injury,
injury from moving parts or electric shock.
PUMP FILTER
1. Unscrew Filter Housing (#202).
2. Remove Filter Cartridge (#204). Clean or replace.
3. Inspect O-Ring (#206). Clean or replace.
4. Reattach Filter Housing (#202).
Gun Filter
WARNING:
Follow all safety precautions as described in
high pressure warning section before proceeding. If your
spray gun leaks or spits at the tip when you release the
trigger, the needle or seat is dirty, worn or damaged and
must be cleaned or replaced.
Replacement or Removal of Filter:
1. First pull down on trigger safety guard and swing away from
handle.
2. Unscrew handle from spray head.
3. Unscrew left hand threaded* filter from spray head. (*NOTE:
Left handed thread requires turning the filter clockwise to
remove.)
4. Screw new or cleaned filter into the head. (To reinstall left
hand thread turn counterclockwise.)
5. Reattach handle to head and secure safety trigger guard.
(NOTE: If filter breaks off in the head use a small wood
screw to remove.)
Figure 9 For more detail, part number information and assembly
drawings at larger scale, please see the LX-80 Professional
Airless Gun Owner’s Manual (#313-012).
23