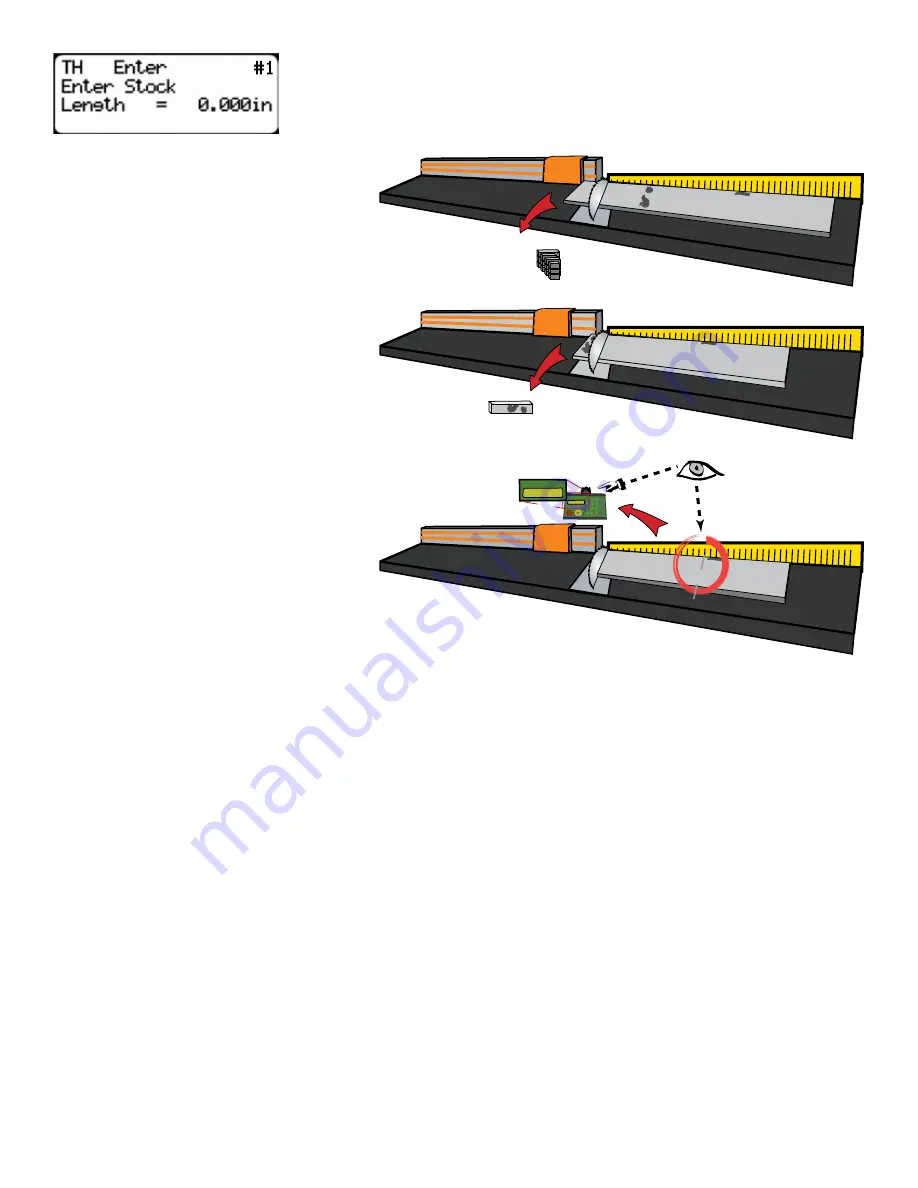
31
TigerStop
TigerStop
TigerStop
TigerStop
30in
26.5in
1 0
2 0
3 0
4 0
5 0
6 0
7 0
30
START
1 0
2 0
3 0
4 0
5 0
6 0
7 0
1 0
2 0
3 0
4 0
5 0
6 0
7 0
2. TigerRack will ask you to enter the stock length. Enter what you
measured and press [Start].
3. TigerRack will optimize the
material up to the defect and will
use as much of the material as
mathematically possible.
Note: If you are using the Standard
Interconnect Kit, TigerRack will move to the next
part length when tool cycle is complete.
4. Cut out your defect.
5. TigerRack will once again ask you
to enter the stock length. Measure
up to the next defect, enter this
measure and press [Start].
Note: If no defect is present, measure up to the
end of the material.
6. TigerRack will optimize the material up to the defect and will use as much of the material as
possible.
7. Continue in this fashion until the entire stock is used. If you have more parts to cut, start at step 1
with a new piece of material.
Why Use BackBoard Defecting & Optimizing?
• Dynamic Optimization
™
determines the best use of material, so the operator (unskilled worker or pro
fabricator) only has to focus on feeding parts and cutting.
• TigerRack moves to the correct position up to .008” so the operator never has to use a tape
measure or set a manual stop ever again.
• TigerRack reduces station setup time between different cut lengths and allows the operator to
optimize for defects like forklift stabs, shipping damage, dents, or aesthetic blemishes, while getting
optimal yield.
• TigerRack increases accuracy. The operator doesn’t have to worry about cutting errors or the
associated costs of rework. Quality control concerns are no longer a bottleneck.
• Dynamic Optimization
™
reduces scrap waste and shelving costs. Purchase less raw footage while