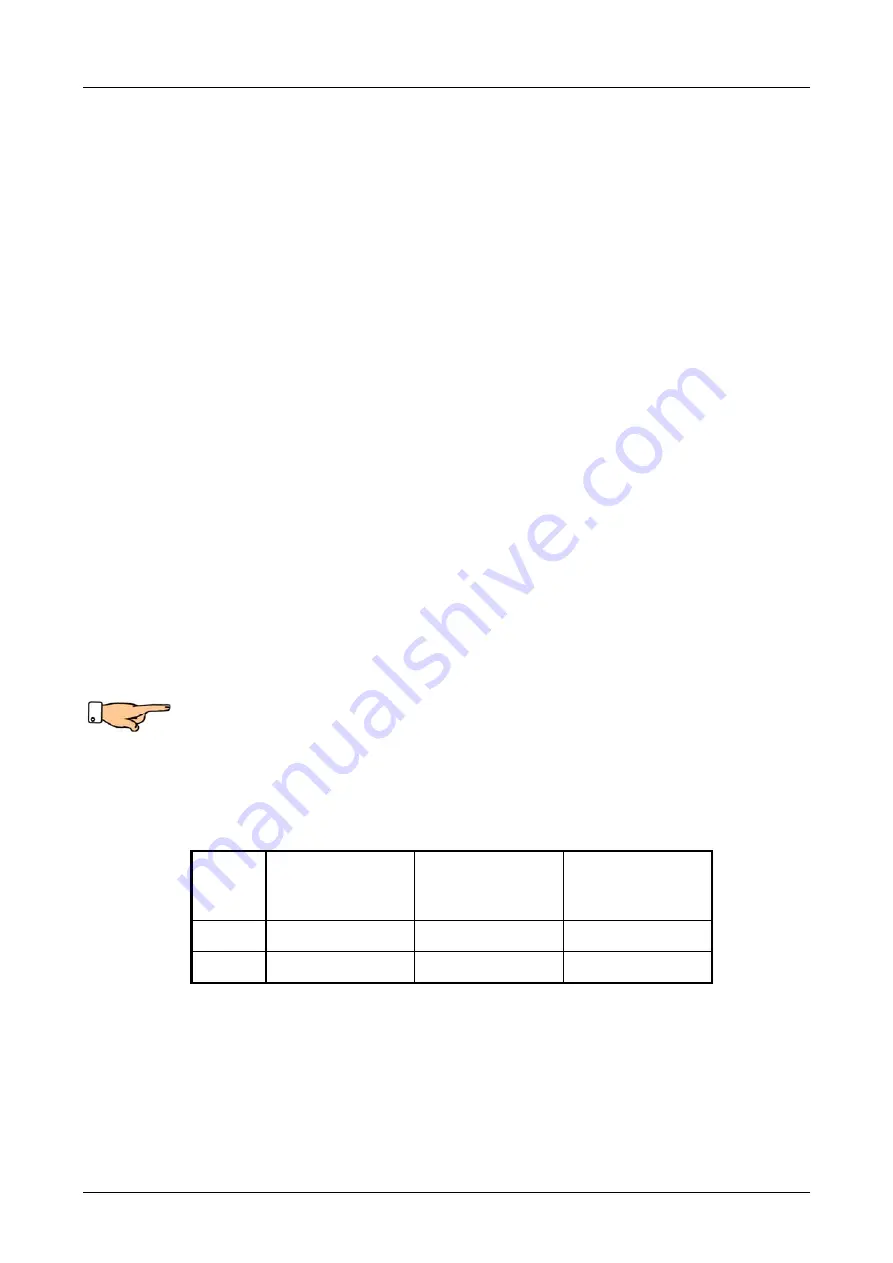
O
PERATING
M
ANUAL
6. S
ERVICING
ThyssenKrupp Aufzugswerke GmbH
45
Issue 06.2004
b) Testing of both brake circuits
When a brake circuit is tested individually, activate emergency stop operation
and repeat testing for
both brake circuits
.
Deceleration must fall below the stopping distance of the single circuit tests !
c) Inspection of wearing condition:
Put a feeler gauge between coil body and armature disk and check air gap.
The brake must be closed (coils de-energized).
Repeat several times at the circumference.
This method only applies to the front brake which is easily accessible. The
second brake is mounted recessed in the bearing bracket.
Testing the air gap at the second, recessed mounted brake:
Screw the enclosed hexagon screws M8 x 150 (marked red) into
8.4 mm
∅
holes at the brake front (see fig.15 pos. 11). Screw in until the
distance between the screwhead and the support is approx. 1-3 mm.
Attach dial gauge and holder at the brake and vertically align the dial gauge
towards the screwhead. (See fig. 15)
Energize brake circuit to be tested shortly several times and read screw
stroke at dial gauge. (The stroke corresponds to the airgap at the front
brake).
Afterwards
remove
screws and reposit.
Replace brake as soon as the max. limit air gap is reached. Repairs to
be performed at the factory!
Discription of brake replacement see chapter 7.5.
Note:
the electro magnet may fail to attract the armature base plate properly
and without delay if the air gap is too large. This means that the brake opens
delayed or fails to open.
Never tighten the red screws (fig.15, pos. 11). Remove the screws before
operation is started. In case of disregard the brakes cannot be closed!
Table air gap brake
Typ
Rated torque
for 2 brake
circuits
Rated air gap
Braked
complete
Limit air gap
Braked
complete
1250
2500
Nm
0.35 mm
± 0,1
max.
0.6
mm
1700
3400
Nm
0.35 mm
± 0,1
max.
0.7
mm
Rated air gap
brake closed (at zero current), new lining
Limit air gap
brake closed (at zero current), worn off lining
Summary of Contents for Mini gearless DAF270
Page 2: ......
Page 4: ......
Page 58: ...OPERATING MANUAL 8 ANNEX ThyssenKrupp Aufzugswerke GmbH 58 Issue 06 2004...
Page 62: ...OPERATING MANUAL 8 ANNEX ThyssenKrupp Aufzugswerke GmbH 62 Issue 06 2004...
Page 63: ...OPERATING MANUAL 8 ANNEX ThyssenKrupp Aufzugswerke GmbH 63 Issue 06 2004...
Page 64: ...OPERATING MANUAL 8 ANNEX ThyssenKrupp Aufzugswerke GmbH 64 Issue 06 2004...
Page 65: ...OPERATING MANUAL 8 ANNEX ThyssenKrupp Aufzugswerke GmbH 65 Issue 06 2004...
Page 67: ...OPERATING MANUAL 8 ANNEX ThyssenKrupp Aufzugswerke GmbH 67 Issue 06 2004...
Page 68: ...OPERATING MANUAL 8 ANNEX ThyssenKrupp Aufzugswerke GmbH 68 Issue 06 2004...
Page 69: ...OPERATING MANUAL 8 ANNEX ThyssenKrupp Aufzugswerke GmbH 69 Issue 06 2004...
Page 71: ...OPERATING MANUAL 8 ANNEX ThyssenKrupp Aufzugswerke GmbH 71 Issue 06 2004...
Page 73: ......
Page 74: ......
Page 75: ......