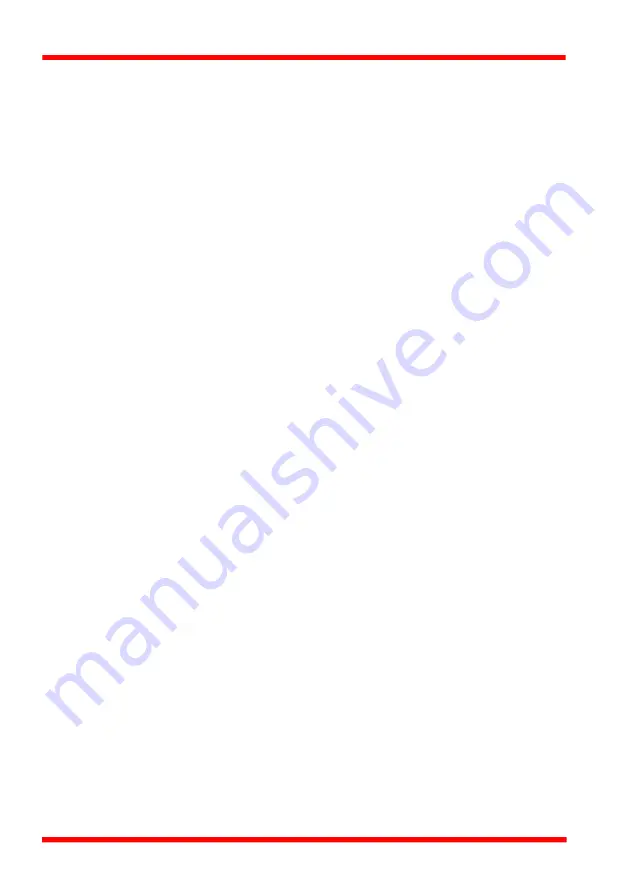
24
HA0368T Rev C May 2019
Chapter 4
4.5 Operation From The Top Panel
The following brief tutorial guides the user through a typical series of operations.
4.5.1 Preparation
1) Connect a solenoid actuated device (e.g. a Thorlabs SH05 Shutter) to the
‘SOLENOID’ connector on the rear panel of the unit.
2) Connect the INTERLOCK jack plug - see Section 3.4.2.
3) Connect the unit to a +15V DC power supply unit (PSU) - see Section 3.3.2.
4) Connect the unit to the PC USB bus
5) Switch ON the power to the PSU.
6) Turn ON the keyswitch.
4.5.2 Manual Mode
1) Select Manual mode (see Section 4.4.2.).
2) Move the wheel upwards. The SH05 shutter opens.
3) Move the wheel down. The SH05 shutter closes.
4.5.3 Single Mode
1) Select Single mode (see Section 4.4.2.).
2) Move the wheel upwards. The SH05 shutter opens for the time set in the ON time
menu option, (see Section 4.4.3.) then closes. If the wheel is moved down before
the ON time is completed, the SH05 shutter closes and the remaining ON time is
ignored..
4.5.4 Auto Mode
1) Select Auto mode (see Section 4.4.2.).
2) Move the wheel upwards. The SH05 shutter begins to open and close. Unless the
default settings have been changed, the following settings apply:
ON (Open) time: 1s
OFF (Closed time: 1s
Number of Cycles: 0 (i.e. infinite)
See Section 4.4. for more information on these settings.
3) Move the wheel down. The SH05 shutter closes.
4) Turn OFF the keyswitch.
5) Switch OFF the power to the PSU.