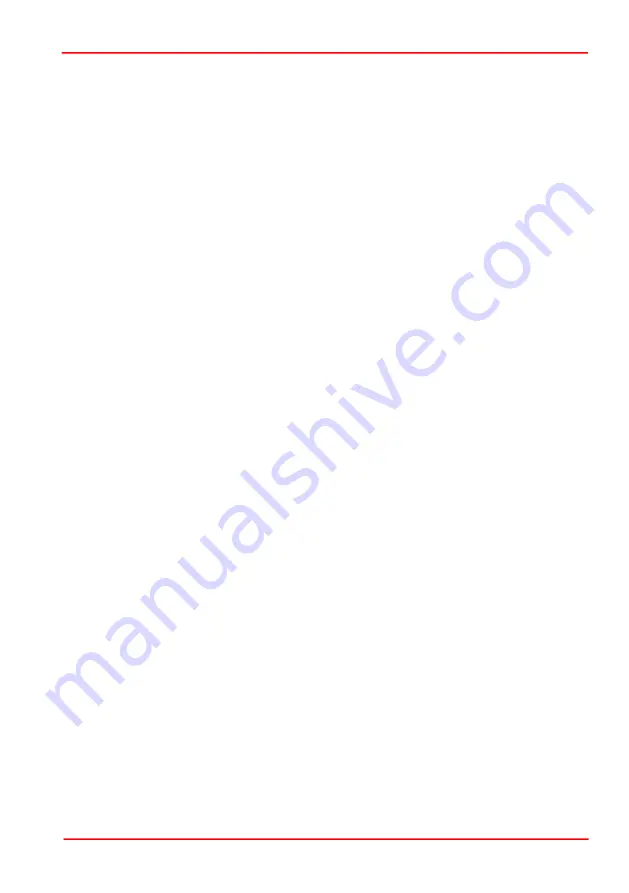
Rev D Mar 2020
Page 0
Appendices
Appendix A Rear Panel Connector Pinout Details .................................... 49
Appendix B Preventive Maintenance ......................................................... 50
Appendix C Specifications........................................................................... 51
Appendix D Piezo Operation - Background ............................................... 53
Appendix E Regulatory ................................................................................ 56
Appendix F Thorlabs Worldwide Contacts ................................................ 58